Definição
Dentre os desafios enfrentados por empresas que buscam aumentar sua capacidade, modernizar sua estrutura ou ainda obter uma melhor localização, está a transferência de sua unidade fabril atual para sua nova localização, seja ela situada na mesma cidade ou em um local distante.
Realizar a transferência de todo o material de estoque de uma unidade fabril para uma nova planta produtiva, sem que haja dano ao material ou perda e garantindo sua rastreabilidade durante toda sua movimentação requer planejamento e organização.
Cada etapa do projeto de transferência que será apresentada a seguir é fundamental para o sucesso de sua execução. Além disso, o projeto de transferência de plantas produtivas é desenvolvido com base na filosofia Lean Logistics que, em essência, visa identificar em qualquer processo as atividades que agregam valor aos clientes e eliminar os desperdícios, proporcionando alta velocidade e fluxo de materiais e informações.
Etapas
A realização de um projeto de transferência de plantas produtivas compreende as seguintes etapas:
- Mapear os padrões de itens: nesta primeira etapa, devem ser definidos os padrões de itens de acordo com a armazenagem atual do material, as dimensões e o peso estimado dos itens e os requisitos de embalagem e transporte.
- Definir modais de embalagem e de identificação por padrão de item e método de embalagem: para cada padrão de item identificado na etapa anterior, devem ser definidos os métodos e os materiais de embalagem adequados para o empacotamento dos itens e a melhor forma de identificação.
- Ambientar e treinar equipes: as equipes devem ser treinadas no processo de inventário, na identificação dos padrões de itens mapeados e nos métodos de trabalho definidos, conforme as instruções de trabalho elaborados.
- Inventariar os itens: para garantir a acuracidade do estoque antes do processo de transferência, os itens devem ser inventariados e os ajustes necessários devem ser realizados, conforme o procedimento da empresa.
- Definir e identificar as posições de armazenagem na nova planta: considerando que as estruturas de armazenagem da nova planta produtiva estarão disponíveis, devem ser definidas as alocações dos itens conforme a nova lógica de endereçamento e devem ser identificados as novas localizações.
- Empacotar, faturar e carregar os itens: após o inventário, os itens devem ser embalados e identificados conforme os modais de embalagem definidos na segunda etapa. Em seguida, deve ser realizado o faturamento dos itens para que possam ser carregados.
- Transportar os itens: de posse das notas fiscais eletrônicas, os itens podem ser carregados no veículo e enviados à nova unidade da empresa.
- Descarregar e alocar nos endereços da nova unidade fabril: na etapa final, os itens recebidos da antiga planta produtiva devem ser descarregados, conferidos e armazenados em suas novas posições, conforme a lógica de endereçamento estabelecida.
Benefícios
Um projeto de transferência de plantas produtivas realizado com excelência apresenta os seguintes benefícios:
- Adequado acondicionamento dos itens com diferentes modais de embalagem, evitando a ocorrência de danos aos materiais durante sua movimentação.
- Dimensionamento exato dos modais de embalagem necessários, evitando o desperdício ou sobra de material de embalagem para o acondicionamento dos itens.
- Realização da transferência sem perda de itens.
- Rastreabilidade dos itens durante todo o processo de transferência.
- Realização do processo de transferência dentro do cronograma previsto.
- Alocação dos itens nas posições estabelecidas da nova planta produtiva conforme lógica de endereçamento previamente elaborada.
Aplicação
A seguir, é apresentado um exemplo de aplicação de Projeto e Execução de Transferência de Plantas Produtivas.
Etapa 1 – Mapeamento dos padrões de itens
Inicialmente, foi realizado o mapeamento físico de todos os Departamentos da empresa que seriam transferidos, desde a matéria-prima até o produto acabado, para posterior definição dos modais de embalagem e da estratégia de transferência entre as unidades. Durante o mapeamento, foram identificados os padrões de itens, conforme o tipo de armazenagem atual, as dimensões e os pesos estimados dos itens e os requisitos de embalagem e transporte, por exemplo, itens que apresentam elementos de rosca ou vedação e necessitam de cuidados especiais.
Na planta produtiva mapeada, foram identificados itens armazenados em prateleiras, em Bins plásticos de diferentes tamanhos, em caixotes de madeira e em paletes, distribuídos no piso e em estruturas de armazenagem (itens de grande porte). Os padrões de itens mapeados estão listados no quadro a seguir.
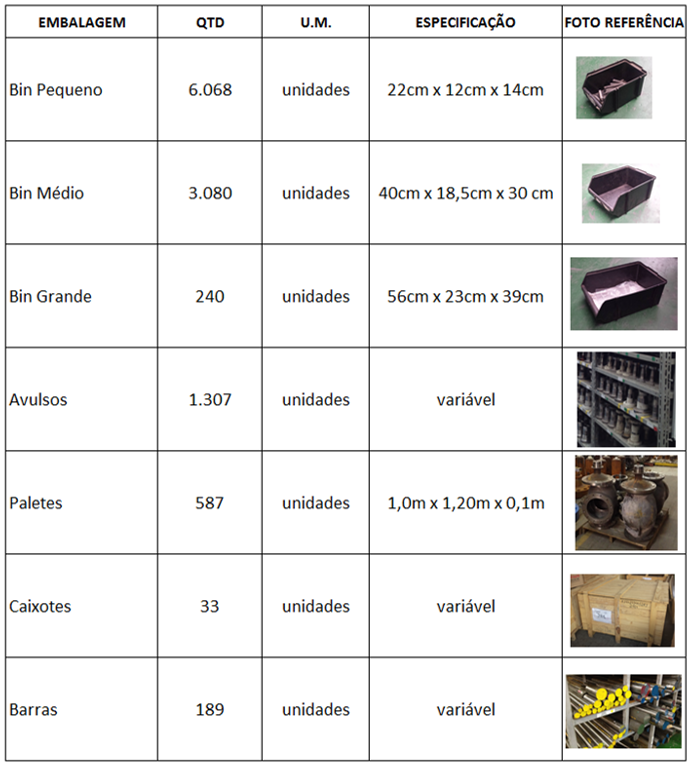
Etapa 2 – Definição dos modais de embalagem e de identificação por padrão de item e do método de embalagem
Após o mapeamento físico, foi possível definir os modais de embalagem, atentando-se às particularidades de cada item e à proteção necessária durante o processo de transferência. Além disso, foram definidas as formas de identificação de cada padrão de item, fundamental para garantir a rastreabilidade do item e evitar que ocorram perdas durante o processo de transferência.
Para cada padrão de item, também foi definido o método de trabalho adequado para garantir que os modais de embalagem e de identificação protejam os materiais e permaneçam nos itens durante todo o processo de transferência. Para isso, foram elaboradas instruções de trabalho para cada modal de embalagem, conforme exemplificado na afigura a seguir.
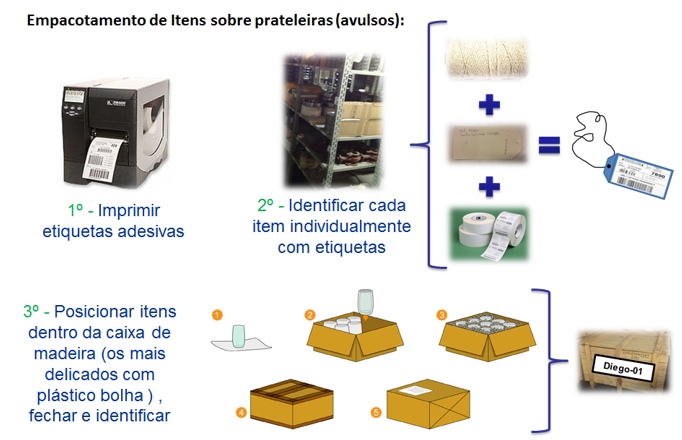
Em seguida, foi dimensionada a necessidade de material de embalagem para cada padrão de item e, com base no mapeamento físico, foram calculadas as quantidades necessárias de cada material para o empacotamento de todos os itens.
Durante esta etapa, também foi definido o tipo de veículo que seria utilizado para realizar o transporte dos materiais. Além de verificar a opção mais rentável, foram considerados os requisitos dos materiais a serem transportados, a capacidade dos veículos e as docas para a realização do carregamento e descarregamento.
Após a definição do tipo de veículo que seria utilizado para realização do transporte, foi possível estimar o número de viagens necessárias para a realização da transferência entre as plantas produtivas.
Etapa 3 – Ambientação e treinamento de equipes
Antes de iniciar o inventário, foram elegidas as equipes responsáveis por executar o inventário dos itens e por embalar e carregar os materiais na planta produtiva atual e as equipes responsáveis por descarregar e armazenar os itens na nova planta produtiva.
Em seguida, as equipes foram capacitadas no processo de inventário e no processo de transferência por meio das instruções de trabalho. Além disso, os integrantes das equipes que não estavam familiarizados com os materiais dos estoques foram ambientados para garantir o cumprimento dos procedimentos.
A figura, a seguir, exibe uma das instruções de trabalho utilizadas na capacitação das equipes envolvidas no processo de transferência.
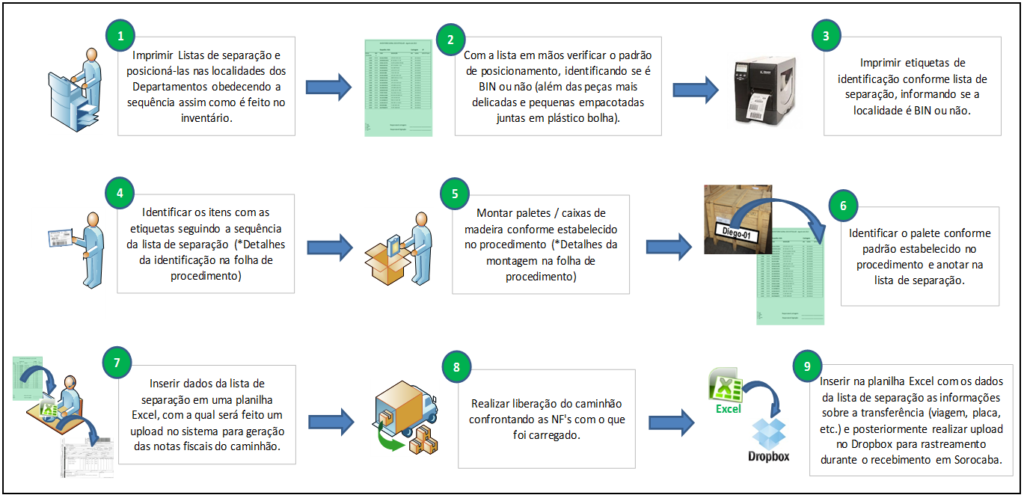
Etapa 4 – Inventário dos itens
Nesta etapa, foi realizado o inventário de todos os itens armazenados em estoque conforme o procedimento da empresa e, em seguida, foram realizados os ajustes necessários no sistema.
Etapa 5 – Definição e identificação de posições de armazenagem na nova planta
Enquanto os itens estavam sendo inventariados na planta produtiva antiga, foram definidas as novas alocações dos itens, conforme a lógica de endereçamento, e foi realizada a identificação das localizações na nova planta produtiva. Desta forma, ao receber os itens na nova planta, as equipes já poderiam armazenar os materiais nos endereços definitivos.
Etapa 6 – Empacotamento, faturamento e carregamento dos itens
Antes de iniciar o processo de transferência, as equipes foram divididas por departamentos e cada uma delas recebeu uma lista informando quais os itens deveriam ser embalados e em quais quantidades.
Os itens foram identificados e embalados conforme os modais definidos na etapa 2 e receberam um endereço de transição para garantir a rastreabilidade do item. Além disso, cada palete ou caixa utilizado na transferência recebia uma packing list com a relação de todos os materiais contidos na embalagem e com os endereços dos itens na nova planta produtiva.
Após executar o processo de embalagem, os itens foram faturados e armazenados na área de pré-carregamento.
Etapa 7 – Transporte
Finalmente, após a emissão das notas fiscais eletrônicas, os itens foram carregados no veículo e enviados à nova unidade da empresa. Todas as informações referentes aos itens de estoque e as viagens realizadas durante o processo de transferência foram centralizadas em um sistema de controle, em que também foram registradas as divergências identificadas durante o processo de separação e embalagem dos itens de estoque.
Etapa 8 – Descarregamento e alocação nos endereços da nova unidade fabril
Ao receber os materiais na nova planta produtiva, as equipes descarregaram as caixas e paletes até a área de picking e realizaram a conferência dos itens, conforme a packing list. Em seguida, os itens foram armazenavam em suas novas posições.
Como você pode ver, um projeto de transferência de plantas feito com excelência, gera inúmeros benefícios para uma organização.
E se você quer mais conteúdos como esse, acompanhe a Nortegubisian pelo Facebook, LinkedIn e Instagram.