Desafio
Considerada uma das maiores empresas do mercado de embalagens em cartão, papel e plástico flexível, esta importante indústria possui parceria de longa data com a Nortegubisian. Durante o planejamento estratégico conduzido pela Nortegubisian, as estratégias para o ano de 2022 foram desdobradas em diversos planos A3, sendo um deles relacionado a implementação da cultura Lean nos processos operacionais do centro de distribuição.
O nosso desafio foi de assumir o papel de mentor do plano A3 criado, auxiliando no planejamento e execução das ações visando a otimização das operações.
Confira como esse trabalho foi desenvolvido!
Desenvolvimento do Projeto
No processo de planejamento e desdobramento das estratégias do Grupo para o ano de 2022, foi identificado que a iniciativa Lean nas operações do Centro de Distribuição seria essencial para atingimento de metas definidas na matriz X. O plano A3 desenvolvido tinha como principais objetivos atuar em oportunidades de melhorias visando otimização dos processos e redução de erros nas atividades. Por ser um plano com ampla atuação na operação do CD, as ações foram divididas em 2 blocos: suporte na execução e mentoria dos planos.
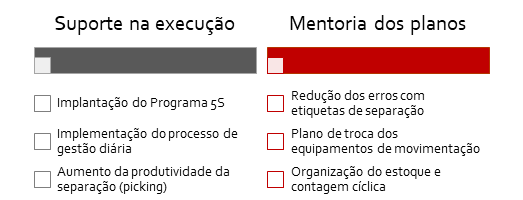
1. Implantação do Programa 5S
A ferramenta Lean de 5S é uma filosofia corporativa que visa aperfeiçoar o comportamento das pessoas através da mudança de hábitos e atitudes de forma a tornar o ambiente de trabalho agradável, seguro e produtivo. Com esse objetivo a implantação do programa 5S foi organizada através de um plano A3, contendo todas as fases do roadmap, responsáveis e prazos para realização das ações.
a) Fase 1 – Preparação
A fase de preparação envolveu todo o registro da condição atual do local de trabalho, planejamento do Dia D e treinamento (teórico + prático) para 100% dos colaboradores da operação.
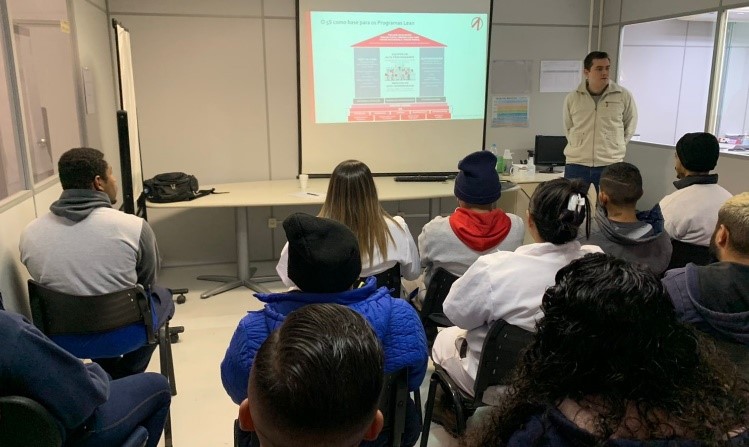
b) Fase 2 – Dia D
A segunda fase do roadmap foi iniciada com a realização do Dia D com a participação da gerência, coordenação, lideranças e operação, sendo o marco de implantação do programa no centro de distribuição. Durante a realização do Dia D, todas as oportunidades de melhorias que não foram possíveis de serem aplicadas foram registradas e transformadas em planos de ação.
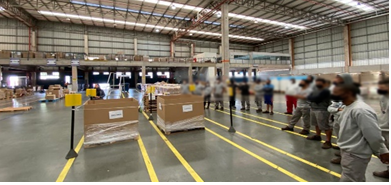
c) Fase 3 – Sustentação
A última etapa da implantação do programa foi iniciada com a construção de auditoria para avaliar a efetividade dos planos de ação e a manutenção dos cinco sensos. Foi definida a periodicidade mensal para as auditorias, sendo utilizado formulários digitais (Figura 3) para auxiliar no processo de avaliação e registro.
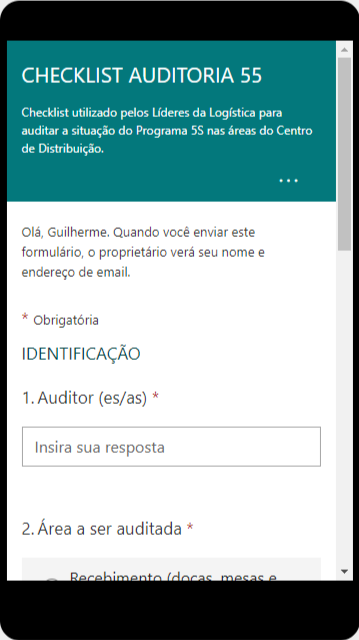
2. Implementação do processo de Gestão Diária
A implementação da gestão diária no CD teve como objetivo agilizar a identificação e eliminação dos problemas nas operações de recebimento e expedição, visto que é um sistema de acompanhamento que permite verificar a fluidez do que está sendo feito e se o desempenho está normal ou se apresenta algum tipo de desvio. A implementação foi realizada com base nos 4 elementos que compõe a gestão diária e pode ser resumida nas etapas da Figura 4.
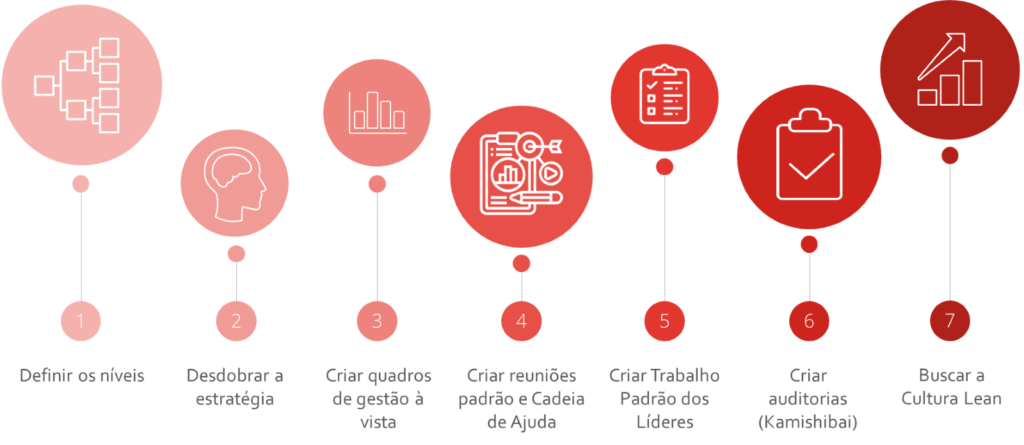
A definição dos níveis da gestão e o desdobramento da estratégia foram realizados durante a frente de trabalho responsável pela estratégia do grupo. Com isso, foram definidos os indicadores importantes para a área atingir seus objetivos e criados os quadros de gestão à vista para os níveis tático e operacional. Para cada nível, as reuniões foram criadas junto com as regras de horários, participantes necessários, temas a serem tratados e a cadeia de ajuda.
Visando o direcionamento à gestão visual, garantia de análise adequada dos quadros e o estabelecimento de uma cadência para a liderança, criou-se o trabalho padrão dos líderes e as auditorias Kamishibai.
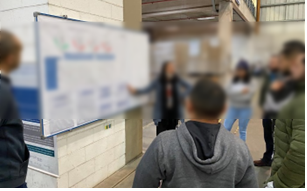
3. Aumento da produtividade do processo de separação (picking)
A separação é considerada um dos processos mais críticos dentro de um centro de distribuição, pois tem relação direta com a satisfação dos clientes do grupo. Com o intuito de melhorar a produtividade da separação elaborou-se o Estudo de Tempos e Métodos para determinar o tempo padrão e ciclo efetivo da atividade, além de identificar oportunidades de melhoria que possam impactar no processo, e o Diagrama de Espaguete para mapear a movimentação dos colaboradores durante a operação.
Neste contexto, foram apresentadas diversas oportunidades de melhoria para o processo: revisão da estratégia de alocação dos produtos no picking, dimensionamento do picking, padronização do trabalho, troca dos coletores, revisão dos perfis dos colaboradores no sistema dos coletores, troca dos equipamentos de movimentação.
A proposta da nova estratégia de alocação com base na curva PQR, ou seja, de acordo com o giro de cada item, proporcionou uma redução de 45% no deslocamento dos separadores gerando maior agilidade para a realização do picking. Na Figura 6 é possível observar que com a nova alocação dos produtos, os colaboradores não precisam sempre deslocar-se por toda a linha de picking.
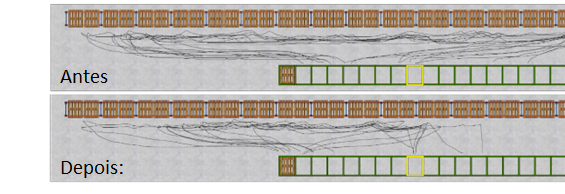
4. Mentoria: redução de erros com etiquetas de separação
Em paralelo ao trabalho desenvolvido, realizou-se a mentoria de um plano A3 focado na redução de erros com etiquetas de separação. A partir dos treinamentos sobre metodologias e ferramentas do Lean, a equipe de trabalho pode colocar em práticas os ensinamentos recebidos.
Como parte do plano, a análise de causa raiz foi fundamental para desenhar a situação alvo desejada e mapear as ações necessárias para atingir os resultados esperados. As ações foram concentradas em três pilares: instruções de trabalho, treinamentos iniciais teóricos/práticos e de auditorias do processo.
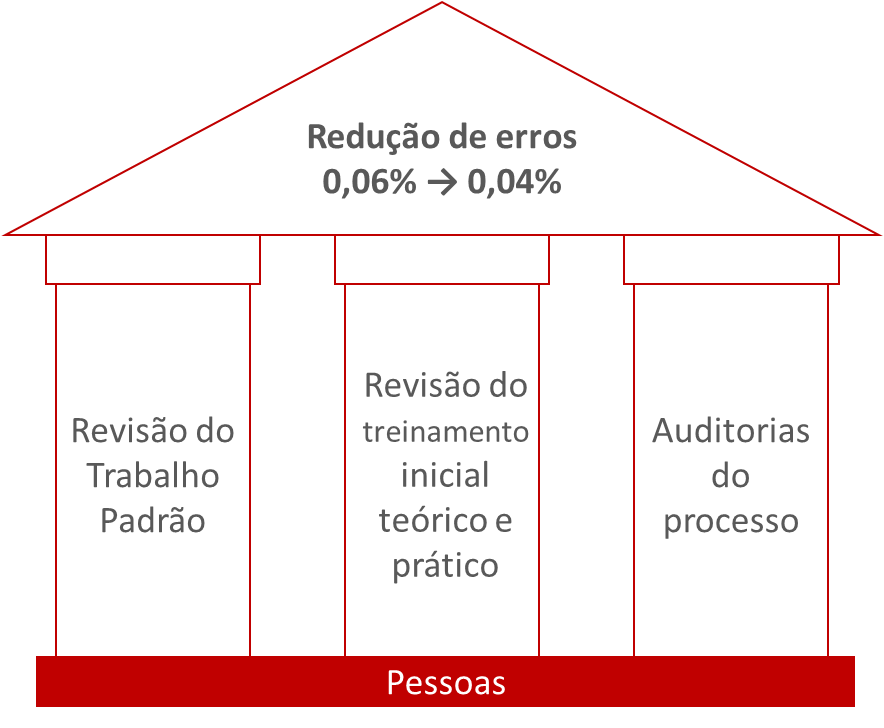
Figura 7 – Situação alvo do plano de redução de erros.
Resultados
Ainda nos primeiros meses do programa 5S foi possível observar as mudanças nas atitudes dos colaboradores que resultaram tanto na transformação do ambiente de trabalho quanto na evolução das notas obtidas nas auditorias (Figura 8). O 5S tem grande contribuição na busca por melhor produtividade, qualidade e economia dentro da empresa.
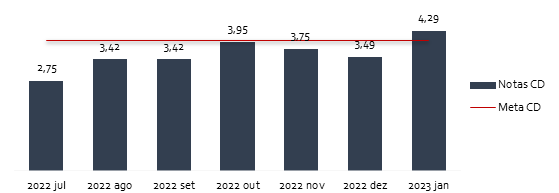
Com a implementação das ferramentas e ações descritas, foi observado aumento de 16% na produtividade da separação, saindo de uma média de 217 vol/h por colaborador para 251 vol/h, ultrapassando a meta de 230 vol/h estabelecida para o ano.
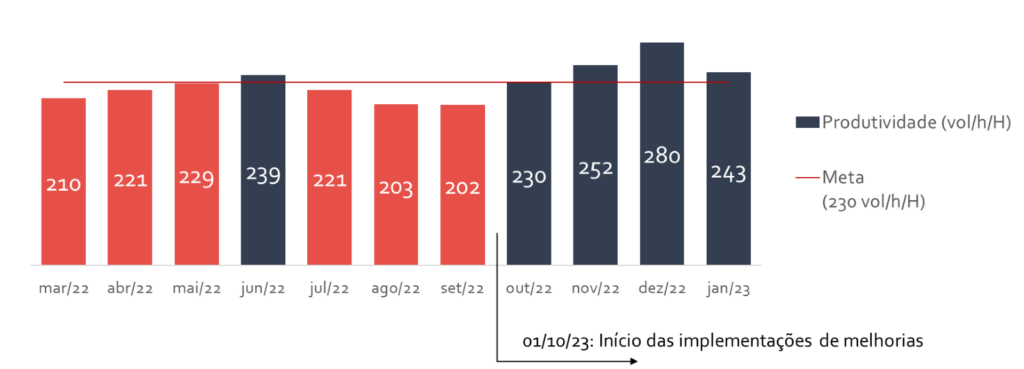
Atrelado ao aumento da produtividade, a qualidade da separação também foi melhorada através da redução dos erros com etiquetas de 0,10% em set/2022 para 0 erros em jan/23.
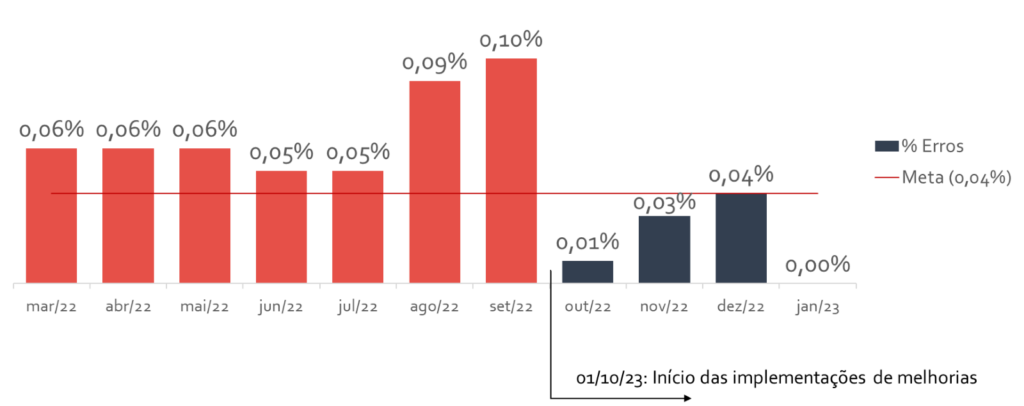
Tanto para produtividade quanto para os erros de separação, os bons resultados foram mantidos pelos 4 meses após o início das implementações das melhorias.
Todas as ações desenvolvidas durante o trabalho trouxeram também ganhos qualitativos na operação, percebido tanto pelos separadores quanto pela liderança do CD. Em dezembro, momento de alta demanda, foram reduzidas as necessidades horas extras, melhora na gestão dos colaboradores e atividades, criação da cultura de responsabilidade pela organização do CD, melhora na qualidade de vida dentro do CD.
Agora, se você ficou interessado em descobrir como uma consultoria especializada pode ajudar a alavancar seus resultados, entre em contato conosco!
Além disso, não se esqueça de acessar nossos outros cases de sucesso e nos acompanhar no Instagram, Facebook e LinkedIn.
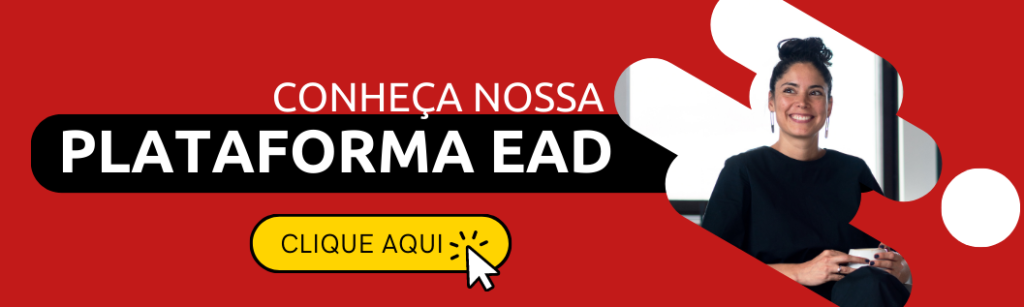