Em um ambiente de negócios cada vez mais competitivo, eliminar desperdícios é essencial para garantir operações mais eficientes e elevar a produtividade. Empresas que buscam otimizar seus processos e maximizar o valor para os clientes precisam adotar práticas que reduzam atividades desnecessárias e ineficazes.
No contexto do Lean Manufacturing, os desperdícios são classificados em oito categorias, conhecidos como os “8 Desperdícios do Lean”. Esses desperdícios representam qualquer atividade que consuma recursos, tempo ou esforço, mas que não agrega valor direto ao produto ou serviço final, impactando negativamente no desempenho e nos resultados da empresa.
E de que forma podemos reconhecer e eliminar esses desperdícios na rotina das empresas? Nesse artigo, abordaremos cada um deles e forneceremos soluções práticas para sua mitigação.
Quais são os 8 Desperdícios do Lean?
- Produção Excessiva.
- Espera.
- Transporte.
- Processamento Excedente.
- Estoque Excessivo.
- Movimentação Desnecessária.
- Defeitos.
- Talento Desperdiçado.
A seguir, exploramos cada um desses desperdícios e como eliminá-los:
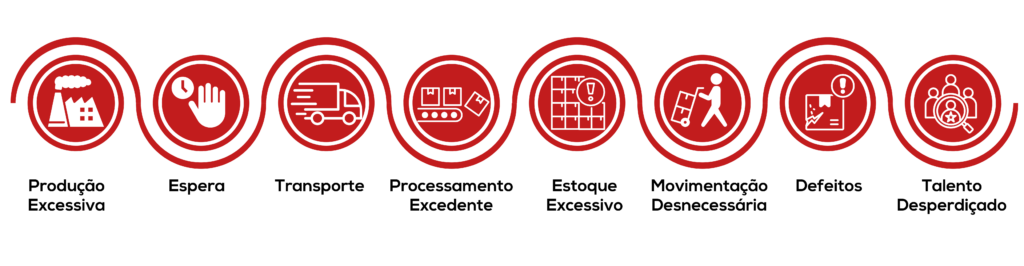
1. Superprodução
A produção excessiva ocorre quando se fabrica mais do que o necessário, antes da demanda real. Isso resulta em estoques excessivos, ocupa espaço e pode levar à obsolescência de produtos. Além disso, impacta negativamente a eficiência do fluxo de trabalho e aumenta custos operacionais sem necessidade.
Como eliminar?
- Implementar produção puxada (Just in Time): produza apenas o necessário, reduzindo estoques desnecessários.
- Utilizar sistemas de previsão de demanda mais precisos: adote ferramentas de análise de dados para prever demandas com maior precisão.
- Estabelecer lotes menores e flexíveis de produção: reduza a quantidade produzida por vez para evitar excessos.
2. Espera
O desperdício de espera ocorre quando os processos ficam paralisados devido à falta de materiais, informações ou recursos necessários para a execução. Isso pode acontecer por problemas na logística interna, falhas na comunicação ou processos com baixa eficiência.
Como eliminar?
- Aplicar técnicas de balanceamento de linha: distribua tarefas de forma equilibrada para evitar gargalos.
- Reduzir tempos de setup: automatize e padronize processos para diminuir o tempo de preparação de máquinas.
- Estabelecer fluxos contínuos para evitar gargalos: identifique e elimine pontos de ineficiência no fluxo de trabalho.
3. Transporte
O transporte desnecessário de materiais dentro da empresa não agrega valor e pode resultar em danos aos produtos, aumentando os custos operacionais. Movimentações excessivas dentro da linha de produção indicam um layout mal planejado e processos ineficientes.
Como eliminar?
- Melhorar o layout da fábrica para minimizar deslocamentos: reorganize o espaço de trabalho para reduzir movimentações excessivas.
- Implementar rotas eficientes de transporte interno: planeje trajetos para reduzir distâncias percorridas.
- Utilizar ferramentas como o mapeamento de fluxo de valor: identifique e elimine processos de transporte desnecessários.
4. Superprocessamento
Excesso de processamento ocorre quando se realiza mais trabalho do que o necessário para atender à necessidade do cliente, como inspeções excessivas ou funções desnecessárias no produto. Isso gera desperdício de tempo e recursos sem agregar valor real.
Como eliminar?
- Padronizar processos: defina um fluxo de trabalho eficiente para evitar etapas desnecessárias.
- Eliminar etapas desnecessárias: analise e remova processos que não agregam valor ao cliente.
- Utilizar tecnologias que simplifiquem a operação: implemente sistemas automatizados para reduzir esforço manual.
5. Estoque Excessivo
O excesso de estoque ocupa espaço, aumenta custos de armazenagem e pode levar a perdas por obsolescência. Além disso, estoques elevados podem mascarar problemas como falhas no planejamento de produção e atrasos na cadeia de suprimentos.
Como eliminar?
- Aplicar metodologias como Kanban para controle de estoque: utilize cartões visuais para gerenciar níveis de estoque.
- Trabalhar com fornecedores para entregas Just in Time: estabeleça parcerias para recebimento de materiais conforme necessário.
- Reduzir a produção de itens não necessários: produza somente conforme a demanda real para evitar acúmulos.
6. Movimentação Desnecessária
Movimentos excessivos dos operadores dentro do ambiente de trabalho reduzem a produtividade e podem causar fadiga desnecessária. Isso pode ser resultado de um layout mal estruturado, falta de organização ou uso inadequado de ferramentas e equipamentos.
Como eliminar?
- Ergonomizar postos de trabalho: ajuste bancadas, ferramentas e equipamentos para facilitar o trabalho.
- Melhorar o layout das estações de trabalho: posicione materiais e equipamentos de forma acessível.
- Reduzir a necessidade de movimentos repetitivos: automatize tarefas sempre que possível.
7. Defeitos
Produzir itens defeituosos resulta em retrabalho, desperdício de matéria-prima e insatisfação do cliente. Produtos com falhas impactam a credibilidade da empresa e aumentam os custos de operação.
Como eliminar?
- Implementar programas de qualidade como Six Sigma: utilize metodologias para reduzir variações nos processos.
- Utilizar métodos de análise de causa raiz, como 5 Porquês: descubra e elimine a origem dos problemas.
- Criar uma cultura de melhoria contínua: incentive os colaboradores a identificar e corrigir falhas rapidamente.
8. Talento Desperdiçado
Não utilizar plenamente as habilidades e ideias dos colaboradores é um dos maiores desperdícios dentro de uma empresa. Muitas vezes, funcionários têm potencial para contribuir com melhorias, mas não encontram espaço para isso.
Como eliminar?
- Estimular a participação dos funcionários em processos de melhoria: crie canais para sugestões e envolva a equipe nas decisões.
- Oferecer treinamentos para desenvolvimento de habilidades: invista na capacitação contínua dos colaboradores.
- Criar um ambiente de trabalho motivador e colaborativo: valorize talentos e promova uma cultura de inovação.
Benefícios da Eliminação dos 8 Desperdícios do Lean
Agora que você já conhece os desperdícios Lean, descubra os benefícios de eliminá-los.
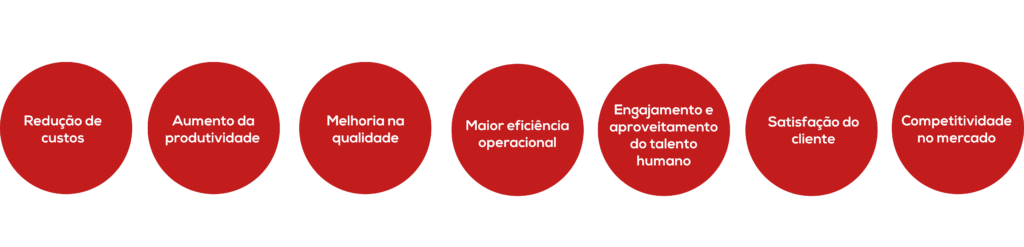
- Redução de custos – Menos desperdício de matéria-prima, redução de estoques excessivos e menor necessidade de retrabalho. Processos mais eficientes diminuem custos operacionais e aumentam a margem de lucro.
- Aumento da produtividade – Com menos esperas, movimentações desnecessárias e transportes ineficientes, os processos fluem melhor, reduzindo o tempo de execução das atividades e aumentando a produção sem demandar mais recursos.
- Melhoria na qualidade – A eliminação de defeitos e do processamento excedente evita falhas, garantindo produtos e serviços mais confiáveis, reduzindo reclamações e retrabalho, além de fortalecer a credibilidade da empresa.
- Maior eficiência operacional – Ao otimizar fluxos de trabalho e eliminar gargalos, a empresa alcança processos mais ágeis e organizados, garantindo entregas dentro do prazo e com menos desperdício de recursos.
- Engajamento e aproveitamento do talento humano – Colaboradores que participam da melhoria contínua se sentem mais valorizados e motivados. A empresa aproveita melhor as habilidades dos colaboradores, incentivando a inovação e a busca por soluções mais eficientes.
- Satisfação do cliente – Produtos e serviços entregues no prazo, com maior qualidade e custo reduzido, geram mais valor para o cliente, melhorando a experiência e aumentando a fidelização.
- Competitividade no mercado – Empresas que operam de forma enxuta e eficiente conseguem se destacar, oferecer preços mais competitivos e crescer de forma sustentável, conquistando vantagem frente à concorrência.
Eliminar os 8 desperdícios do Lean é essencial para garantir eficiência, redução de custos e melhoria na qualidade dos produtos e serviços. Empresas que adotam essas práticas conseguem otimizar processos e aumentar sua competitividade no mercado.
A implementação dessas mudanças exige um compromisso com a melhoria contínua e uma cultura organizacional voltada para a excelência operacional.
É importante lembrar que pequenas ações podem gerar grandes impactos e transformar a maneira como sua empresa opera. Além de ganhos financeiros, a redução de desperdícios melhora o ambiente de trabalho, promovendo maior engajamento dos colaboradores e aumentando a satisfação dos clientes.
Se sua empresa busca melhores resultados, investir em Lean pode ser um caminho certeiro para alcançar maior produtividade, reduzir custos e entregar mais valor ao cliente.
Na Nortegubisian, ajudamos empresas a implementar essas soluções por meio de treinamentos e consultorias especializadas, focadas na sua demanda, garantindo que sua equipe esteja preparada para identificar e eliminar os desperdícios de maneira eficaz.
Quer saber mais sobre como implementar o Lean na sua empresa? Entre em contato conosco e conheça nossos cursos e consultoria especializada. Nos acompanhe também no Linkedin, Facebook e Instagram para mais conteúdos sobre melhoria contínua!
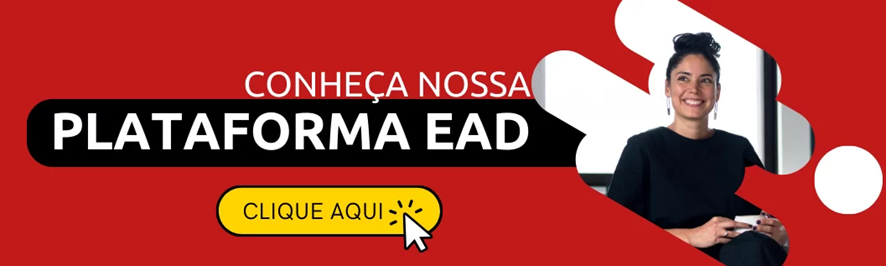