Há mais de 46 anos na área de expedição e atualmente operando com 85 centros de distribuição logísticos localizados em 10 estados do Brasil, a Patrus é uma transportadora de cargas fracionadas B2B (empresa para empresa) e B2C (entrega porta a porta) que utiliza de tecnologia de ponta e de ferramentas Lean para conferir aos seus clientes um atendimento ágil e de qualidade, com segurança no transporte e rastreabilidade sobre sua carga. O objetivo é contribuir para o sucesso dos clientes por meio de soluções inovadoras e personalizadas, gerando valor sustentável a todos.
O trabalho da Nortegubisian com a Patrus Transportes começou em 2017, quando foi escolhida como o parceiro responsável por suportar a implementação da Cultura Lean a nível organizacional. No ambiente administrativo, a implementação do Lean Office foi realizada por ondas.
Em 2020, com o aumento da demanda das compras on-line ou B2C (entrega porta a porta) concluiu-se que era o momento ideal para que a Cultura Lean fosse desdobrada para a expedição, uma área com práticas office, mas muito próxima do operacional, sendo portanto uma área estratégica para garantir a eficiência operacional, pois de nada adiantaria as cargas serem separadas e carregadas de forma eficiente se o veículo tivesse que ficar um tempo demasiado aguardando a emissão dos documentos para seguir viagem.
O Desafio
O desafio da Nortegubisian consistiu em mapear o funcionamento da expedição de uma das plantas da Patrus localizada no estado de São Paulo, aplicar melhorias para alcançar um estado de excelência e então criar um plano de ação para que todos os centros de distribuição do estado possuíssem o mesmo padrão em relação ao modelo mapeado e otimizado.
Vale ressaltar que esse trabalho de nivelamento entre as plantas é de suma importância para garantir que todos as instalações da Patrus trabalhem em sinergia, com adoção de práticas Lean e, portanto, utilizando da melhor forma a tecnologia e os recursos disponíveis.
Mapeamento
O início do projeto consistiu no mapeamento da expedição escolhida: a filial de Campinas. A escolha se deu pelo fato de que a planta é recordista na emissão de CT-es (conhecimentos de transporte eletrônicos, um documento fiscal obrigatório que vincula a nota fiscal do produto à empresa transportadora, informando isso à receita federal) no estado.
Para identificar todas as atividades realizadas pelos colaboradores da expedição de Campinas, foi utilizada a ferramenta SIPOC, a qual consiste em delimitar as fronteiras de cada processo realizado (ou seja, identificar quebras de continuidade dentro da rotina de trabalho), listar tais processos e identificar suas entradas e saídas, com seus respectivos fornecedores e clientes. Combinando o SIPOC com a ferramenta da voz do cliente, é possível identificar as CTQs de cada processo, ou seja, as características críticas para a qualidade, que traduzem quantitativamente a expectativa do cliente sobre cada processo realizado na expedição.
Com base no SIPOC, é possível fazer um desdobramento de cada processo identificado por meio de fluxogramas e VSMs, que é a ferramenta de mapeamento do fluxo de valor, a qual torna visível oportunidades de melhoria dentro do fluxo, tal como estoques intermediários mal dimensionados, excesso de comunicação, falha no nivelamento de conhecimento ou esforço da equipe, entre outros. A partir do levantamento destas oportunidades de melhoria, foi realizada uma priorização para que as ações pudessem ser executadas dentro de um prazo pré-estabelecido. As oportunidades priorizadas foram:
- Criar um painel automático de gestão para o processo de “ler e manifestar CT-es” por meio do Power BI
- Alterar o layout do escaninho (armário fracionado que possui o intuito de armazenar todos os CT-es presentes na filial, sendo que cada fração do armário corresponde a uma filial destino) local da expedição, a fim de tornar mais intuitivo o processo de “guardar CT-es no escaninho” e, assim, aumentar o índice de completo e correto (%C&C) do mesmo.
- Criar um placar envolvente a fim de saber quantas vezes foram encontrados CT-es armazenados no escaninho incorreto através de uma ação preventiva (conferência periódica) ou corretiva (quando um CT-e é perdido e a equipe precisa encontrá-lo de maneira urgente)
- Criar um KPI para explicitar o número de atrasos de viagens dentro do mês devido à falha da expedição
- Estabelecer reuniões diárias de gemba para expor os KPIs da área e buscar a melhoria contínua por meio de uma cadência de responsabilidades.
Desenvolvimento e resultado das ações
1. O processo de “ler e manifestar CT-es” consiste em vincular (via leitor de código de barras), no sistema computacional utilizado pela Patrus, todos os CT-es que serão transportados em determinada viagem. Um CT-e pode corresponder a um único volume ou a um agrupamento de volumes, e, por lei, os documentos físicos precisam ser transportados junto aos seus produtos correspondentes.
Porém, na expedição da Patrus, quem decidia qual seria a específica viagem a qual iria receber CT-es lidos em determinado momento, era o líder da expedição, com base em sua experiência e suas pesquisas feitas diariamente dentro do centro de distribuição. O problema sistêmico que essa tomada de decisão poderia gerar é o fato de que o líder pode errar ou passar desapercebido por algum detalhe. Além disso, 4 homens-hora diários da liderança eram dedicados exclusivamente a essa tarefa.
A solução encontrada foi criar um painel em Power BI que estabelece um ranking de prioridade acerca das viagens que necessitam receber CT-es lidos, eliminando assim todo o trabalho que precisaria ser realizado pelo líder. Critérios de prioridade foram estabelecidos e o painel foi desenvolvido.
O resultado foi a economia de 4 horas/ homem diário da liderança, disponibilizando tais horas para dedicação ao trabalho rotineiro e aplicação e disseminação da cultura Lean por toda a Patrus. Em valores monetários, as 4 horas/ homem economizadas diariamente correspondem a R$1.300,00/mês. A Figura 1 a seguir apresenta um draft do painel de gestão criado em Power BI.
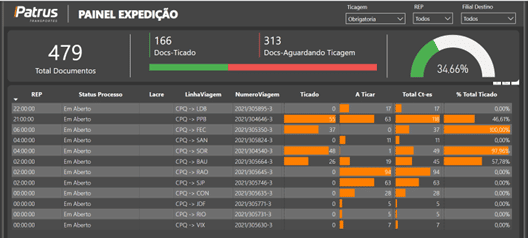
2. O processo de armazenar ou guardar os CT-es no escaninho ocorre após a emissão e conferência dos documentos. Os conhecimentos devem ser guardados um de cada vez em seu “destino” específico (ou seja, na fração do escaninho correspondente à sua filial/cidade destino), para que erros não ocorram. Contudo, antes da alteração de layout, todas as etiquetas que sinalizavam o local específico para cada filial destino, localizavam-se exatamente acima do espaço reservado para armazenagem de CT-es e isso foi uma queixa dos funcionários que não eram tão habituados a armazenar CT-es (o natural, quando vemos uma sinalização, é inferir que ela indica o espaço que está logo acima, e não logo abaixo).
Desta forma, muitos erros de armazenagem de CT-es eram ocasionados em função do layout do escaninho, o que fomentou a mudança das etiquetas para a posição exatamente abaixo do espaço reservado para armazenagem de CT-es.
Os resultados qualitativos dessa mudança foram explicitados pelos colaboradores, que relataram uma menor incidência de erros na armazenagem dos documentos e maior agilidade na execução do processo.
3. A criação de um placar envolvente a fim de mostrar para o time a quantidade de vezes em que um ou mais CT-es foram encontrados no escaninho incorreto, foi fundamental para criar um senso de responsabilidade nos colaboradores. A própria exibição do placar já contribui para uma diminuição nas “ações corretivas”, que é o nome dado ao ato de “encontrar um CT-e no escaninho errado de forma emergencial”, e aliando isso à mudança no layout do escaninho, concluiu-se que a tendência das ações corretivas se direcionou para o número 0, ao passo que as ações preventivas (encontrar um CT-e no escaninho errado ao realizar uma inspeção preventiva/periódica no escaninho) se estabilizaram em 2 ações por dia.
A explicação para tais números consiste no fato de que o time está executando o trabalho de “guardar” os conhecimentos no escaninho de forma muito mais organizada e com maior atenção, por isso as ações corretivas tenderam a 0, além disso, como erros são inevitáveis durante o processo, cerca de 2 ações preventivas ocorrem por dia, encontrando inconsistências no escaninho logo após o seu surgimento.
4. A criação de um KPI para explicitar o número de atrasos de viagens dentro do mês devido a falhas da expedição foi fundamental para que, ao analisar os números, os colaboradores pudessem criar um senso de responsabilidade e compreender o impacto da não realização do processo conforme o padrão estabelecido. Com a exposição desse indicador, os atrasos devido a falhas de expedição rapidamente zeraram, vide que o time desenvolveu o senso de urgência para liberação de viagens dentro dos horários programados.
5. A criação das reuniões de gemba (no local de trabalho) foi um passo importante que permitiu o estabelecimento de uma rotina para analisar a produtividade do dia anterior, parabenizar a todos em caso de sucesso e debater eventuais atrasos na liberação de viagens. Esta reunião representa uma oportunidade para buscar melhorias a fim de tornar o processo mais ágil e, assim, buscar cada vez mais a excelência.
Considerações finais
Todas as ações trouxeram também um ganho qualitativo aos processos da expedição de Campinas, os quais foram percebidos pelos clientes e traduzidos no resultado de um MFA (Market Feedback Analysis), uma espécie de uma pesquisa de satisfação direcionada aos clientes internos do processo). Perguntou-se, o grau de satisfação com cada processo realizado pela expedição de Campinas e, em uma escala de 1 a 5, a resposta média obtida foi de 4,4, o que superou a meta inicial da equipe de 4,1.
Além disso, foram criadas LUPs (Lição de Um Ponto) para cada um dos processos a fim de consolidar e formalizar o conhecimento dos colaboradores acerca das atividades. Complementarmente, foi estruturada uma matriz de habilidades sinalizando o grau de conhecimento de cada colaborador em relação a cada um dos processos mapeados na expedição. Esta ferramenta permitiu a identificação de gaps de conhecimento da equipe e servirá de guia para o desenvolvimento da equipe de expedição.
Uma vez consolidada todas essas melhorias e boas práticas, documentadas por meio dos fluxogramas e LUPs, criou-se um roadmap para que o coordenador coorporativo pudesse replicar o modelo de Campinas para todas as filiais do estado de São Paulo.
Um plano de ação A3 foi estruturado para contemplar as ações e o cronograma de implantação das práticas Lean nas demais filiais. Neste âmbito, a missão da Patrus, especificamente da equipe de expedição, é nivelar as filiais do estado de São Paulo a fim de replicar o padrão de excelência desenvolvido em Campinas. Além disso, outros dois desafios deverão ser trabalhados:
- Eliminar emissões manuais de CT-es nas filiais. Durante o mapeamento, identificou-se que muitas filiais ainda realizavam a emissão dos CT-es de forma manual, o que representa mais morosidade para o processo e uma maior probabilidade de ocorrência de falhas. A principal causa diagnosticada foi associada ao desconhecimento de ferramentas já disponibilizadas, treinamento da equipe e padronização a nível corporativo.
- Criar uma central de resolução de problemas e dúvidas que dizem respeito às expedições, algo que hoje é centralizado na equipe de tráfego. Esta iniciativa permitirá um atendimento mais ágil e assertivo. Além disso, assim como previsto no plano de ação A3, futuramente esta área poderá exercer a função de um centro compartilhado, onde processos que hoje são realizados individualmente em cada filial poderão ser centralizados com a atuação de equipes dedicadas e especializadas, permitindo assim uma economia considerável de recursos.
Se identificou com o assunto e gostaria de ter uma solução semelhante para a sua empresa? Então, entre em contato conosco! A Nortegubisian está preparada para buscar soluções para o seu negócio. Nos acompanhe também no Instagram, Facebook e LinkedIn para ficar sempre por dentro das novidades.