Com mais de 60 anos de trajetória, uma das maiores empresas do Brasil no ramo de nutrição vegetal está em franco crescimento.
No contexto de pandemia, a fábrica brasileira se viu diante de um desafio onde a empresa aumentou sua carteira de clientes e passou pelas seguintes dificuldades: como adaptar todo o fluxo logístico para os crescentes volumes de produção? Quais são as mudanças necessárias para garantirmos que, mesmo em épocas de pico, a expedição de materiais não será afetada, ao mesmo tempo que não teremos um entrave no recebimento de nossas matérias-primas?
Foi através desses questionamentos que o projeto de Plano Diretor Logístico em parceria com a Nortegubisian começou!
Desenvolvimento do projeto
O projeto iniciou com um mapeamento de todos os fluxos AS IS de material dentro da planta produtiva com o auxílio da ferramenta Diagrama de Spaghetti, que permite visualizar toda a trajetória dos materiais e identificar desperdícios de Movimentação e Transporte, Gargalos e Estoques Intermediários. No In loco também foram coletadas informações de tipos de armazenagem utilizados, equipamentos de movimentação e os locais de armazenagem de Matérias Primas, Produto Acabado e Embalagens.
Em seguida, para conseguir mensurar essas movimentações, foi realizado um Estudo de Tempos e Métodos (ETM), sendo então possível analisar a ocupação atual dos equipamentos de transporte. Além disso, foi coletado também todo o histórico de recebimento, expedição, consumo de matérias-primas (MP) e produção de produto acabado (PA), bem como as projeções de crescimento desses números.
A partir de uma robusta análise desses dados, a Consultoria pôde chegar no diagnóstico de que manter o layout atual iria sobrecarregar os equipamentos, além de travar o fluxo em pontos estratégicos da fábrica, como o abastecimento da produção. Dessa forma, partimos para o desenho do fluxo TO BE.
Para isso, o trabalho foi separado em 2 frentes:
1. Fluxos Inbound e Outbond
Layout Macro
A primeira oportunidade de melhoria identificada foi a pulverização dos locais de armazenamento de matérias-primas. A planta possuía diversos galpões ao redor da unidade produtiva, que acabaram sendo construídos de forma emergencial, e dificultava o fluxo de material. A centralização em um armazém de Matéria Prima e outro de Produto Acabado permitiu a criação de um fluxo logístico muito mais lógico e otimizado, conforme vamos abordar ao fim desse tópico.
Equipamentos de Movimentação
Uma segunda oportunidade identificada foi a melhoria dos equipamentos de movimentação, visto que a fábrica utilizava equipamentos inadequados para transporte de distâncias consideravelmente longas. Assim, a Nortegubisian trouxe para o projeto alternativas para o transporte de materiais à granel e ensacado, que têm potencial de gerar grandes ganhos de produtividade nas movimentações, além de redução de custos devido a menor frequência necessária e o menor desgaste dos equipamentos.
Na imagem abaixo, está disposto um dos equipamentos sugeridos para o transporte de bags de MP e PA dentro da planta. Trata-se de um rebocador industrial de vagões.
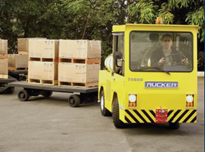
Além disso, é claro, a rota dos equipamentos de movimentação foi sugerida de modo a otimizar os fluxos. Segue abaixo um exemplo de fluxo desenhado para o rebocador.
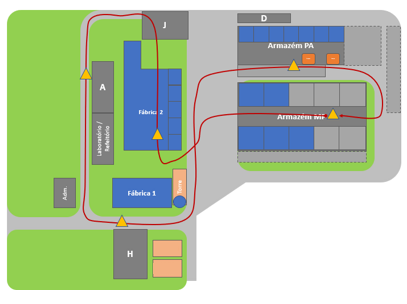
O fluxo desenhado acima permite um alto ganho de produtividade nas movimentações entre os armazéns de MP e PA e a unidade fabril, devido ao fato de que em nenhum trecho o caminhão transitará descarregado. Apesar disso, algumas alterações estruturais seriam necessárias para possibilitar esse fluxo.
Outra sugestão para otimizar o fluxo logístico foi a instalação de talhas para facilitar o abastecimento de MP no processo produtivo. Até então, essa atividade vinha sendo realizada com a ajuda de 2 equipamentos (e consequentemente 2 funcionários) de movimentação simultaneamente, ocupando-os desnecessariamente. Além disso, o método gerava altas quantidades de perda de material, portanto foi considerado inadequado. A talha permite a fácil manipulação do material apenas com a presença de um operador.
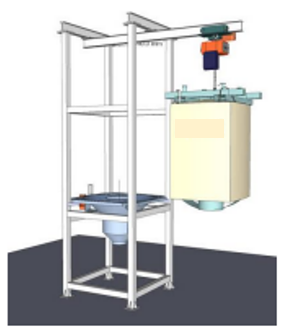
Por fim, com essas otimizações, dentre outras, foi possível dimensionar o estado futuro. A partir disso, os volumes de produção esperados para 2022 e 2023 caberiam tranquilamente no novo fluxo logístico da planta.
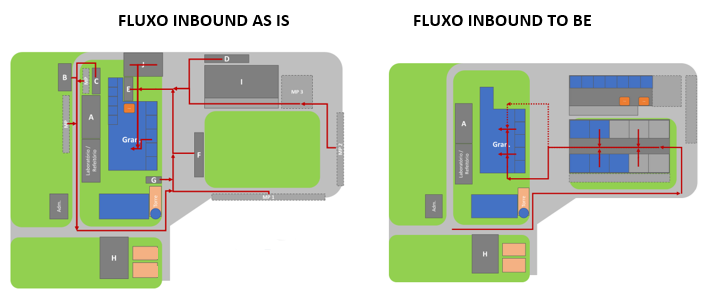
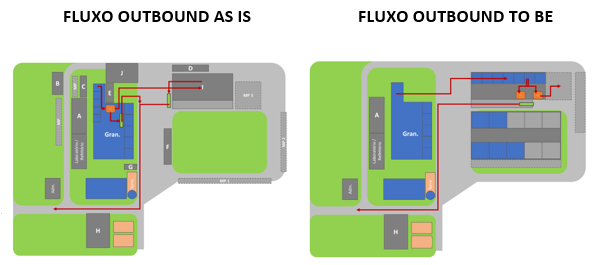
2. Armazenagem de Matérias Primas e Produto Acabado
Com o aumento de volume de produção, o estoque tanto de matéria-prima quanto de produto acabado deve acompanhar este aumento, mantendo a chamada cobertura de estoque: o índice que mede o tempo que o meu estoque consegue cobrir as futuras demandas do meu cliente. Para garantir isso, foi sugerido um método de armazenagem chamado Drive-In, que permite um alto aproveitamento de espaço e otimiza a área disponível para armazenagem devido à verticalização que o método permite. Além disso, o formato de armazenagem também evita perdas de material por compactação e empedramento, já que os bags não são empilhados uns sobre os outros diretamente. E, por fim, o método permite o respeito da estratégia FIFO (First In, First Out) de expedição.
Com isso, a equipe do projeto analisou também as frequências de recebimento e de expedição, bem como as quantidades médias e os picos. Junto com a estratégia definida com o cliente a respeito da cobertura de estoque desejada, as áreas de armazenagem foram dimensionadas de modo a atender as necessidades futuras da planta produtiva.
Resultados
A principal entrega da equipe foi um pacote robusto de sugestões (com opções alternativas em alguns pontos) com todos os dimensionamentos e “linha do tempo”, onde é possível verificar em qual momento os investimentos nas adequações precisam ser realizados para que a estrutura comporte o crescimento esperado e ao mesmo tempo permita atingir o melhor equilíbrio entre performance operacional e custos.
Agora, se você também quer saber como uma consultoria especializada no assunto pode auxiliar a sua organização na reestruturação do fluxo logístico, entre em contato com a gente e confira nossos outros cases de sucesso!