Contextualização
No início de 2022 a Nortegubisian iniciou mais uma jornada para implementação do seu Programa de Excelência Organizacional (PEx), em uma empresa do segmento de tecnologia e logística.
A empresa, foco do trabalho, possui mais de 20 anos de experiência no mercado e destaca-se não apenas pela implantação de soluções tecnológicas, como também em logística e prestação de serviços para a indústria de Meios de Pagamento, Captura de Transações e diversos outros nichos e segmentos.
Com matriz em São Paulo e representantes nos principais mercados do país, a empresa dispõe de uma área operacional de mais de 2.000 m² e é considerada a maior operadora de POS (Points of Sales) do Brasil, contando com mais de 2.000 colaboradores. Possui cobertura em todo território nacional com empresas parceiras de transportes e embarques aéreos e sistema próprio de operador logístico, tornando as respostas mais rápidas (70% dos atendimentos são realizados em D+1).
Além disso, possui um ecossistema com soluções diversas e integradas e hiper foco em inteligência logística, permitindo a realização de mais de 400 mil movimentações mensais em 220 pontos de distribuição.
O desafio do projeto estava pautado na criação de um ambiente propício para o desenvolvimento de melhorias e que fosse capaz de expandir a visão crítica e analítica das equipes para identificação de oportunidades de melhoria que, por sua vez, pudessem gerar resultados consistentes. O objetivo era promover um saving de R$1.000.000,00 em um ano de programa.
Nesse âmbito, foi necessário a definição de um plano de trabalho robusto que contemplasse os métodos e ferramentas Lean que seriam aplicadas nas áreas, com foco no ambiente operacional, e um plano de capacitação acelerado dos colaboradores chave da empresa para que pudessem contribuir no diagnóstico e desenvolvimento das oportunidades de melhoria.
Metodologia da Implementação do PEx
O método utilizado para implementação do Programa seguiu as seguintes etapas:
- Sensibilização das equipes: o trabalho teve início com uma sensibilização de todos os colaboradores da empresa quanto ao objetivo do programa, os seus benefícios tanto para empresa quanto para os próprios colaboradores e a necessidade da participação e contribuição de todos com o programa. Essa etapa inicial foi de fundamental importância para garantir o engajamento de todos. A Figura a seguir apresenta um desses encontros de sensibilização das equipes.

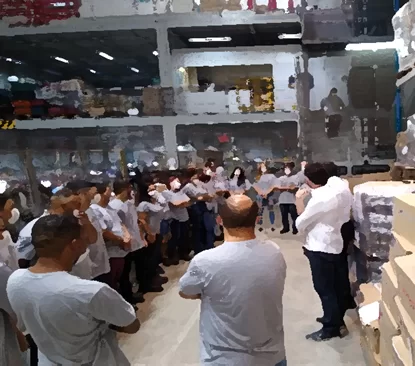
2. Estruturação do escritório de melhorias interno: nesta etapa foram definidos os recursos que seriam dedicados exclusivamente para o programa de melhoria (escritório Lean) e dos demais participantes de outras áreas (equipe multidisciplinar) com atuação parcial no programa. A construção de um time forte e engajado com o propósito, foi essencial para o sucesso do programa.
Nesta fase definiu-se também o formato das reuniões de cadência semanais, cujo objetivo era avaliar o andamento do programa, discutir oportunidades de melhoria, priorizar projetos e avaliar eventuais dificuldades. A criação desta cadência de responsabilidades foi essencial para colocar ritmo na execução.
3. Mapeamento geral da empresa: nesta etapa foi realizado um mapeamento macro da organização com foco na identificação dos processos, número de colaboradores e principais dificuldades e desafios enfrentados por cada setor. Este mapeamento preliminar, mesmo que ainda superficial, foi de fundamental importância na definição do potencial de melhorias que cada área dispunha e, portanto, crucial na priorização de quais áreas deveriam ser trabalhadas em primeira instância.
4. Definição da trilha do conhecimento e capacitação das equipes: para que fosse possível criar multiplicadores das práticas Lean Thinking, auxiliando não apenas na identificação das oportunidades de melhorias, mas também na manutenção das boas práticas implementadas, foi necessário realizar treinamentos intensivos com os colaboradores da empresa, em todos os turnos de trabalho.
A capacitação considerou temas específicos para cada público-alvo conforme foi especificado na trilha do conhecimento estabelecida. A tabela a seguir apresenta a trilha de conhecimento estruturada para o primeiro nível de maturidade Lean do programa.
Faixa | Módulo | Público-Alvo | Carga Horária |
Nível de Qualificação | Introdução ao Lean e conceitos básicos de melhoria | Todos | 1,5 |
5 sensos da qualidade | Todos | 2 | |
Mapeamento de processos (VSM) | Líderes | 4 | |
Fluxo Contínuo e Trabalho Padrão | Líderes | 3 | |
Planos de ação Kaizen | Todos | 1,5 | |
Gestão à Vista e Cadência de Responsabilidades | Líderes | 1,5 | |
Gestão do Conhecimento – Matriz de Habilidades | Líderes | 1 |
A meta estabelecida para o primeiro ano de programa era formar 140 colaboradores considerando a trilha de conhecimento para o primeiro nível de maturidade Lean.
A Figura a seguir ilustra uma das sessões de treinamento aplicadas aos colaboradores da empresa.
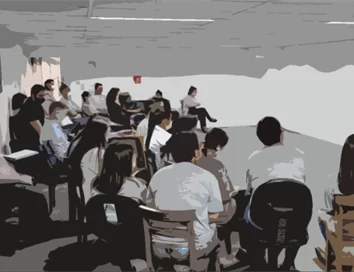
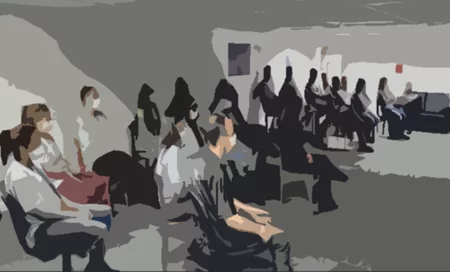
5. Definição do roadmap de implementação de melhorias: esta foi a fase de definição das ferramentas a serem aplicadas e dos entregáveis de cada área participante da imersão, ao término do primeiro ano de jornada. Ao todo foram estabelecidos 10 entregáveis:
a. Mapeamento de processos (VSMs e Fluxogramas) e identificação de oportunidades de melhoria com vistas aos 8 desperdícios Lean.
b. Oportunidade de melhoria priorizadas e com contramedidas direcionadas por meio de eventos Kaizen.
c. Capacitação das equipes na trilha do conhecimento estruturada.
d. Revisão de Layout com o uso do diagrama de Spaguetti para otimização do fluxo de trabalho.
e. Aplicação dos 5 sensos da qualidade (5S): utilização; ordenação; limpeza; saúde; segurança; bem-estar e padronização; e autodisciplina.
f. Apuração dos resultados quantitativos e qualitativos.
g. Estruturação de procedimentos e instruções de trabalho para os processos otimizados.
h. Aplicação de treinamento aos colaboradores em suas respectivas funções com base nos procedimentos e instruções de trabalho (novos ou revisados).
i. Definição gestão diária, incluindo quadros de gestão à vista, especificação de indicadores de desempenho e suas respectivas metas e pauta dos assuntos a serem abordados nas reuniões.
j. Implementação de melhorias relacionadas a gestão a vista da área, indo além dos quadros, e contemplando também placas de identificação dos postos de trabalho, identificação dos corredores de circulação, entre outros.
k. Estruturação de um book contendo o descrito de como o Lean deve operar no setor, incluindo requisitos auditáveis
6. Lançamento do programa de ideias: para impulsionar a captação de ideias de melhoria para o programa, foi estruturado e formalizado um programa de ideias para que os colaboradores pudessem contribuir de forma mais ativa. As ideias sinalizadas eram avaliadas pelo escritório de melhorias e as que apresentassem viabilidade operacional e financeira eram convertidas em Kaizens. A meta estabelecida para o programa foi de desenvolver no mínimo 70 kaizens durante o primeiro ano do programa.
7. Definição da ferramenta de gestão das ações de melhoria: dada a magnitude da empresa, do programa e do número de ações de melhoria a serem gerenciadas concomitantemente, foi necessário definir e parametrizar uma ferramenta eletrônica de gestão de ações e seus respectivos status, primordialmente: em andamento, concluídas e atrasadas. A decisão foi por adotar um software totalmente web denominado Monday que já estava em implementação na empresa para outras finalidades.
Esta ferramenta além de ser um gerenciador de ações e atividades, ainda permite a automação de alguns fluxos de trabalho e foi essencial para a nossa jornada, principalmente considerando que havia membros da equipe que ficavam fisicamente em outras localidades. A Figura a seguir traz uma ilustração de um quadro estruturado no referido software para gestão das ações de melhoria.
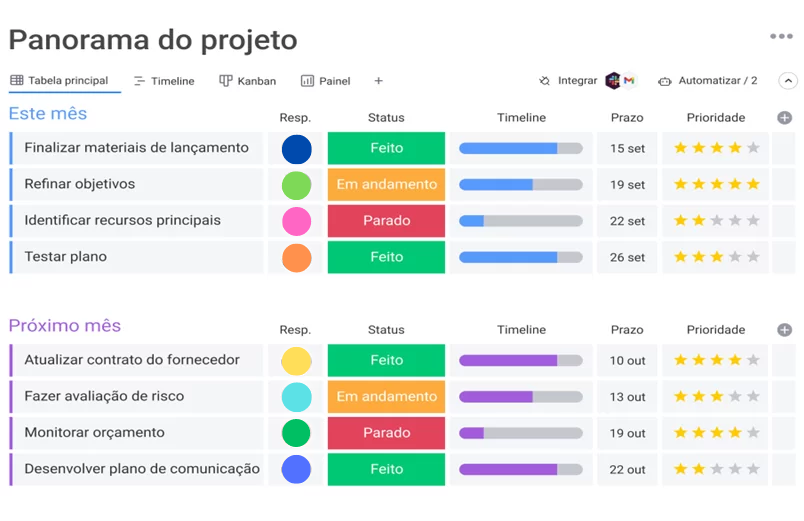
8. Incursões de melhoria: com toda estrutura do programa criada e os colaboradores sendo treinados, iniciou-se o processo de imersão nas áreas priorizadas com o objetivo de mapear os processos em detalhes, identificar, implementar e gerenciar as oportunidades de melhoria diagnosticadas, garantido otimizações de fluxo, melhoria da qualidade dos serviços prestados, ganhos de ergonomia para os colaboradores (da área operacional) e principalmente reduções de custos que pudessem viabilizar o atingimento da meta de saving estabelecida anteriormente.
As incursões foram pautadas no roadmap apresentado anteriormente e os responsáveis por conduzir cada incursão foram estabelecidos de forma que houvesse uma mescla entre a consultoria e os membros do escritório de melhorias interno, além da participação dos demais recursos com atuação parcial no programa. O tópico seguinte apresentará uma síntese das iniciativas e principais resultados alcançados com as incursões.
Principais Iniciativas e Resultados
Otimização do processo de recebimento
- Redução de Headcount: ao mapear o processo de recebimento, identificou-se que havia oportunidades de melhoria relacionadas ao correto dimensionamento do número de colaboradores para atender a demanda e consequentemente o takt time do processo. Diante desta constatação, decidiu-se por realizar um ETM – Estudo de Tempos e Métodos para avaliar a hipótese.
Ao término do estudo foi possível comprovar a tese de que o número de colaboradores (15 considerando os 3 turnos de trabalho) alocados para o processo estava acima da necessidade atual.
A Figura a seguir apresenta o resultado do estudo, evidenciando o gap entre o tempo de ciclo efetivo e o takt time.
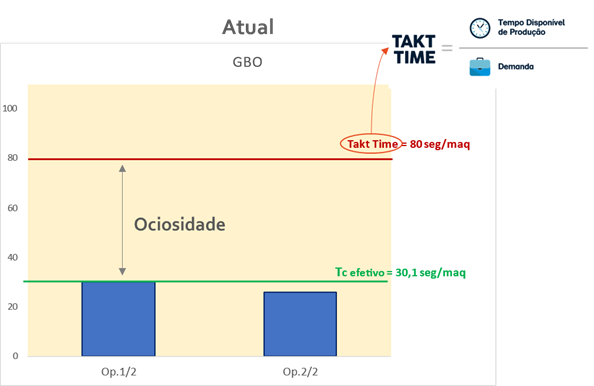
Com a adequação do número de colaboradores ao takt time do processo, associado a outras melhorias de fluxo, foi possível reduzir 7 colaboradores no processo já considerando um percentual de aumento da demanda para os períodos subsequentes. A Figura a seguir apresenta o cenário otimizado que fora prototipado.
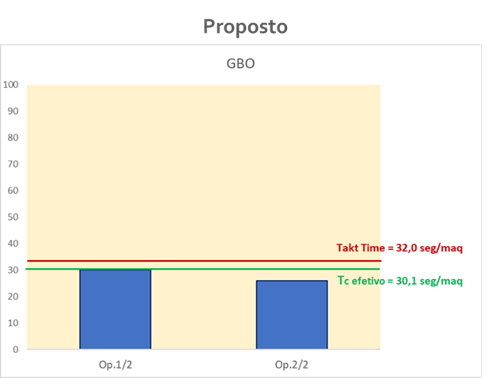
- Saving anual de R$323.000,00: a adequação dos recursos ao tempo takt, associado a criação de quadros de gestão a vista e dashboards automáticos para apoiar as tomadas de decisão, possibilitou a geração de um saving de R$323.000,00 anuais, considerando salários, encargos e demais benefícios.
Um ponto importante a ser salientado é que os 7 colaboradores reduzidos não foram demitidos da empresa, mas sim remanejados para outros setores que demandavam contratação. Este é um aspecto extremamente relevante a ser considerado em qualquer programa de melhoria, pois uma demissão oriunda de uma ação de melhoria pode gerar resistências e barreiras na implementação de outras iniciativas.
A melhor estratégia aqui é deixar que o turn over da empresa se encarregue de equalizar o número de colaboradores, ou seja, direcionar esses colaboradores sobressalentes para novas vagas ou para vagas em que houve uma demissão voluntária ou involuntária.
Otimização do processo de pintura
- Redução de 62,7% do tempo de preparação: o processo de preparação consiste no envelopamento do produto para que possa seguir para a cabine de pintura, de forma que a tinta possa ser aplicada apenas nas partes adequadas, evitando que o equipamento seja danificado. Trata-se de um processo moroso, minucioso e artesanal (realizado praticamente 100% de forma manual). Além disso, representa uma atividade de espera para execução do processo de pintura, portanto, trata-se de uma atividade Não Agregadora de Valor (NAV). Outro complicador é que este tempo NAV é duplicado, pois ao retornar do processo de pintura, o equipamento precisa ser desenvelopado.
Diante disto, foram conduzidos estudos para avaliar formas diferentes e mais eficientes de se realizar a vedação dos equipamentos, incluindo a adoção de borracha líquida. Houve revisão de Layout, substituição dos instrumentos utilizados para vedação e padronização das boas práticas. Estas ações conjuntas geraram na média, considerando os modelos que mais passam pelo processo de recuperação estética, uma redução de 62,7% do tempo de preparação.
- Aumento de 300% da produtividade: já com relação a cabine de pintura, não havia uma estrutura adequada para realização do processo e por este motivo era necessário realizar o processo em etapas. A parte superior era pintada sobre uma bancada. Ao término, era necessário esperar a tinta secar (tempo de cura) e só depois a pintura das outras partes do equipamento poderia ser realizada. A principal melhoria implementada foi a adoção de gancheiras, que permitiu que os equipamentos fossem pintados integralmente de uma única vez, agilizando o processo, eliminando a etapa de espera e aumentando substancialmente a produtividade do setor.
- Alteração e padronização do processo de pintura: buscando a redução de retrabalhos por craquelamento da tinta, workshops e treinamentos foram realizados com especialistas da área, onde foi possível observar as boas práticas utilizadas no mercado e trazê-las para a realidade da empresa, reduzindo assim o retrabalho e promovendo o aumento da qualidade dos itens pintados na cabine de pintura.
- Saving de R$ 276.618,03 para o período aferido: o principal indicador do setor era mensurado com base no resultado financeiro, calculado entre a diferença da receita gerada pelo setor no mês e o seu custo mensal.
Antes da implementação das melhorias, o setor criado em 2020, nunca havia alcançado a meta mínima e que representava o ponto de equilíbrio e, por este motivo, acumulava prejuízos recorrentes. Os resultados antes da implementação das melhorias são apresentados na Figura a seguir.
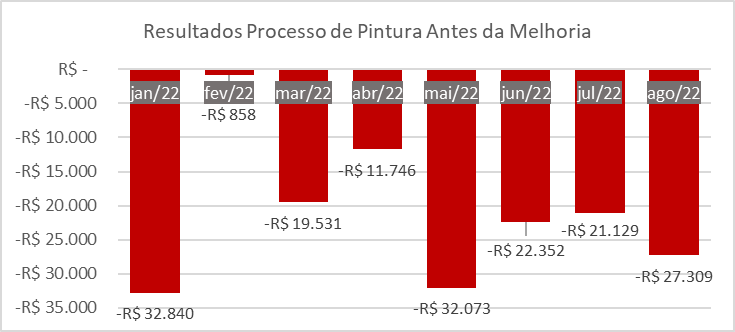
Após a implementação do pacote de melhorias, os resultados rapidamente alcançaram o ponto de equilíbrio e seguiram em tendência de crescimento nos meses subsequentes, gerando lucros de forma recorrente e consistente. A Figura a seguir apresenta os resultados após a implementação do pacote de melhorias sinalizado.
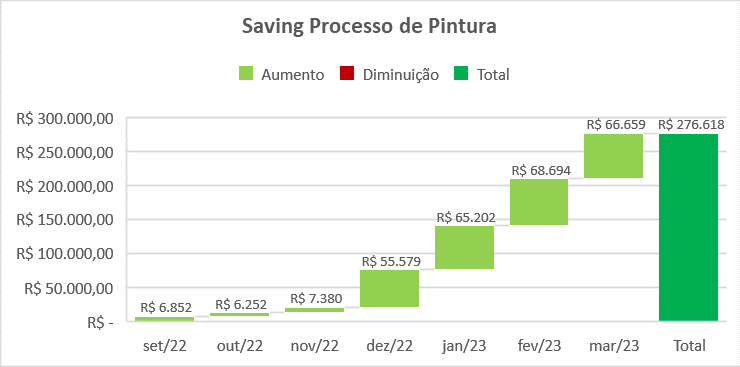
- Ganhos em ESG: com a alteração do modelo de trabalho, foi possível reduzir o consumo de energia da cabine de pintura (em torno de 50%), direcionando a entrada e saída de ar para pontos específicos da cabine, além de reduzir o consumo de solventes.
Otimização do processo de montagem de kit
- Redução de movimentação e superprodução: anteriormente, o processo de montagem de caixas para alocar as máquinas e seus componentes era realizado em um espaço separado da linha de montagem. Com a alteração do sequenciamento produtivo de montagem de kit, essas caixas passaram a ser montadas como linha, no momento da necessidade, reduzindo assim a movimentação dos operadores para transportar as caixas até a posição de uso, além de reduzir a quantidade de caixas produzidas antes da necessidade (Work in Process).
- Aumento de produtividade em 30% e saving anual de R$184.766,4: uma das principais melhorias aplicadas no processo de montagem, envolveu também o balanceamento de atividades por meio da aplicação do ETM, onde foi possível constatar ociosidade em algumas etapas do processo, alta flutuação e movimentações desnecessárias. A Figura a seguir apresenta o Gráfico de Balanceamento de Operações (GBO), evidenciando as referidas constatações.
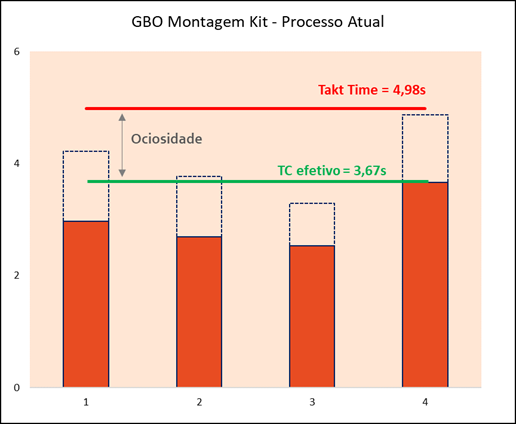
Além da adequação do número de colaboradores para atendimento do takt time, os procedimentos foram revisados e um novo Layout foi proposto, incluindo a substituição da estrutura atual de montagem por uma modular, com esteiras manuais de roletes conectando os postos de trabalho, o que eliminou o deslocamento de colaboradores para movimentação de materiais. A Figura a seguir apresenta o novo Layout concebido para o setor.
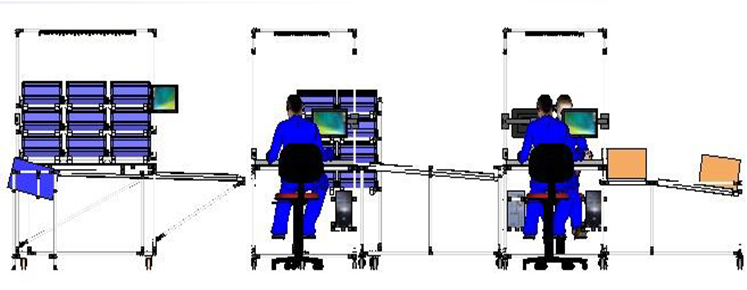
O pacote de melhorias implementadas garantiu um aumento de produtividade na ordem de 30% e um saving decorrente da equalização da mão de obra, na ordem de R$184.766,40 anuais.
Otimização do processo de expedição
- Melhoria na gestão e controle de não conformidades: anteriormente não existiam registros de não conformidades dos itens que eram recebidos pelo setor de expedição e que só eram observados no momento do picking. No novo processo estruturado, todos os operadores passaram a ter acesso a um formulário para apontamento das não conformidades do dia e, juntamente com o líder e o supervisor da área fornecedora, passaram a discutir formas de melhorar continuamente o processo.
- Alteração do layout produtivo: buscando uma melhor organização da área e aumento da área disponível para alocação de paletes para o picking, um novo layout foi proposto para otimização do fluxo produtivo. A Figura a seguir ilustra o novo layout proposto.
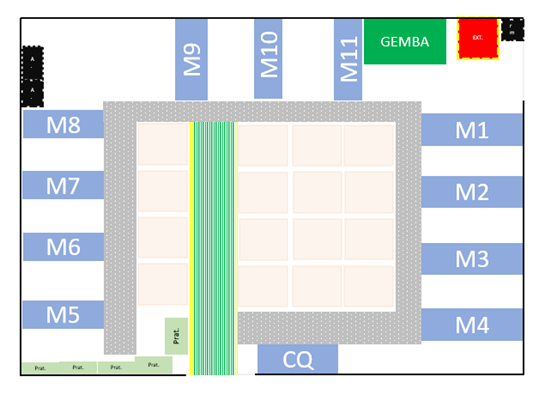
- Redução do tempo de carregamento em 33%: antes da implementação das melhorias no setor, a transportadora, ao chegar na doca para carregar o veículo, precisava ficar aguardando um tempo demasiado para que a equipe de expedição pudesse disponibilizar os volumes a serem carregados. Este tempo demasiado era muito em função de falhas na programação e pela dificuldade de localizar os paletes que deveriam ser direcionados para cada transportadora e região.
Diante deste cenário, as principais melhorias desenvolvidas foram, o estabelecimento de uma programação com separação em D-1 e a adoção de regras de gestão a vista que consistiram em estabelecer uma cor para cada transportadora e a padronização das cores das etiquetas e das posições paletes para o acondicionamento dos materiais já separados e prontos para embarque.
Com a implementação destas ações, o tempo médio de espera por transportadora que era na ordem de 1 hora e 40 minutos caiu para 1 hora e 8 minutos, representando uma redução de 33% do tempo de espera.
- Aumento de 70% de produtividade no processo de conferência: outra melhoria de grande impacto foi a adoção de QR Code para identificação de caixas master no processo de conferência de volumes provenientes da operação. Anteriormente, a leitura dos códigos de barra era realizada individualmente, ou seja, os colaboradores abriam a caixa master e realizavam a leitura individual de cada umas das caixas.
Com a adoção do QR-Code, ao fazer a leitura da caixa master, todos os itens acondicionados nela são automaticamente registrados via sistema, dispensando a leitura individual dos volumes (bipagem única).
O conjunto de alterações aplicadas no processo fez com que a produtividade mensal por colaborador, saísse de uma média de 10.000 máquinas para 17.000 máquinas, o que representa um ganho de produtividade de 70% em apenas 2 meses.
Otimização do envio para laboratório externo
- Redução de 47% do tempo de espera para gerar NF superior a 1 dia e em 96% superior a 4 dias: o antigo processo de solicitação de emissão de nota fiscal para a saída das máquinas que seriam direcionadas aos laboratórios parceiros, tinha uma média de 3 dias de espera, podendo chegar em alguns casos em até 13 dias. Além do não atendimento da meta e interrupção do fluxo, este cenário ocasionava um acúmulo excessivo de materiais parados, o que era extremamente crítico considerando as restrições de espaço.
Ao mapear o processo, observou-se que este tempo de espera era ocasionado principalmente por uma ausência de integração entre os sistemas de informações que eram utilizados pela equipe de envio para laboratório e financeiro. Com a integração dos sistemas, o novo cenário apresentou uma redução de 96,80% no tempo de espera superior a 4 dias e em 47,07% para esperas superiores a 1 dia para geração de NFs.
- Redução de 62% do tempo médio para recebimento da NF: com a melhoria implementada e citada anteriormente, o tempo médio para geração das NFs que era de 3 dias (e podia chegar em até 13 dias) foi reduzido para 1,14 dias, o que representa uma redução de 62%.
- Balanceamento das operações e economia de R$370.000,00 no ano: além das melhorias de sistema, foi realizado também uma alteração importante no processo. As atividades que eram realizadas em um setor único (envio para laboratório externo) foram integradas à linha de triagem em um modelo de fluxo contínuo, reduzindo os estoques intermediários e o Lead Time do processo. Para que esta implementação fosse possível houve a necessidade de realizar o balanceamento do processo. Todas estas ações integradas permitiram a redução de 7 colaboradores, gerando um saving anualizado de R$370.000,00
Otimização da logística de entrega
- Redução de R$ 190.000,00 no custo anual com fretes: anteriormente o processo de expedição estava dimensionado exclusivamente para que pudesse realizar as entregas no menor tempo possível. Uma análise de custos versus o atendimento dos SLAs impostos pelos clientes foi direcionada para que se vislumbrasse oportunidade de otimização de frete.
Identificou-se então que era possível realizar a consolidação de algumas cargas em alguns dias específicos da semana para os estados do Norte, Nordeste e Centro-Oeste. As alterações na programação (grade de expedição) possibilitaram uma redução de 27,8% do número de viagens, gerando um saving anualizado de R$190.000,00 sem qualquer tipo de impacto nos prazos SLAs estabelecidos em contrato com os clientes.
Outras iniciativas trabalhadas
- Revisão do Layout – cenário galpão atual: revisão do layout considerando o galpão atual e suas dimensões. Utilizou-se primeiramente um desenho 2D para análise do fluxo de movimentação (diagrama de Spaguetti) e posteriormente, com a versão 2D validada, foi elaborada também a versão em 3D. As Figuras a seguir apresentam algumas imagens ilustrativas.
Visão 2D
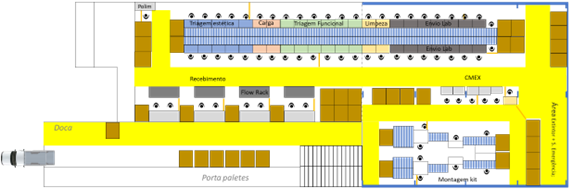
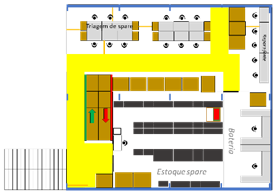
Visão 3D
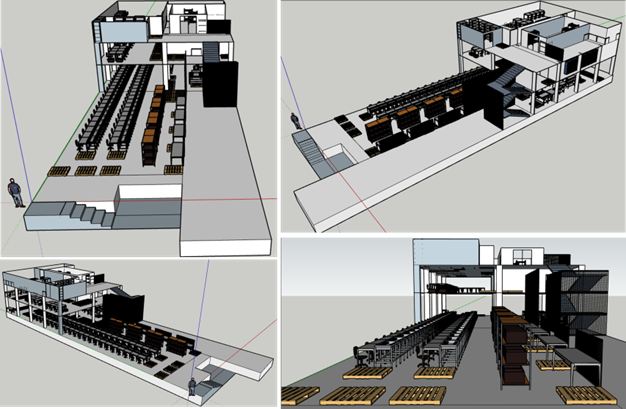
- Dimensionamento de linha de operação: para otimização do fluxo produtivo foi prototipada a linha de operações em fluxo contínuo, permitindo a eliminação de esperas entre etapas e de estoques intermediários. A Figura a seguir apresenta um desenho técnico do modelo proposto.
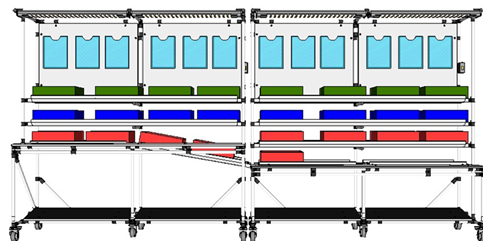
- Proposta de novo Layout: foi elaborada também uma versão do Layout considerando a mudança de operações para um novo galpão. Todas as dimensões do novo espaço foram coletadas para desenho em 2D e análise do fluxo de movimentações (diagrama de Spaguetti). As dimensões do novo espaço permitiram a prototipagem de um Layout horizontal, sem a necessidade de verticalização, que onerava o fluxo de movimentação do galpão anterior (necessidade de empilhadeira para deslocar materiais para as etapas do processo que ficavam alocadas no mezanino). A Figura a seguir ilustra o novo Layout proposto.
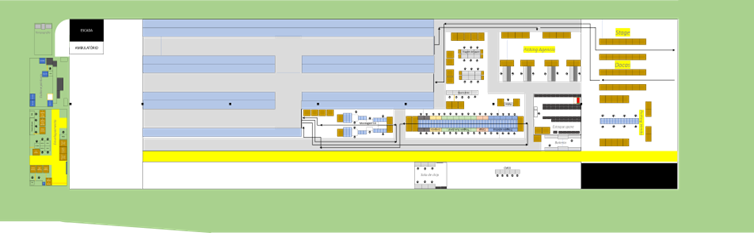
- Estudo de acondicionamento de materiais na estrutura porta paletes do novo galpão: outra iniciativa conduzida foi o estudo para o dimensionamento do número de posições porta paletes para cada tipo/ família de materiais, considerando volume e giro de estoque. Além disso, foi elaborada uma proposta de codificação das estruturas porta paletes. A Figura a seguir ilustra a proposta de divisão e acondicionamento dos materiais na estrutura dimensionada.
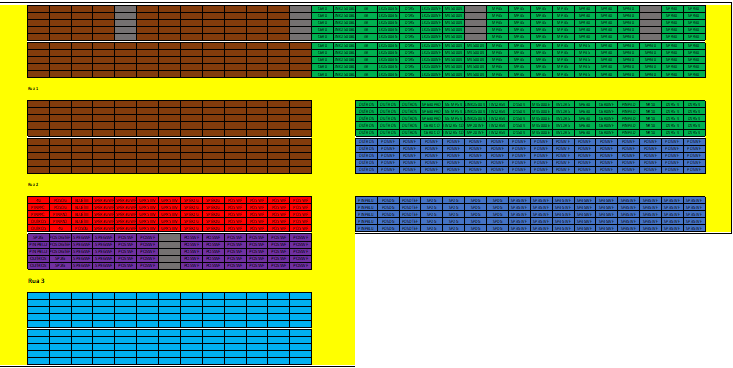
- Parametrização dos estoques de insumos: durante a elaboração da proposta do novo Layout e considerando as restrições de espaço, foi conduzido um estudo para determinar os níveis ideais de estoque para os insumos utilizados na operação. Esta parametrização tende a garantir que haja em estoque apenas o material necessário, nem a mais (ocupação de espaço e capital empatado) e nem a menos (impacto na eficiência da operação). No estudo ficou evidente a necessidade de adequação dos níveis de estoque. A Figura a seguir apresenta o exemplo de um SKU onde pode-se observar uma enorme discrepância entre o estoque médio e o estoque máximo calculado versus o estoque médio atual, indicando oportunidades de equalização dos níveis de estoques de insumos.
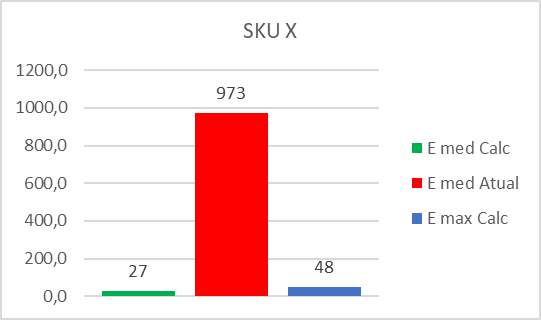
Conclusões e Considerações Finais
Como observado nas sessões anteriores, este foi um projeto bastante intenso, com diversas frentes de trabalho simultâneas, com muitas mudanças e com resultados muito impactantes e transformadores.
No que tange as metas inicialmente estabelecidas, podemos dizer que o projeto foi um sucesso, uma vez que todas as metas foram superadas com êxito.
Após o primeiro ano de implementação do programa foi possível alcançar um saving de R$1.410.974,00 o que representa 41% a mais em relação a meta de R$1.000.000,00 estabelecida inicialmente. A Figura a seguir apresenta o gráfico com os resultados obtidos.
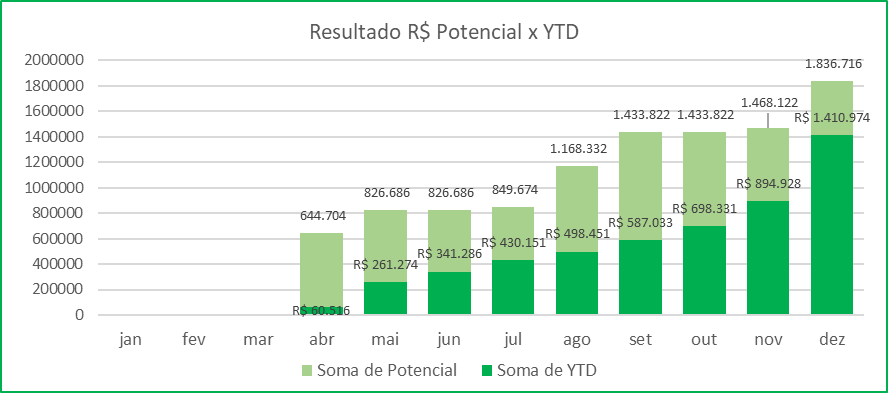
No que se refere as metas de número de Kaizens, também foi possível obter um resultado excepcional, alcançando ao final do período, um número de 346 Kaizens concluídos frente a meta estabelecida inicialmente de 70 Kaizens. A Figura a seguir apresenta um extrato do controle do número de kaizens, evidenciando a extrapolação da meta já em meados do mês de setembro.
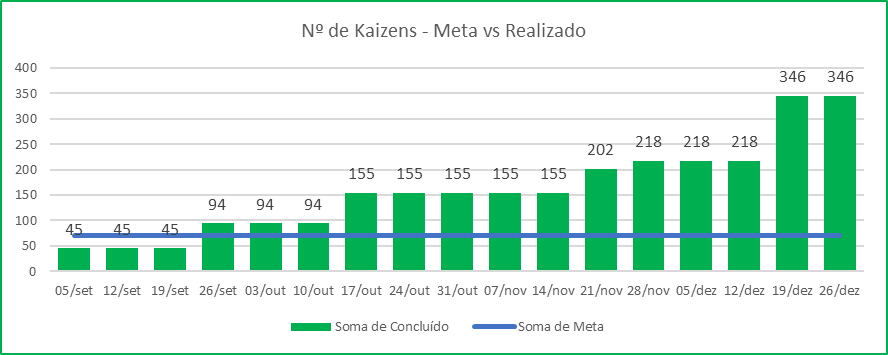
E por fim, mas não menos importante, ao final do primeiro ano do programa também obtivemos êxito na meta de capacitação dos recursos. O objetivo inicial era formar 140 colaboradores considerando a trilha de conhecimento para o primeiro nível de maturidade Lean, e ao final do período conseguimos formar 174 colaboradores, o que foi de fundamental importância para o atingimento das metas anteriores relacionadas ao número de Kaizens e saving gerado. A Figura a seguir apresenta um extrato do controle do número de colaboradores formados no final do período.
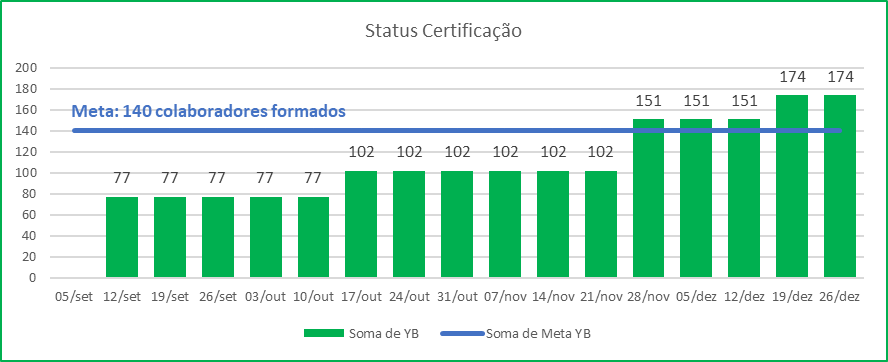
Diante das evidências apresentadas constata-se que o projeto obteve grande êxito em seu primeiro ano de existência.
É importante salientar que todos os resultados apresentados apenas foram possíveis com o empenho e dedicação de todas as partes envolvidas, com a criação de uma sistemática de sustentação, acompanhamento e monitoramento do programa e com o apoio e respaldo da alta direção.
Ainda há muitas melhorias a serem desenvolvidas e um longo caminho a percorrer em direção a excelência, mas já é notória as transformações tanto estruturais quanto de mentalidade e principalmente na cultura organizacional da empresa.
Gostou do nosso artigo sobre PEx? Não se esqueça de acessar nossos outros cases de sucesso e nos acompanhar no Instagram, Facebook e LinkedIn.
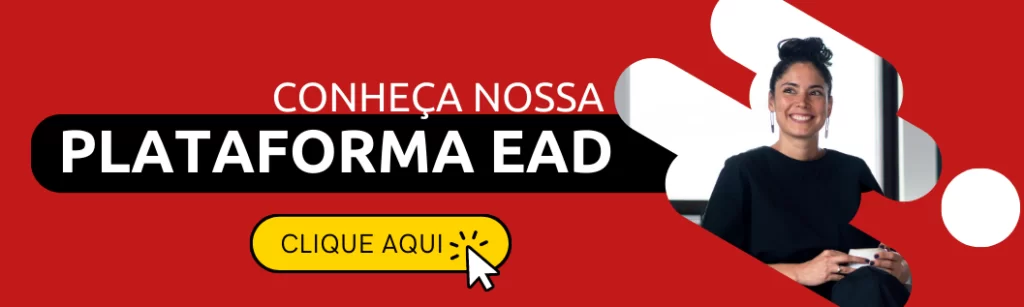