Desafio
De origem nacional e com mais de 70 anos de história, essa empresa possui mais de meio milhão de metros quadrados em área nas suas duas unidades, produzindo diariamente 240 toneladas de produtos, que são distribuídos para mais de 80 países.
Mesmo com um grande quadro de profissionais especializados de manutenção, os executivos observavam um cenário de aumento dos custos de peças de reposição e se frustravam com repetidos esforços mal sucedidos para aumentar o tempo disponível de suas máquinas, principalmente na estabilização de seu desempenho após limpeza e troca de produto. Além disso, devido ao alto nível de automação de seus processos produtivos, os operadores de máquina tinham sua capacidade subutilizada, fazendo o papel de inspetores do processo e observando o trabalho das máquinas, tudo isso com uma cultura de “eu quebro, você conserta” com a manutenção.
Solução
Diante dessa problemática, e visando a redução dos custos de manutenção e o aumento de disponibilidade dos equipamentos, a Nortegubisian viu a oportunidade de aplicar sua metodologia de Manutenção Autônoma, um dos oito pilares da Manutenção Produtiva Total (TPM). Aliada a esta metodologia, foram utilizados princípios da manufatura enxuta, em um projeto composto das seguintes etapas: diagnóstico do processo produtivo, treinamento e implantação dos sete passos da Manutenção Autônoma (MA).
A equipe Nortegubisian usou o Value Stream Mapping (VSM), para mapear e entender o macro processo produtivo, o fluxo de materiais e o fluxo de informação porta-a-porta de uma família de produtos, correspondente a uma das linhas de produção. O VSM permitiu também o registro de algumas oportunidades de melhoria baseadas na mentalidade dos desperdícios do Lean Manufacturing.
Após treinamento ministrado pelos consultores da Nortegubisian sobre os conceitos da MA e seus passos de implantação, foi escolhida uma linha piloto para a realização dos trabalhos. Esta linha foi dividida em equipes, chamadas Grupos Autônomos (GAs), sendo atribuído um líder a cada uma delas. Os colaboradores de cada GA foram responsáveis pela execução dos passos de MA nas máquinas relacionadas, sob supervisão e coaching da consultoria.
Passo 1 – Limpeza, inspeção e etiquetagem
O primeiro passo da MA consistiu em uma grande força tarefa dos operadores e da equipe de gestão na limpeza e lubrificação das máquinas e equipamentos, na sua inspeção e reaperto de parafusos. Além disso, as ações de reparo e melhoria dos equipamentos, identificadas durante a limpeza e inspeção, foram geridas visualmente pelos próprios operadores, por meio de etiquetas coloridas.
Passo 2 – Medidas de combate à fonte de origem de sujidade e locais de difícil acesso
O segundo passo consistiu em um olhar mais crítico a respeito das atividades do passo 1. Nesse passo, foram identificadas as causas raízes da presença da sujeira encontrada nas máquinas e equipamentos, bem como foram identificados e documentados os casos em que havia dificuldade de acesso para limpeza e inspeção dos equipamentos.
Para ambos os casos, foram elaborados e documentados planos de ação, envolvendo os operadores e a manutenção.
Um exemplo de plano de ação é mostrado na Figura 1. Nesse exemplo, a troca de uma vedação tipo “O-ring”, ates feita com o uso de uma chave tipo “unha”, passou a ser feita com o auxílio de uma alavanca. Além de se eliminar a necessidade de uma ferramenta, essa ação reduz o tempo de troca, potencialmente aumentando a disponibilidade do equipamento.
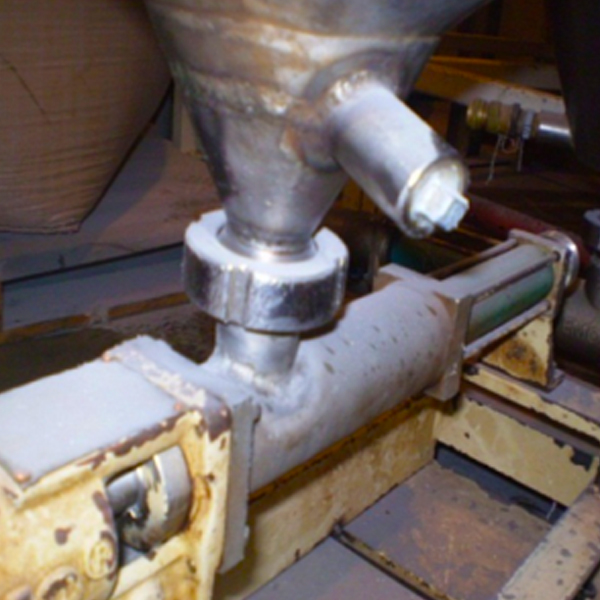
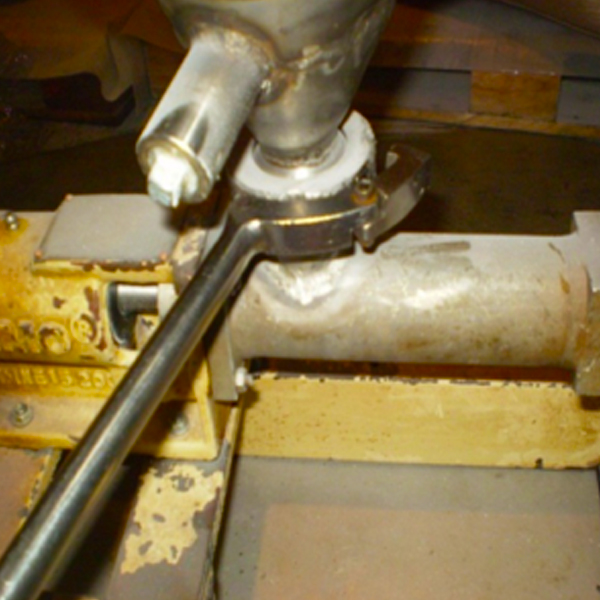
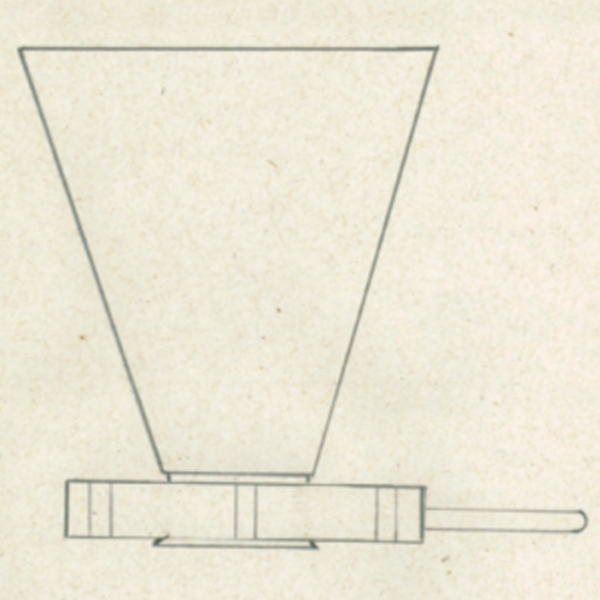
Figuras 1, 2 e 3 – Exemplo de plano de ação realizado no passo 2.
Passo 3 – Elaboração de procedimentos provisórios de limpeza e inspeção
No terceiro passo as atividades de limpeza e inspeção foram incorporadas à rotina de trabalho dos operadores, estabelecendo padrões de limpeza e operação. Tais padrões são simples e objetivos e usados pelos operadores para comparação com a situação encontrada nos equipamentos, definindo se há um problema ou não. Adicionalmente, os padrões estabelecem responsabilidade e frequência às atividades. A Figura 2 mostra um exemplo de procedimento e sua execução.
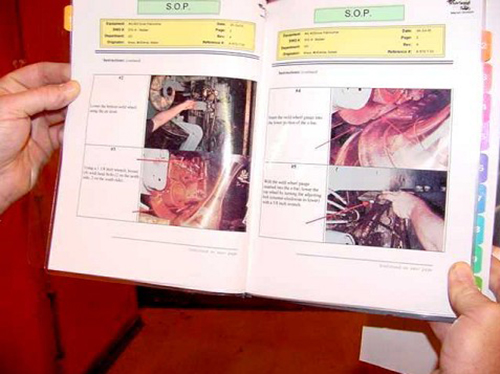
Figura 2 – Procedimento e execução (passo 3).
Passo 4 – Inspeção geral dos equipamentos
O objetivo desse passo foi proporcionar conhecimento técnico aos operadores, por meio de maior integração com a equipe de manutenção. Dessa forma, os operadores passaram a compreender formalmente a estrutura e funcionamento dos seus equipamentos, complementando a sua experiência diária.
Passo 5 – Inspeção autônoma
Nesse passo, as atividades e conhecimentos adquiridos nos passos anteriores foram consolidados e documentados na forma de uma revisão dos procedimentos do passo 3 e em Lições Ponto a Ponto.
Passo 6 – Padronização
Com o objetivo de padronizar as atividades de MA, foram desenvolvidas Instruções de Trabalho Padrão (ITPs), que orientam cada atividade do procedimento do passo 5. Cada operador foi treinado em todas as ITPs e a manutenção acompanhou de perto as atividades de MA dos operadores durante um período de testes e adaptações.
Passo 7 – Auto-Gestão
O passo final da metodologia de implantação da MA visou a estruturação de um modelo de melhoria contínua das suas atividades e de seus resultados. Para tal, indicadores de desempenho foram estabelecidos e monitorados pelos próprios GAs, com a elaboração de planos de ação sempre que necessário. Adicionalmente, são estabelecidas auditorias periódicas que garantem a plenitude de execução das atividades.
Resultados
Dentre os resultados e benefícios verificados com a implantação da MA, pode-se citar:
- Redução de 48% do tempo indisponível das máquinas devido à manutenção corretiva (de 3,05% para 1,57%). Esse aumento de disponibilidade representou 55 horas a mais de produção por mês, conforme figura a seguir:
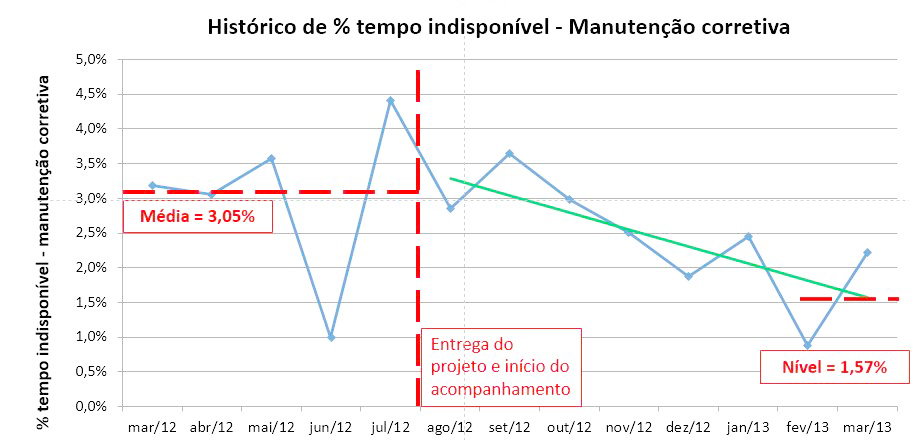
- Redução de 23% nas despesas com peças de manutenção, conforme na figura a seguir:
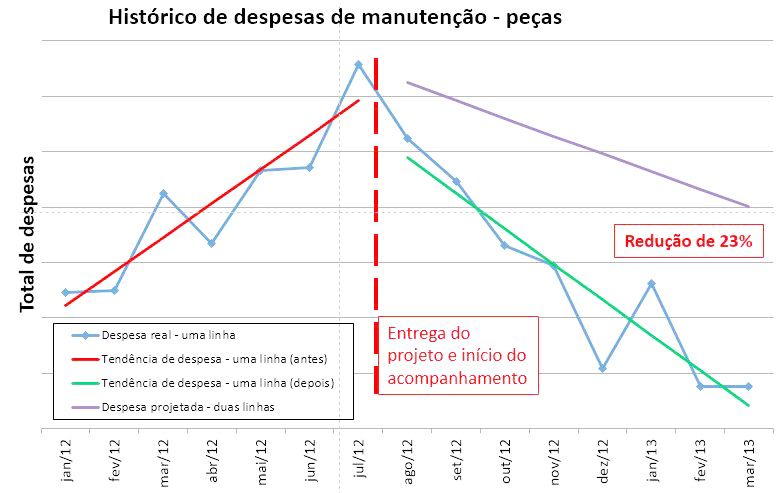
- Redução da ociosidade dos operadores de máquina, que passaram a dedicar 60 horas semanais, antes ociosas, às atividades de MA;
- Redução do quadro de manutenção dedicado à linha;
Além dessa lista de benefícios oriundos de uma metodologia sólida de execução de TPM – pilar MA, a Nortegubisian proporcionou à empresa uma extensa lista de oportunidades de melhoria, tanto no nível de operação, quanto no de gestão de seus processos, firmando uma parceria extremamente benéfica e duradoura.
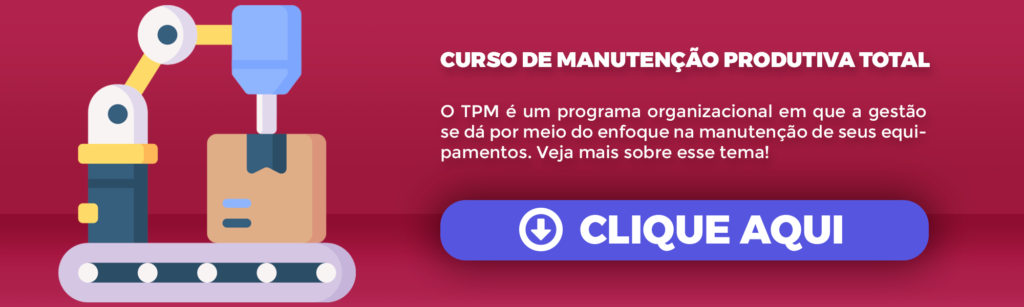
Se você gostou deste case, não deixe de nos seguir nas redes sociais e conferir outros conteúdos relevantes. Estamos no LinkedIn, Facebook, Instagram e YouTube!