Uma tradicional empresa fornecedora de computadores e laptops permite aos seus potenciais clientes que configurem suas próprias máquinas através do seu site, customizadas a partir da escolha entre várias opções de: tipos de processadores, disco rígido, tamanho de tela, sistema operacional, placa de vídeo, peso, cor, tipo de aplicação profissional e preço.
Analisando-se as possibilidades de cada opção (ver na tabela 1) para a família de produtos “notebooks ultrafinos”, chega-se à impressionante quantia de 145.800 diferentes combinações.
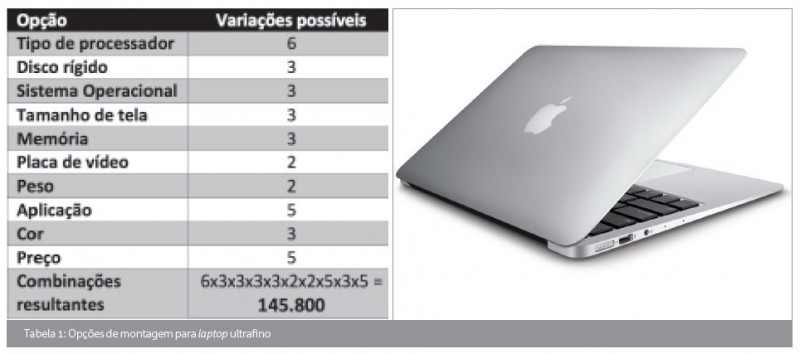
Sob a ótica do cliente, a possibilidade de escolha entre milhares de configurações possíveis é extremamente positiva, pois permite a “montagem” de um produto customizado, focado em suas demandas, expectativas de desempenho e qualidade.
Mas, quando olhamos para o interior das empresas, em particular para a área de gestão de operações, nos deparamos com um cenário bastante complexo: para gerar um grande portfólio de produtos e atender as necessidades dos consumidores, serão necessários milhões de componentes diferentes.
Para entender esta lógica, basta fazer um cálculo simples: se cada máquina (notebook ultrafino) possui dezenas de componentes e o mix de notebooks é da ordem de centenas de opções, a quantidade de componentes diferentes, necessários para montar estes produtos, será da ordem de milhares ou até mesmo milhões de variações.
Nas últimas décadas, notadamente a partir dos anos 80, as organizações industriais têm focado sua estratégia produtiva em mix amplos de produtos, fabricados ou montados em quantidades mensais variáveis e de acordo com a demanda, caracterizando sistemas de produção em lotes e com alta flexibilidade.
A produção em massa se restringiu, neste período, a alguns segmentos de produtos, como determinados tipos de alimentos e produtos químicos.
Para que a diversificação de opções do mix de produtos não gere, como consequência, uma enorme diversidade de itens, a padronização de componentes assume papel fundamental.
Montar ou fabricar produtos diferentes a partir de componentes comuns (padronizados) é a melhor solução para evitar a proliferação de itens e suas consequências, sintetizadas na figura 1: aumento proporcional de itens em estoque, maior necessidade de infraestrutura de controle, área necessária para armazenagem, grande número de fornecedores, de compradores, esforços de gestão de materiais, de planejamento de processos, projeto e manutenção de ferramentas, dispositivos, elaboração e atualização de roteiros de fabricação e montagem e de desenhos.
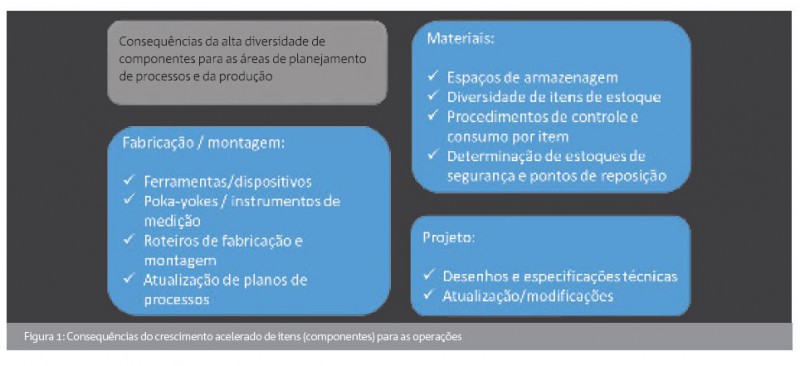
Tecnologia de grupo e seu potencial para padronização de processos e produtos
No final da década de 50, o pesquisador Sergei Petrovich Mitrofanov estudava a adequação entre os limites de capacidade de processamento de máquinas-ferramenta e os componentes que eram processados nestas máquinas. Descobriu que a maioria das máquinas, embora tivesse capacidade para processar peças e componentes de dimensões bastante variáveis, sempre processava componentes de dimensões com poucas variações. A figura 2 exemplifica esta situação: um centro de torneamento possui capacidade para processar eixos com comprimentos variáveis, até 40 pol. No entanto, durante um ano, todas as ordens de produção analisadas apresentaram eixos processados que concentraram a sua dimensão “comprimento” na faixa de 16 a 35 pol.
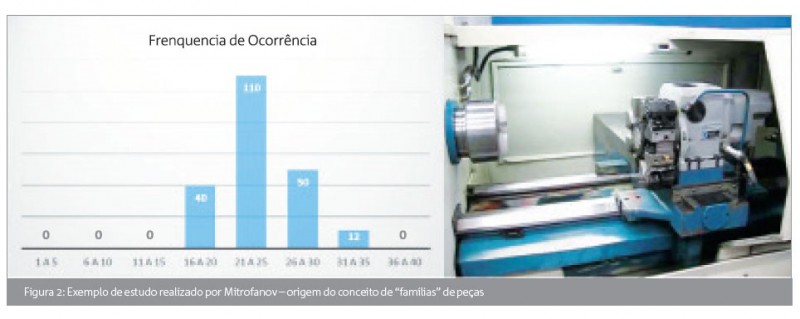
Eixos com comprimentos na faixa de 16 a 30 pol. correspondem a 94% de todas as ordens produzidas na máquina, para o período analisado.
Esta constatação de que as máquinas-ferramenta pudessem estar “subutilizadas” (não em função de sua capacidade produtiva relacionada à quantidade de componentes processados, mas às dimensões destes componentes) originou o conceito de “famílias” de componentes.
Uma “família” de itens caracteriza-se por agrupar componentes, peças ou produtos similares. Os critérios de similaridade geralmente utilizados são as características de projeto e fabricação que apresentam: dimensões, materiais, tolerâncias, especificação da peça em bruto, etapas dos processos de fabricação e montagem.
Na década de 80, John L. Burbidge estruturou o conceito de “Group Technology” (Tecnologia de Grupo) baseado na identificação de “famílias” de peças/componentes e de “agrupamentos” de máquinas e equipamentos. Estes agrupamentos seriam necessários para produzir toda e qualquer peça/componente da família – configurando as células de manufatura e montagem, um layout adequado para processar lotes de quantidades variáveis ao longo do tempo.
Burbidge explorou também os benefícios da Tecnologia de Grupo na área de PPCP (Planejamento, Programação e Controle da Produção): a identificação de similaridades entre peças e componentes, e seu potencial para gerar itens padronizados, que pudessem ser utilizados em diferentes produtos, reduzindo a diversidade de itens a serem programados e por consequência, os esforços da área de PPCP.
A figura 4 mostra as principais características de projeto e fabricação utilizadas para identificação de similaridades e de “famílias” de componentes.
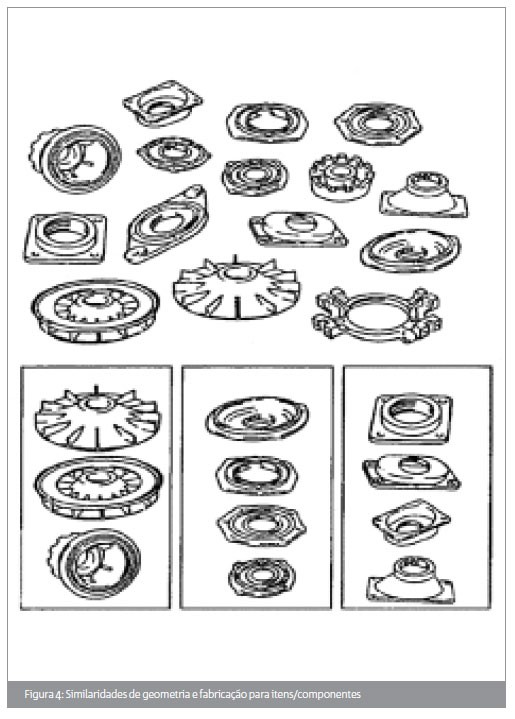
Burbidge também aprofundou o estudo de busca de similaridades para identificar fluxos de processos e gerar layouts com menores desperdícios de movimentação. Este estudo, denominado PFA (Production Flow Analysis), analisa o fluxo produtivo de diferentes itens em uma organização produtiva e avalia a pertinência de adotar arranjos físicos que reduzam as necessidades de movimentação, diminuindo os tempos de ciclo de fabricação.
Uma figura ilustrativa do potencial de aplicação da PFA (Production Flow Analysis) é mostrada a seguir (figura 5).
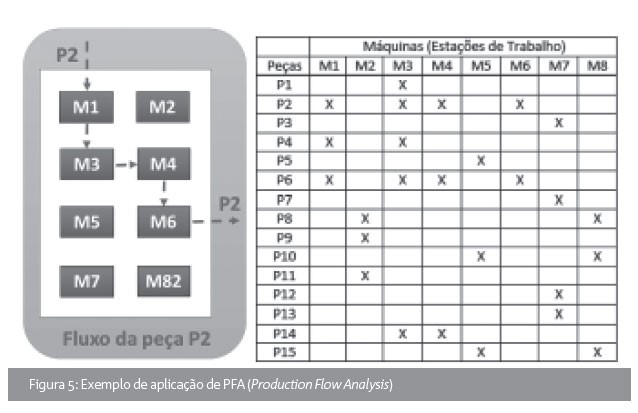
A PFA analisa o fluxo produtivo de cada peça – no exemplo da figura, vê-se o fluxo de P2 representado na matriz de incidência peças x máquinas (estações de trabalho).
Após a representação de cada fluxo, buscam-se os fluxos similares e formam-se os agrupamentos, que gerarão as “famílias” de peças e os “agrupamentos” de máquinas do novo layout.
A figura 6 apresenta a mesma matriz, mas com as peças que possuem fluxos similares identificadas, junto com as máquinas necessárias para seu processamento.
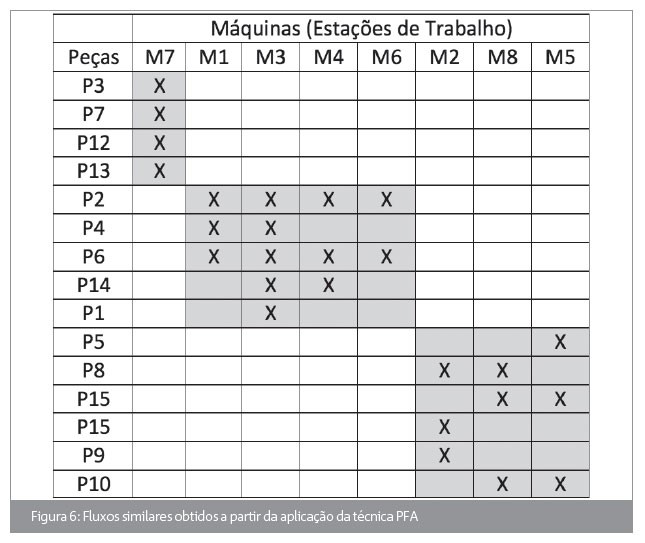
A matriz da figura 6 permite visualizar claramente três agrupamentos obtidos a partir das similaridades de fluxo produtivo: uma família de quatro itens completamente processados na estação M7 (P3, P7, P12 e P13); um agrupamento celular com uma família de quatro itens (P2, P4, P6 e P14) e com um grupo de quatro estações (M1, M3, M4 e M6); outro agrupamento celular obtido com os seis itens restantes (P5, P8, P15, P9 e P10) e com as estações M2, M8 e M5.
Na década de 90, a matriz proposta por Burbidge foi alterada, com a substituição do registro da passagem do item pela máquina de “X” para o algarismo 1. Os espaços em branco na matriz (que denotam a “não” passagem de itens pelas máquinas) foram substituídos por algarismos “0”. A matriz de incidência passou a ser representada, portanto, por um conjunto de algarismos “1” e “0”. Esta pequena mudança permitiu que a busca de similaridades de fluxo passasse a ser feita a partir de algoritmos matemáticos – a “cluster analysis” passou a ser utilizada. Os algoritmos passaram a ser implementados através de rotinas computacionais, gerando maior velocidade na análise dos agrupamentos e na identificação de similaridades.
Atualmente, um grande número de algoritmos diferentes está disponível para avaliar similaridades de fluxo e apresentar soluções de layout baseadas nos princípios desenvolvidos por Mitrofanov e Burbidge.
O potencial de padronização da TG (Tecnologia de Grupo)
A aplicação dos princípios da TG permite obter ganhos consideráveis de tempo tanto no projeto de novos itens, como nos esforços de planejamento de processos produtivos.
A adoção de itens padronizados reduz a necessidade de projetar novos componentes para cada novo produto – auxilia a projetar e modificar projetos com maior velocidade e eficiência.
Os estudos de similaridade de processos permitem identificar fluxos e layouts que economizam tempos de movimentação e projetar ferramentas padronizadas, que reduz os tempos de setup para componentes da mesma “família”, aumentando a disponibilidade dos equipamentos.
O potencial de utilização da TG (figura 7) é muito promissor, mas, no entanto, permanece ainda desconhecido para grande parte das organizações industriais.
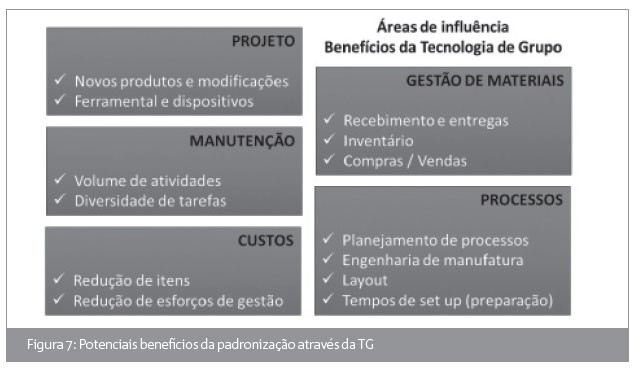
Se você gostou desse conteúdo, continue nos acompanhando no Linkedin, Facebook e Instagram para mais novidades!