Desafio
Com sede no Rio de Janeiro, essa empresa atua na operacionalização e no controle dos processos de Recebimento, Armazenagem, Processamento, Distribuição e Expedição nos Centros de Distribuição dos clientes. Preocupada em atender seus clientes de forma personalizada e garantindo a qualidade de seus serviços, aposta no know-how de seus colaboradores.
Durante a realização do Projeto “Estudo de Tempos e Métodos (ETM)” focado no diagnóstico do Macro Processo de Desembalagem, foram identificadas diversas oportunidades de melhorias relacionadas à falta de padrão e de organização na execução das operações, ao abastecimento de seus insumos e ao planejamento e controle das operações. Essas oportunidades foram traduzidas em planos de ação, visando prioritariamente o aumento de produtividade.
Solução
Diante das oportunidades identificadas, a Nortegubisian viu a chance de utilizar sua expertise nos conceitos de Trabalho Padronizado e de Planejamento e Controle da Produção para executar os planos de ação.
Inicialmente foi realizada a análise dos registros dos tempos padrão, provenientes do projeto anterior, o ETM. Neste momento, foi estudado o comportamento de cada elemento das três operações do processo estudado: Etiquetagem, Encabidamento e Pinagem.
O grande desafio dessa etapa foi criar padrões de trabalho que abrangessem os 6 mil tipos de itens processados anualmente.
A solução foi a classificação das peças em famílias, baseando-se nos tempos de cada elemento e em atributos, identificados durante a análise, que influenciam na produtividade das operações. A Figura 1 mostra uma análise realizada para a operação de etiquetagem, em que foi identificada a influência de um atributo com três níveis.
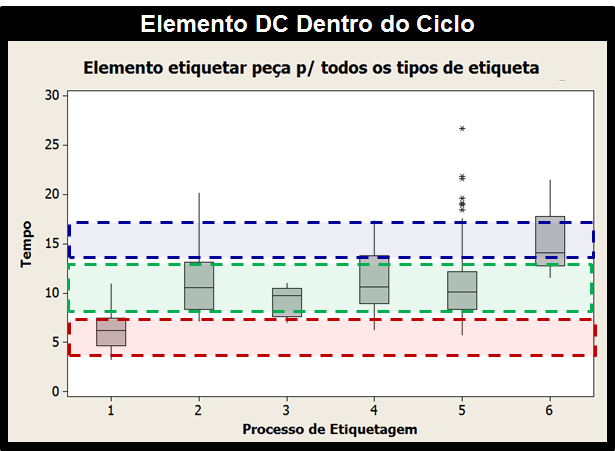
Os atributos identificados possibilitaram a criação de 13 famílias de processamento, contemplando as três operações e todo o mix de produtos.
Adicionalmente, visando balancear as operações nas diferentes famílias e diminuir o tempo de ciclo, foram criadas equipes de processamento com diferentes configurações de processamento.
Finalmente, de modo a esclarecer todas as funções para o novo modelo e todas as responsabilidades em cada nível do trabalho, foram criadas três categorias de instrução de trabalho: operacional, configuração e planejamento e controle da operação.
O primeiro nível de instrução é destinado ao PCP, e estabelece regras para a classificação dos pedidos nas famílias criadas. Já no segundo nível, a instrução é destinada à liderança das equipes, utilizada para definir a configuração da equipe, sua produtividade padrão e o layout da mesa, como pode ser visto na Figura 2. Por fim, foram criadas instruções de nível operacional, estabelecendo os movimentos padrões para cada operação.
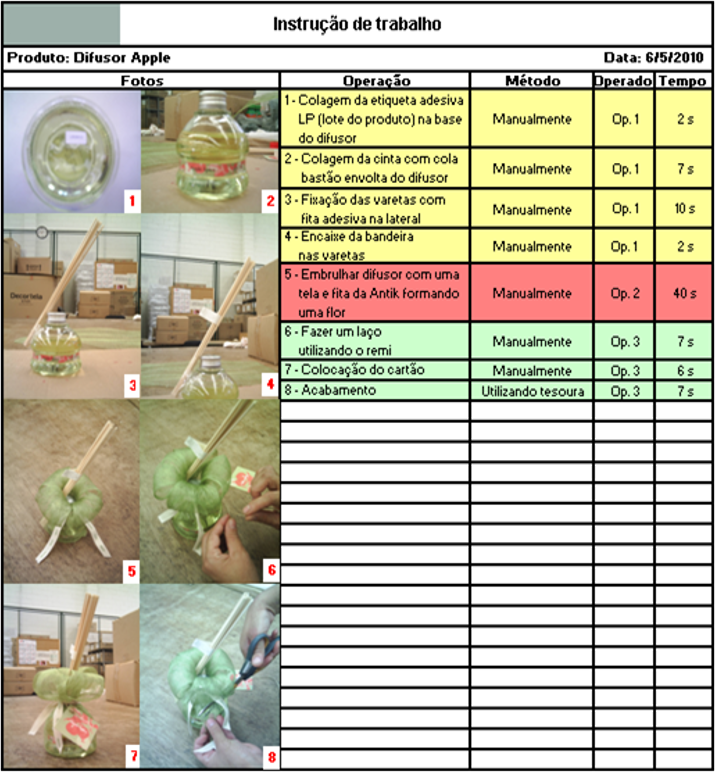
Em um segundo momento, foi desenvolvido e incorporado ao sistema de informação da empresa, um novo processo automatizado, com as seguintes funções:
- Divisão dos pedidos em ordens de processamento;
- Classificação dos pedidos nas famílias de processamento;
- Cálculo dos tempos planejados por ordem;
- Alocação das ordens por equipe de trabalho
- Sequenciamento das ordens por equipe;
- Geração da informação da necessidade de insumos (tipo e quantidade), garantindo maior disponibilidade dos processos.
Com o aumento da velocidade do processo devido ao novo modelo de operação, foi necessário revisar as atividades atribuídas à função de abastecedor. A distribuição do trabalho foi reformulada, sendo a função de abastecimento separada em movimentação e abastecimento, estabelecendo o número de colaboradores necessário, de maneira a garantir a disponibilidade do processo e otimizar a sua produtividade. Para registrar o novo processo, foram elaboradas instruções de trabalho para as operações de movimentação e abastecimento, informando para cada família, os pontos de abastecimento dos insumos utilizados.
Finalmente, na última fase do projeto, foi desenvolvido um modelo de dimensionamento de mão de obra que atendesse à demanda de processamento. O desafio deste modelo é devido à baixa previsibilidade dos processos, causada pela falta de padrão, e à alta sazonalidade da demanda. Essa dificuldade causava um superdimensionamento do efetivo necessário, resultando em uma redução da produtividade.
Para obter um maior aproveitamento dos recursos humanos, o modelo de dimensionamento fornecia um planejamento em médio prazo, capaz de auxiliar na determinação da capacidade, além do número de colaboradores necessários para atender a demanda de processamento.
O modelo considera a demanda projetada por tipo de família e os tempos de processamento, possibilitando maior precisão no cálculo do número operadores necessários, e melhorando a produtividade global da operação.
Resultados
O resultado foi expressivo: aumento de produtividade em torno de 30% nas operações de Desembalagem e Pinagem, e uma melhor gestão de desempenho das operações, fornecendo informação para melhorias posteriores.
Além disso, execução dos planos de ação trouxe os seguintes benefícios à empresa:
- Manutenção do ritmo de processamento;
- Especialização do trabalho (um operador faz uma operação);
- Aumento da produtividade das operações de pinagem, encabidamento e etiquetagem;
- Melhoria da previsibilidade dos processos;
- Balanceamento das operações, reduzindo erros de processamento e estoques intermediários;
- Aumento da disponibilidade dos processos, fazendo com que o tempo disponível seja gasto processando e não esperando;
- Aumento da precisão do dimensionamento da mão de obra necessária, reduzindo custos;
- Embasamento numérico para direcionar novas ações de melhoria de forma contínua.