Definição
O Kanban é um meio de realizar a Produção Puxada (produzir no exato momento em que o processo “cliente” solicita, ou seja, só quando o processo seguinte necessita), através de um método simples e visual. Trata-se de um dispositivo sinalizador que fornece instruções para a produção, retirada ou transporte de itens.
Um dos principais desperdícios Lean observados nas empresas é o desperdício por excesso de estoques. O excesso de materiais na empresa (altos estoques de matérias-primas, estoques intermediários e de produtos acabados) incorre em:
- Manuseio desnecessário;
- Necessidade de área extra de armazenagem;
- Custos de oportunidade;
- Os estoques tendem a camuflar problemas de longos set ups de máquinas, quebras, projetos ruins, fornecedores não confiáveis, layouts ineficientes e não conformidades.
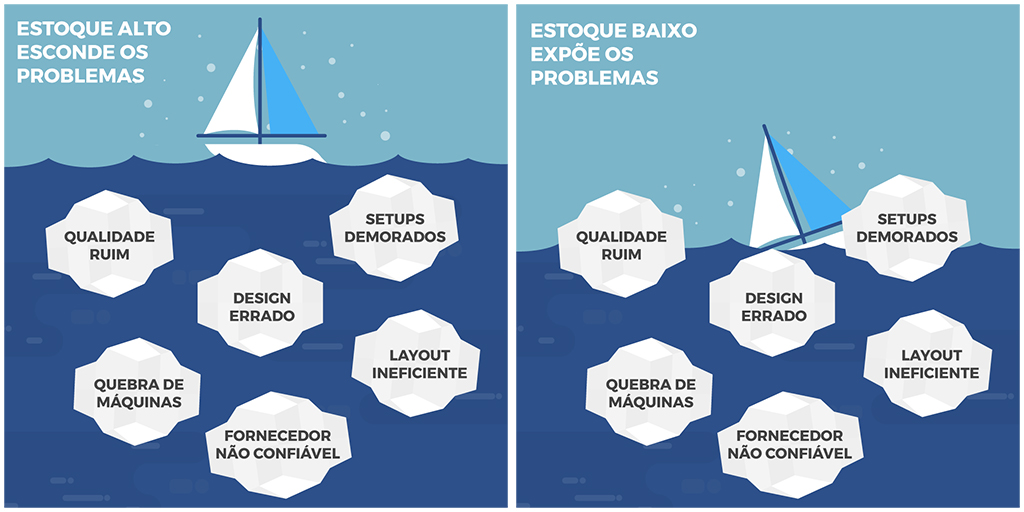
Na busca pela redução ou eliminação dos desperdícios causados pelo excesso dos estoques, muitas empresas que apresentam demanda regular para grande parte de seus produtos adotam a filosofia do Just in Time (JIT).
O JIT é uma filosofia de trabalho cujo objetivo é produzir bens e serviços exatamente no momento em que são necessários de forma a atende a demanda instantaneamente, com qualidade perfeita e sem desperdícios. As partes necessárias são alimentadas no tempo certo, no local certo e na quantidade necessária. Uma empresa que consegue estabelecer este fluxo pode buscar uma situação de “inventário-zero”.
Para isso, é fundamental a adoção de um sistema de produção puxada, em que cada etapa do processo só deve produzir um bem ou serviço quando um processo posterior, ou o cliente final, o solicite.
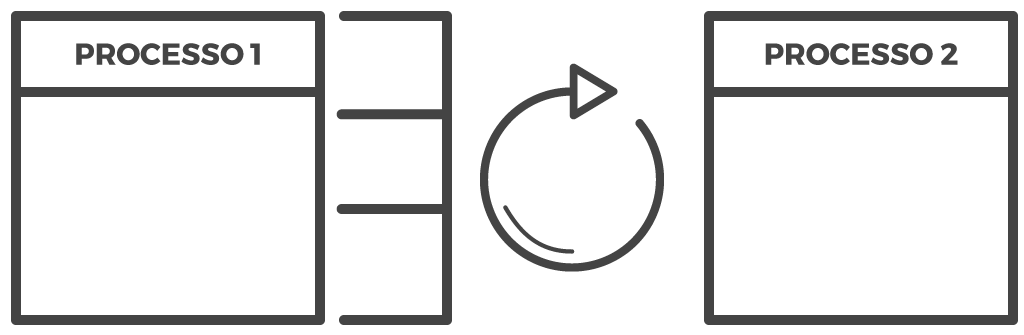
Esta solicitação se dá através do consumo de um estoque controlado de peças, chamado de supermercado, localizado entre os processos. Se o processo posterior não consumir um determinado item, o processo anterior não o produzirá, mesmo que isto contrarie a previsão de vendas.
A produção puxada transfere para o chão-de-fábrica a responsabilidade pela programação diária da produção. São os operadores, baseados na demanda do cliente, que passam a decidir o que fazer e quando fazer.
Supermercados são estoques controlados dimensionados de tal modo que:
- O processo cliente sempre encontra peças dos modelos e nas quantidades necessárias para cumprir seu programa de entregas ou para repor seu supermercado;
- O processo fornecedor sempre consiga repor o supermercado antes que os níveis mínimos de peças definidos sejam atingidos.
Os objetivos dos supermercados são:
- Controlar a produção entre fluxos;
- Controlar a produção no processo fornecedor, “sem programação”;
- Proporcionar que a produção seja realizada baseada em uma demanda real utilizando cartões Kanban.
Os três tipos de cartões Kanban são:
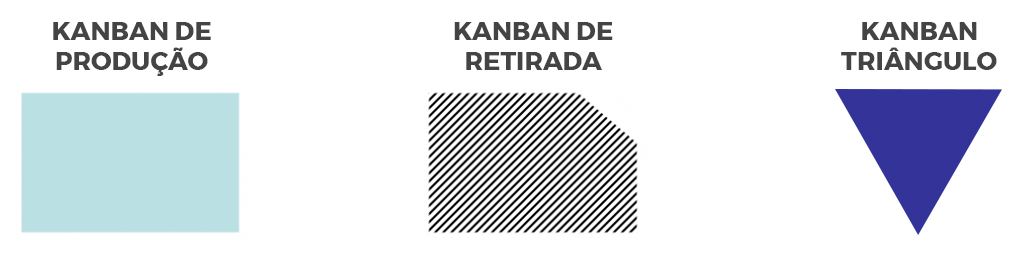
- Kanban de produção: Dá autorização para um processo produzir o item em uma determinada quantidade.
- Cartões: Cada cartão corresponde a uma embalagem do item;
- Triângulo (Kanban de Sinal): Cartão em formato triangular que corresponde a um lote de produção do processo fornecedor.
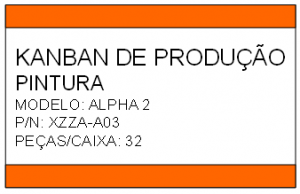
- Kanban de retirada: Dá autorização para a compra de itens em supermercados, em uma determinada quantidade (sistemas de 2 cartões).
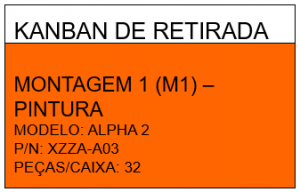
Regras do Kanban
- Regra 1: O processo cliente somente retira peças do supermercado quando isto realmente for necessário, isto é, seja para atender a demanda do cliente, seja para repor o seu supermercado;
- Regra 2: O processo fornecedor só pode produzir itens dos quais possuir Kanban de produção e nas quantidades definidas nestes;
- Regra 3: Somente peças boas podem ser colocadas em supermercados.
A dinâmica do Sistema Kanban
Existem 2 tipos de dinâmicas para a operacionalização do sistema Kanban:
- Um cartão: Usado quando o supermercado fica próximo do processo cliente.
Cliente retira peças do supermercado quando necessário e o cartão de produção que acompanhava a caixa é levado para o quadro REGRA 1.
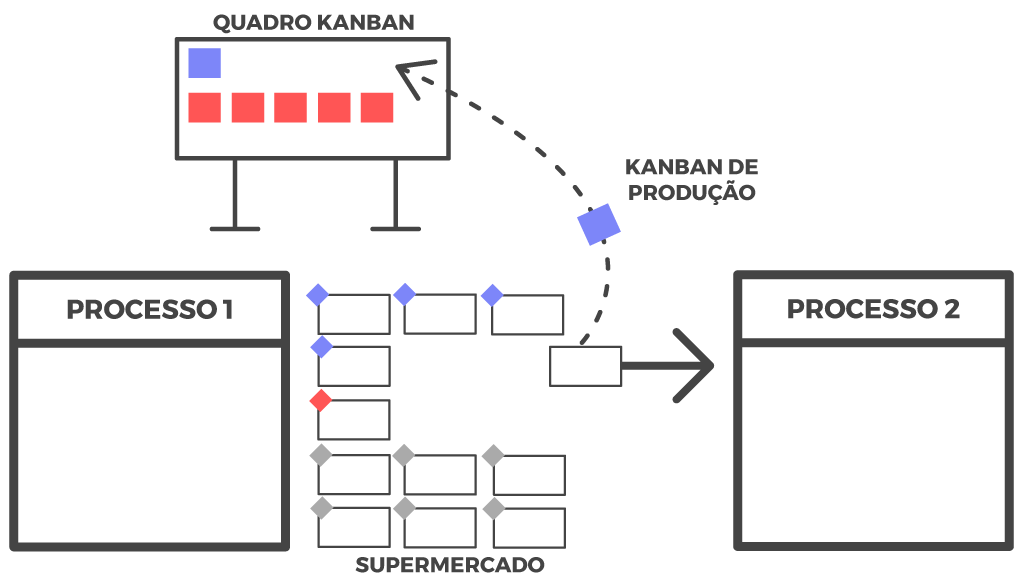
O processo fornecedor produz o item mais crítico do supermercado retirando o Kanban do quadro e colocando-o na caixa de volta ao supermercado REGRA 2.
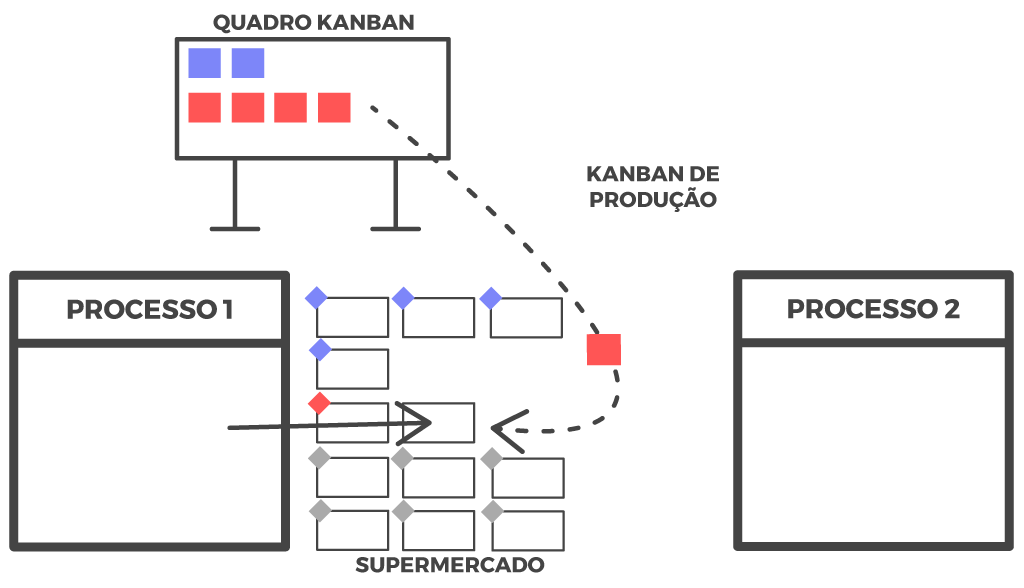
- Dois cartões: Usado quando o supermercado fica distante do processo cliente, como por exemplo, no recebimento.
O cliente consome as embalagens que estão no supermercado da linha REGRA 1. Os cartões de retirada que acompanhavam estas caixas, permitem a compra de peças no supermercado do fornecedor.
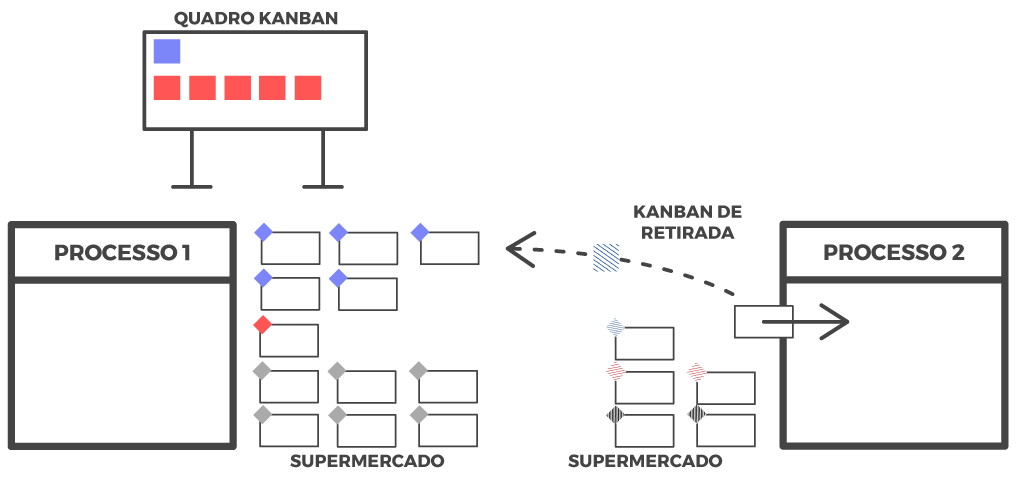
O Kanban de retirada autoriza o cliente a retirar uma embalagem do supermercado. O Kanban de produção que estava na caixa é levado para o quadro e sua produção é autorizada REGRA 2.
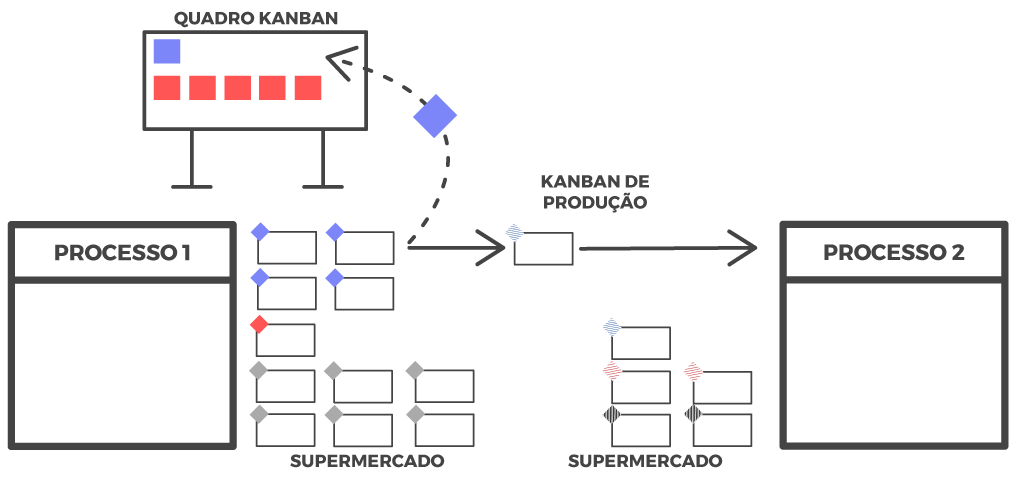
O Quadro Kanban
O quadro Kanban é um dispositivo de gestão visual para que os operadores possam decidir sobre a produção ou não de um item que é consumido em um supermercado entre dois processos.
A medida que o cliente retira peças de um supermercado, os cartões de produção que acompanhavam as caixas são levados para o processo fornecedor e são colocados em quadros. Estes quadros devem mostrar para a linha qual o item que deve ser produzido primeiro e qual o tamanho do lote a ser produzido.
A medida que os cartões chegam ao quadro eles são inseridos primeiramente sobre a faixa verde, depois amarela e, por fim, sobre a vermelha.

Quando as peças vão sendo produzidas os cartões são retirados primeiramente da faixa vermelha, depois da amarela e por fim da verde.

Os cartões que não estão no quadro estão no supermercado acompanhando caixas cheias de peças.

Quando o quadro está cheio de cartões o supermercado está vazio e vice-versa.

O significado das faixas:
- Faixa verde
- Quantidade de cartões: Lote de produção.
- Significado: Não há necessidade de produzir o item.
- Faixa amarela
- Quantidade de cartões: Lead time de reposição.
- Significado: É preciso produzir o item.
- Faixa vermelha
- Quantidade de cartões: Proteção necessária.
- Significado: A proteção está sendo consumida.
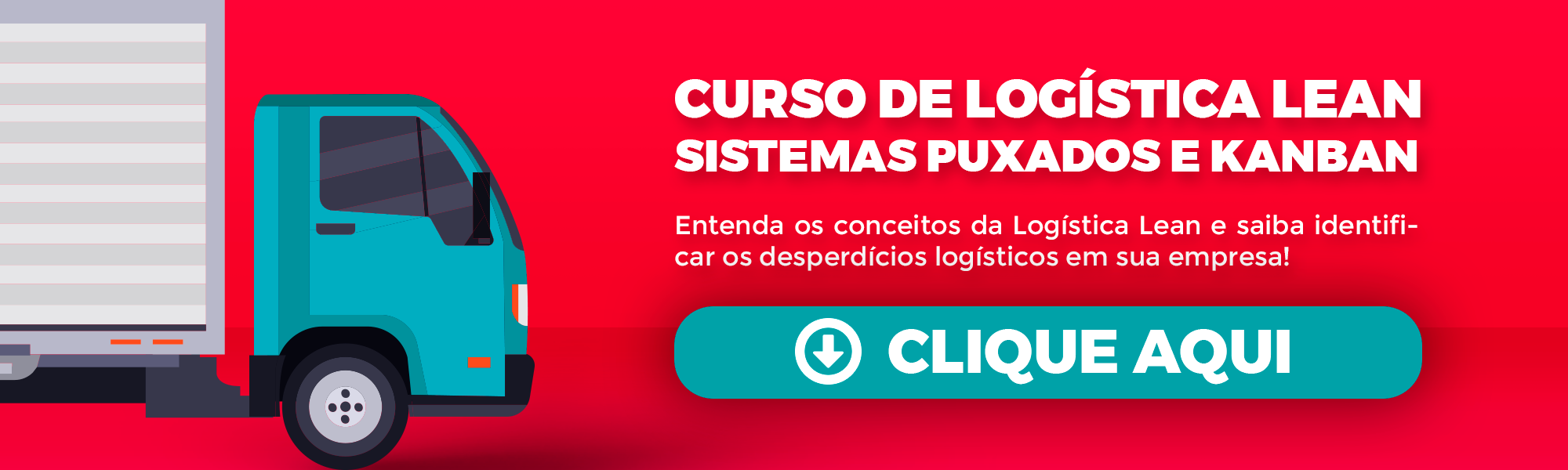
A seguir, a Nortegubisian apresenta as 6 etapas de implantação do sistema Kanban em uma empresa.
1. Elaborar o Mapa de Fluxo de Valor de Estado Atual (VSM) do processo
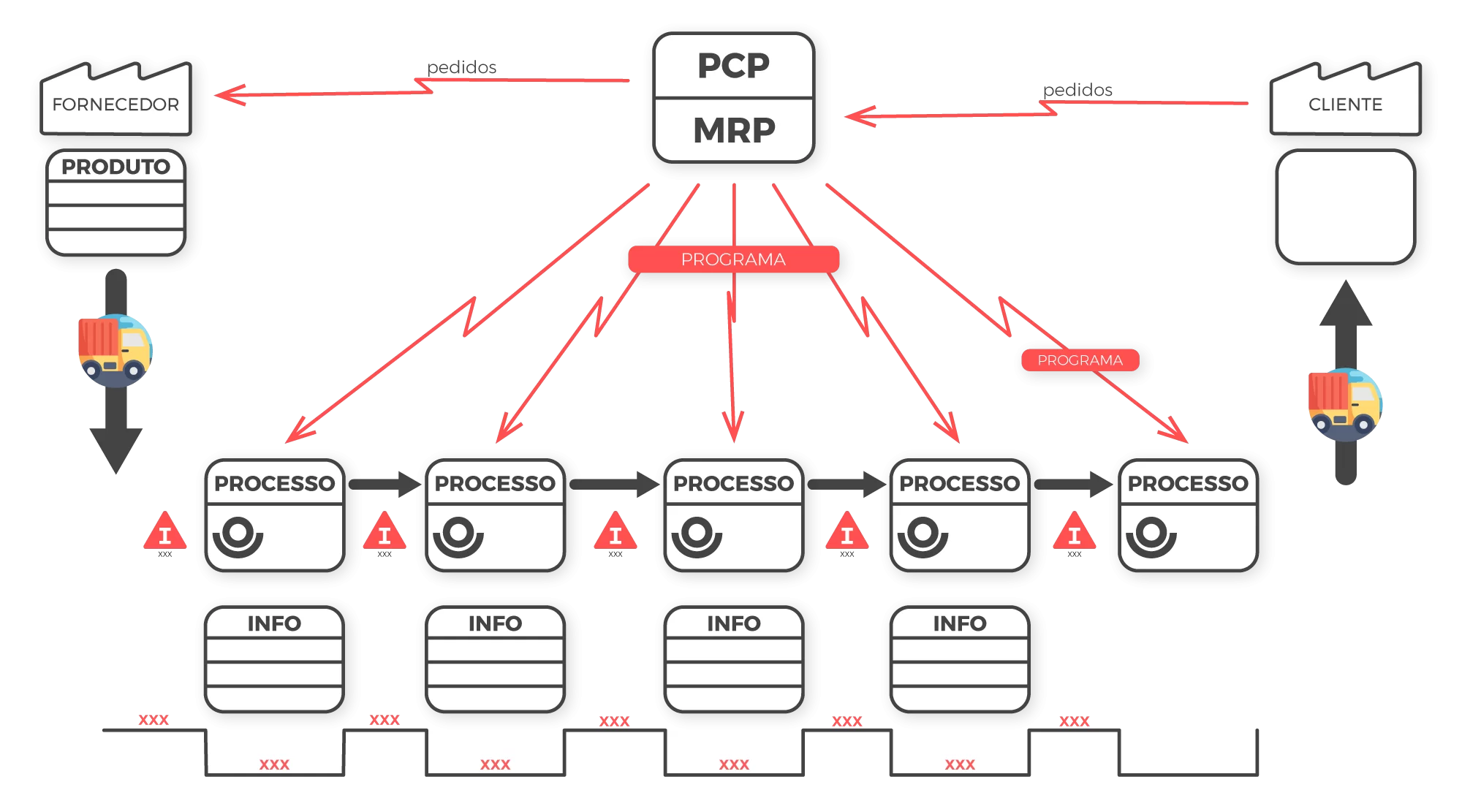
2. Elaborar o Mapa de Fluxo de Valor de Estado Futuro (VSM) do processo
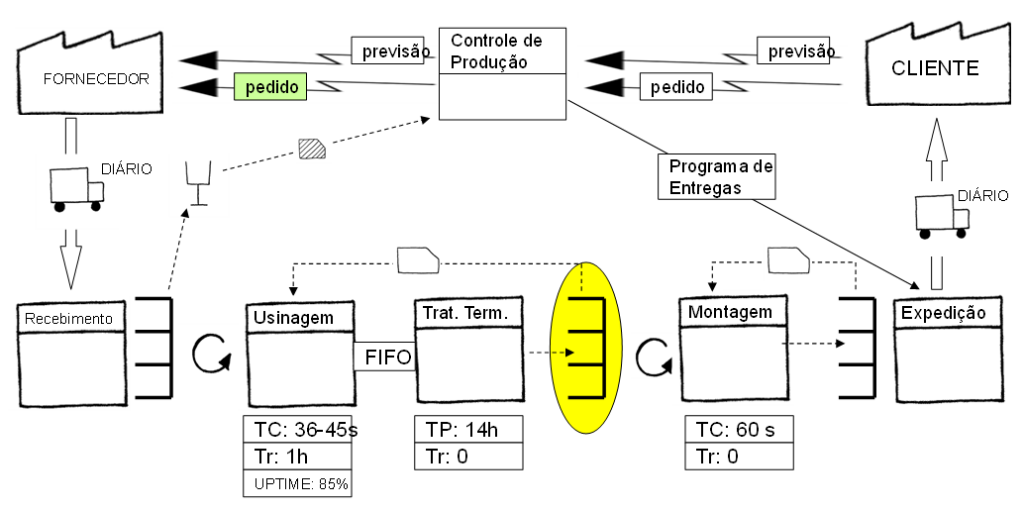
3. Levantamento de dados
- Previsão de demanda das próximas semanas;
- Tempos de ciclo dos processos por modelo na usinagem;
- Quantidade de peças por embalagem;
- Tempo de setup de cada modelo na usinagem;
- Confiabilidade no processo;
- Tamanho dos lotes consumidos pelo cliente interno;
- Tempo disponível para produzir (considerando o uptime).
4. Análise de Demanda dos Itens que compõem o Portfólio
- Identifique os itens de alta frequência e alto volume (I);
- Identifique os itens de alta frequência e baixo volume (IV);
- Identifique os itens de baixa frequência (II e III).
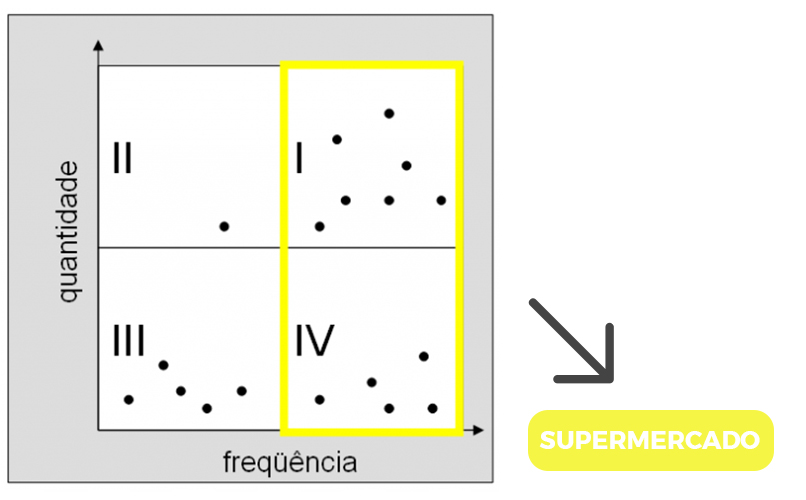
Os itens que podem compor um sistema Kanban e um Supermercado são aqueles de alta frequência de demanda, independentemente do volume produzido.
Antes que um item seja colocado no supermercado é importante buscar entender as razões para as variações de volume de mês a mês, ou mesmo de semana para semana.
Não se pode esquecer que supermercados são indesejáveis. Quanto maiores as oscilações de demanda, maiores eles devem ser para filtrar estes picos para dentro da fábrica.
Para itens com baixa frequência de demanda, recomenda-se a implantação de sistemas empurrados (MTO).
5. Dimensionamento das Faixas Verde, Amarela e Vermelha
Para o cálculo das faixas verde, amarela e vermelha de um supermercado considerando o sistema de um cartão do tipo produção, as seguintes expressões são utilizadas:
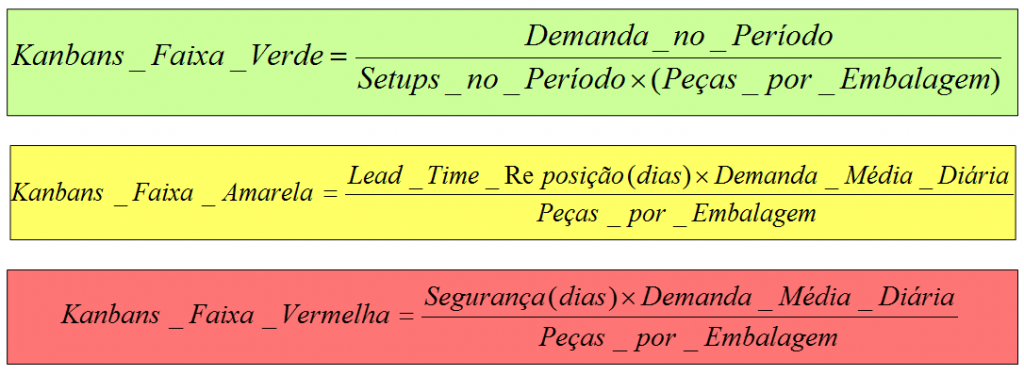
6. Projeto do Quadro Kanban e Heijunka Box
O Heijunka Box é uma ferramenta que permite a programação horária da produção no chão de fábrica. Ele auxilia os operadores a fazerem a programação de produção através do controle dos estoques de peças prontas. Além da quantidade a ser produzida, o quadro indica o ritmo e horários em que devem ser produzidos os vários itens pela linha.

Aplicação
Para exemplificar a implantação do sistema Kanban, a Nortegubisian irá abordar um dos cases de aplicação ao processo de produção de embalagens, mais especificamente caixas de papelão, utilizadas no packing da maior empresa produtora de uvas de mesa do Brasil.
Cenário abordado:
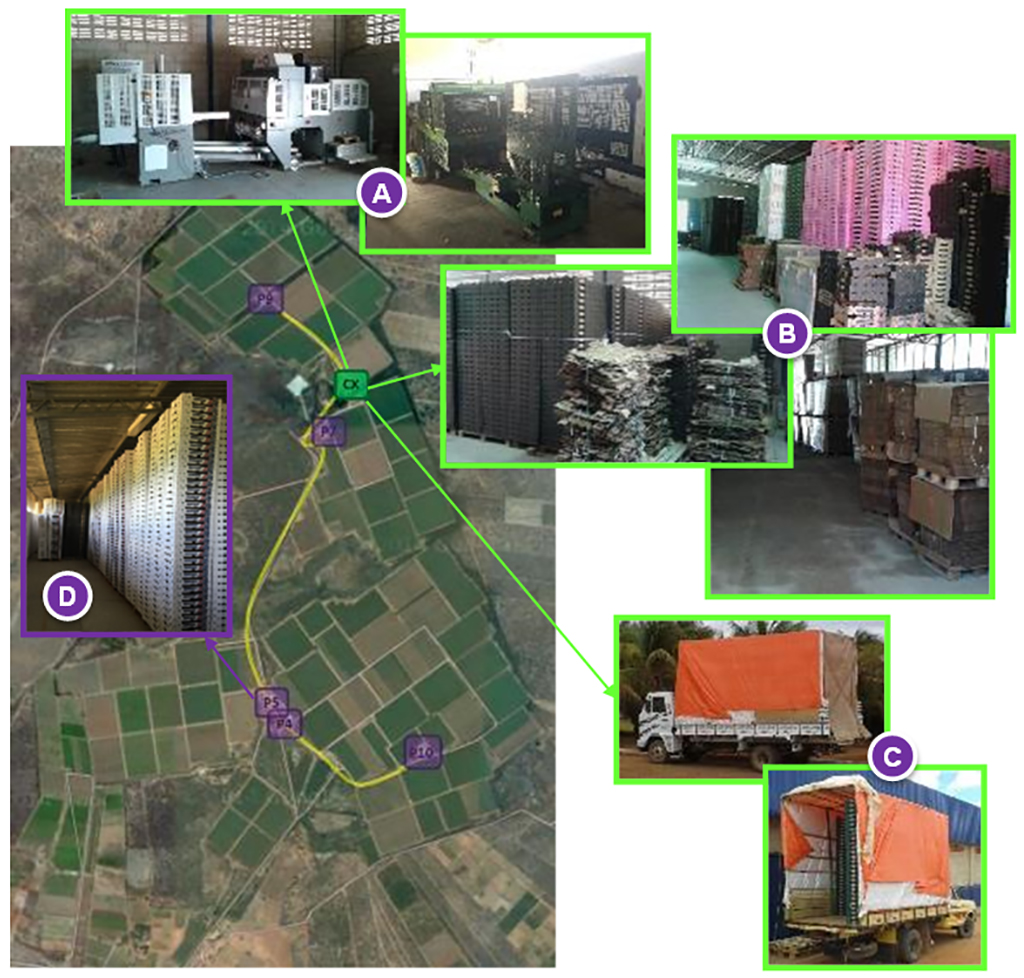
- A Caixaria (área onde são produzidas as embalagens de papelão) possui 2 máquinas de montar caixas (A), as quais trabalham com rendimentos aproximados de 1100 a 1200 cxs/hora;
- A Caixaria deve abastecer 5 Packings espalhados pela fazenda;
- Durante a safra 2 caminhões (C) atuam de forma exclusiva na logística de abastecimento de caixas para os Packings;
- Nos packings são encontrados altos volumes de caixas de diferentes tipos (D) espalhadas pelo almoxarifado;
- Após a reunião de planejamento diário da colheita é realizada a programação do packing para o dia seguinte via sistema. Tanto o Almoxarifado quanto a Caixaria recebem um relatório impresso (E) com a quantidade de material necessário por Packing. Contudo, durante o dia a quantidade pré-estabelecida pode ser alterada conforme feedback das coordenadoras dos Packings (a quantidade por tipo de caixa a ser transportada é definida de maneira empírica, ou seja, baseado na experiência dos responsáveis);
- A Caixaria recebe a programação de recebimento em uma planilha Excel (F) por e-mail e mais as NF’s do cliente para conferir no recebimento da carga. Após conferência a Nota é enviada ao escritório central que lança a informação no sistema;
- O controle de saída de caixas (G) é lançado no sistema pela própria Caixaria (transferência da Caixaria para os Packings).
Por meio do histórico de demanda de 1 (um) ano, foram analisadas a frequência e média de consumo por tipo de caixa e por Packing. Tal estudo permitiu definir quais tipos de caixa eram apropriados para o uso do sistema Kanban (MTS – Make to Stock).
Além disso, pela análise da capacidade produtiva foi possível definir o OEE (eficiência global do equipamento) das máquinas que montam as caixas.
Pela análise dos apontamentos das viagens dos caminhões pode-se concluir o tempo médio de viagem do ponto de origem até os pontos de consumo, além dos tempos de carregamento e descarregamento dos caminhões.
Feito isso, foram calculados os Kanbans de retirada e produção para cada caixa:
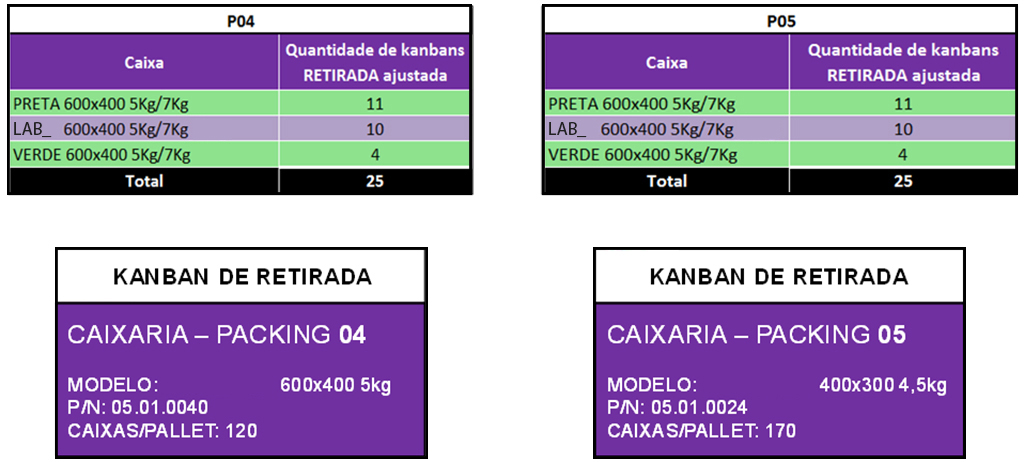
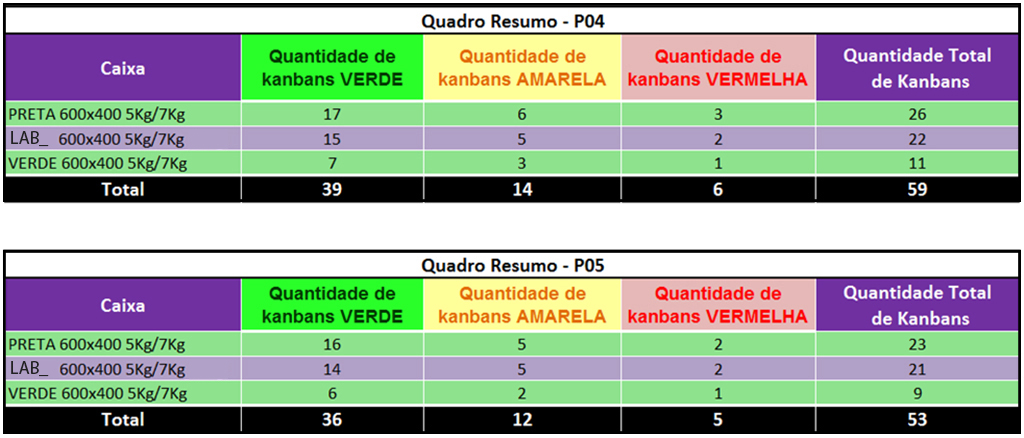
Depois disso, foi dimensionado e projetado o quadro Heijunka Box para permitir a tomada de decisão e gestão do processo de reposição de embalagens pelos operadores. Veja a figura a seguir:

Em seguida foi definida o modelo de funcionamento do Sistema Kanban projetado para a operação.
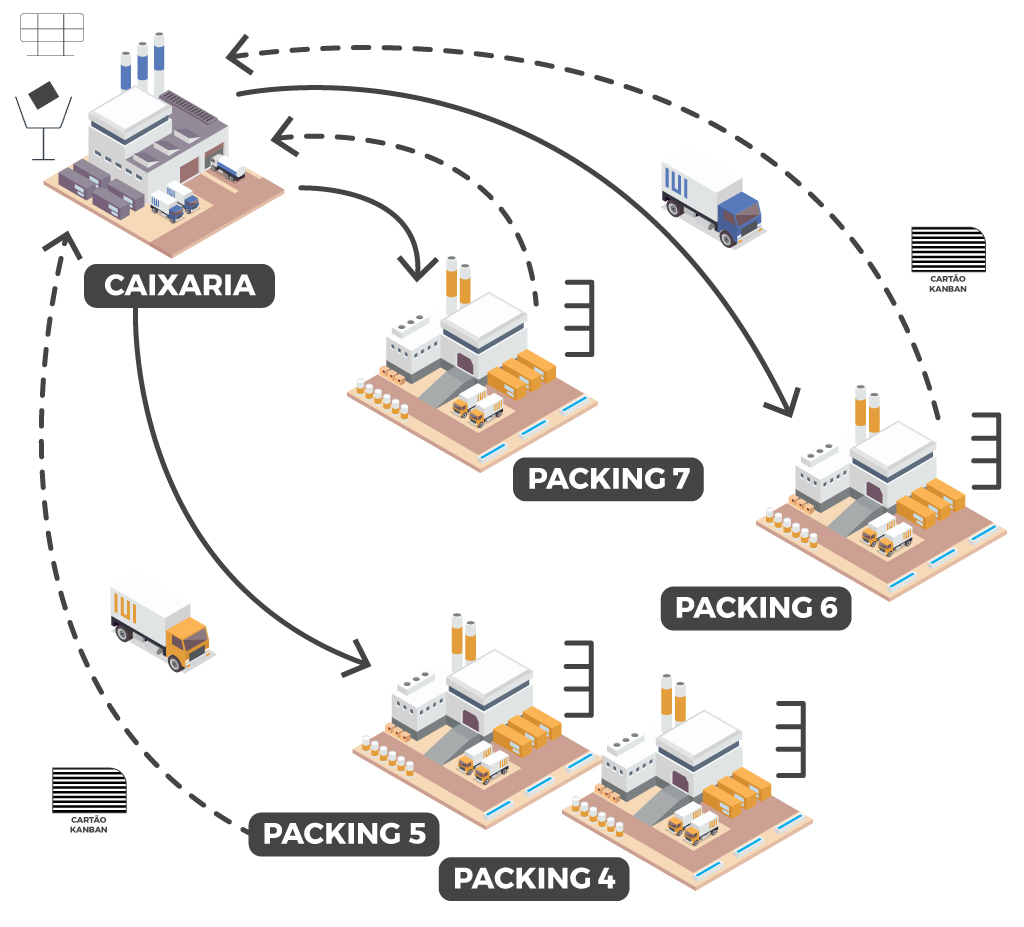
A. O Packing (“Cliente”), ao realizar uma “compra”, retira um pallet fechado de um determinado tipo de caixa presente no Almoxarifado (Caixaria do Packing). Para cada pallet de caixas há 1 Kanban de Retirada, o qual é removido do pallet assim que houver um consumo. Estes cartões Kanban serão guardados por um responsável em uma caixa identificada, onde o motorista do caminhão irá pegar ao final de cada descarregamento. Posteriormente, o motorista do caminhão irá levar os Kanbans de Retirada em seu retorno para a Caixaria.
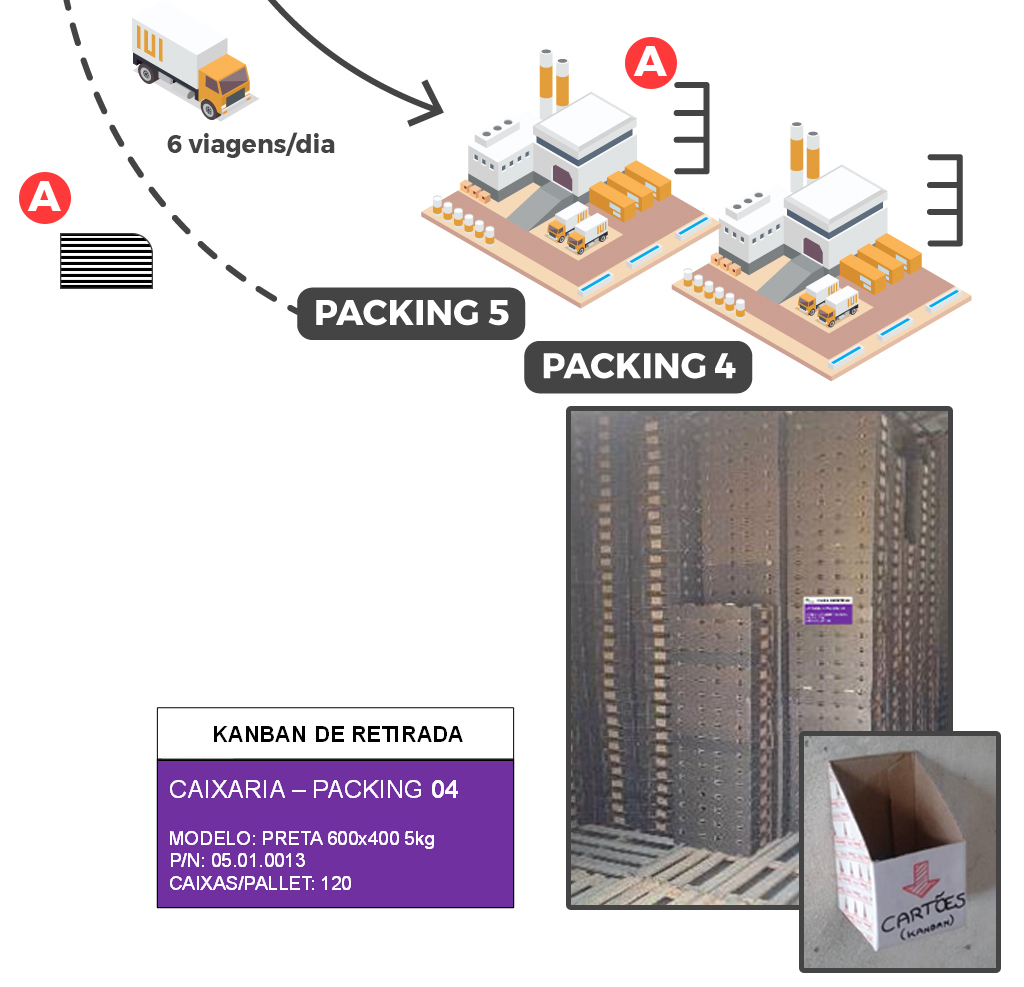
B. Ao chegar na Caixaria, o motorista mostra ao líder de máquina os Kanbans de retirada (“moeda de troca”). O líder de máquina irá autorizar sua equipe a separação dos pallets correspondente ao número de cartões trazidos pelo Motorista. Cada pallet da Caixaria possui um cartão Kanban de Produção, o qual é retirado do pallet na medida em que carrega o caminhão. Por sua vez, o motorista carrega o caminhão com os novos pallets e retorna para o Packing com os Kanbans de retirada após “compra” efetuada.
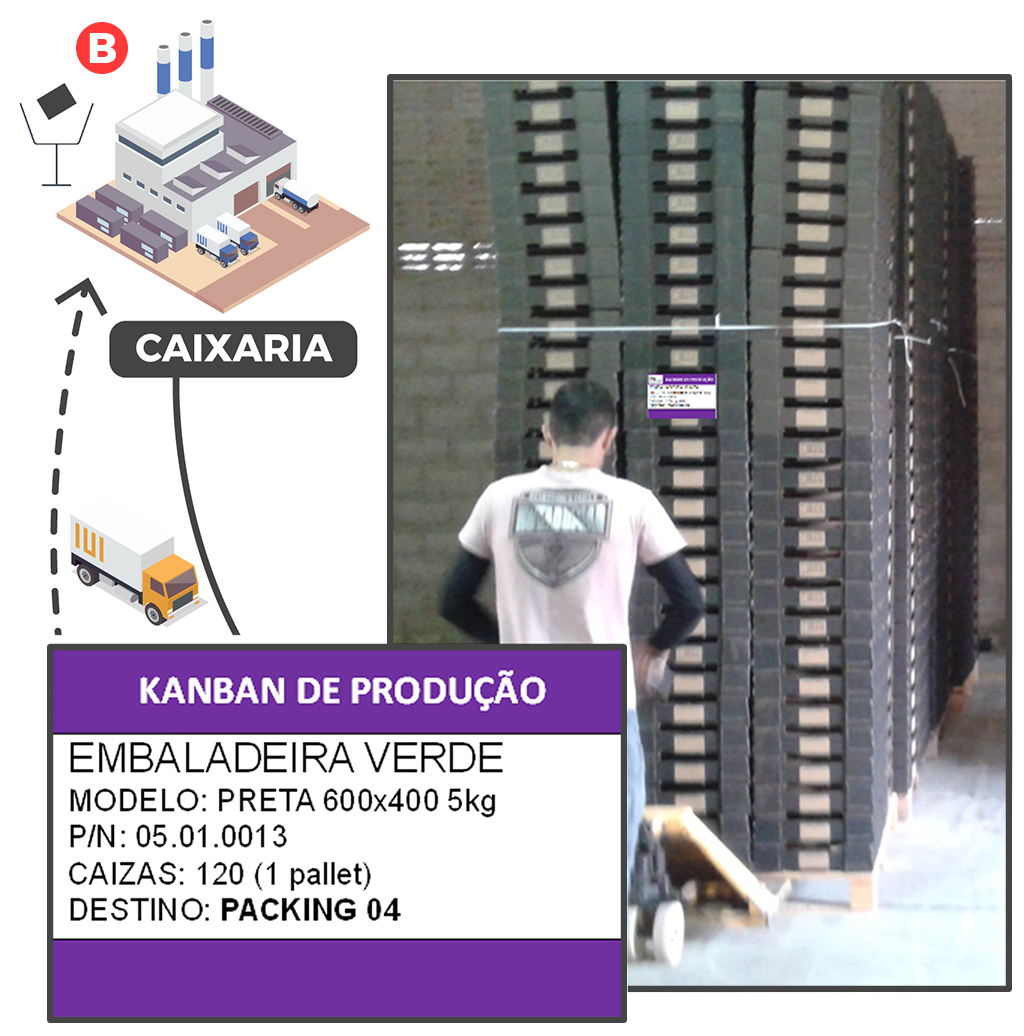
C. Com os Kanbans de Produção retirados dos pallets entregue ao motorista, o líder da máquina irá programar a produção das caixas por meio do Heijunka Box, colocando os Kanbans no quadro (esquerda para direita). Cada novo pallet produzido será identificado com um Kanban de produção que será retirado (direita para esquerda) do Heijunka Box e posteriormente armazenado em seu endereço.
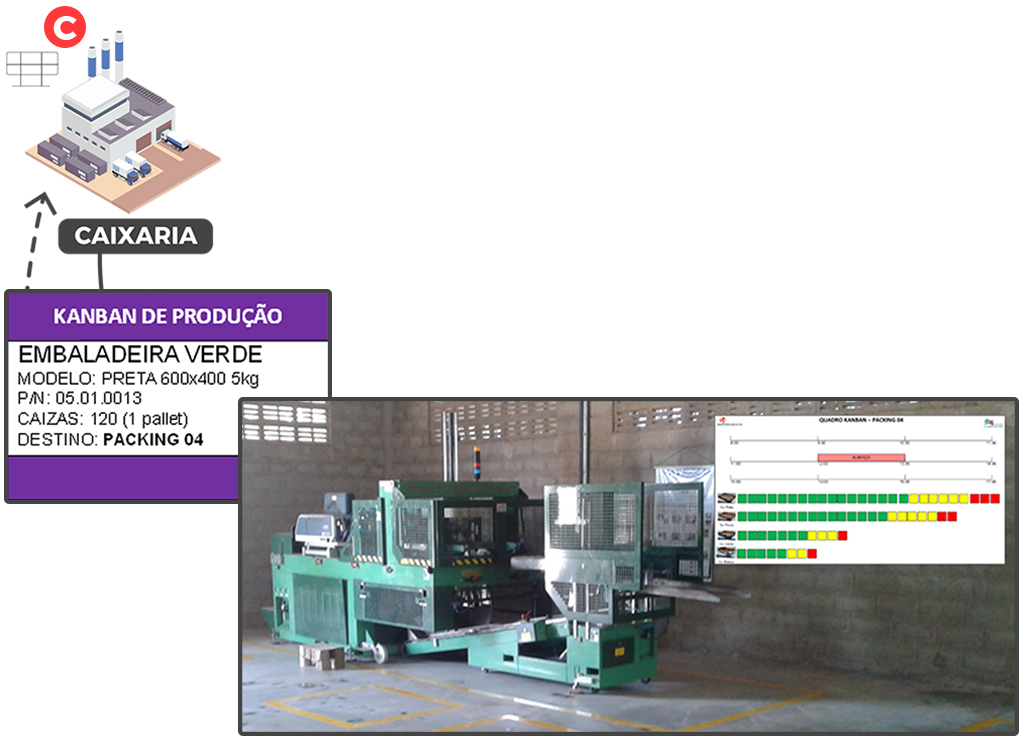
Por fim, a Nortegubisian projetou as áreas de alocação dos supermercados de embalagens (caixas) na caixaria para atender a demanda de cada um dos packings em operação: packings 04, 05 e 07.
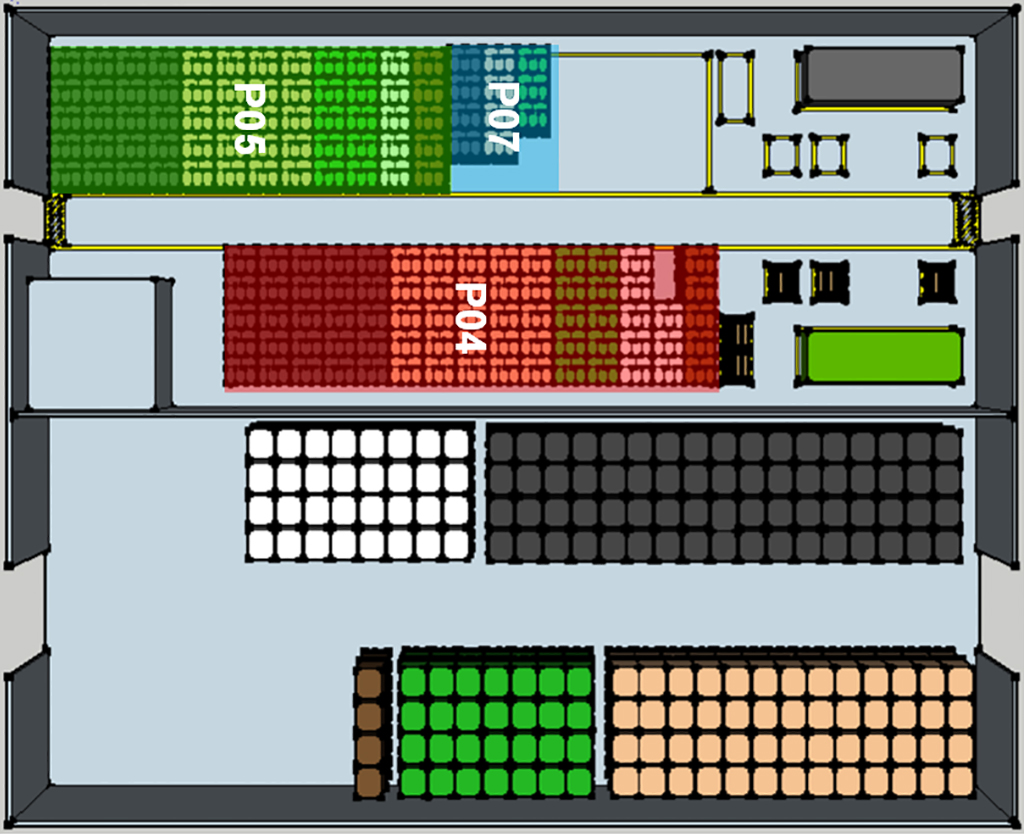
O projeto do layout é importante para manter a organização do espaço de trabalho contribuindo para a manutenção das práticas de 5S na operação.
Nos acompanhe no Facebook, Instagram e Linkedin, estamos sempre atualizando nossos conteúdos para você alcançar a excelência organizacional.