Contextualização
Presente no Brasil há mais de 20 anos, uma empresa metalúrgica consolidada e reconhecida no mercado nacional e internacional por produzir componentes para diferenciais, instigada em assegurar a excelência operacional de seus processos de usinagem, identificou a necessidade de implementar e desenvolver a cultura Lean em seu ambiente fabril.
Diante desta situação, a consultoria Nortegubisian foi selecionada para desenvolver o modelo padrão para a implementação da cultura e práticas Lean na empresa. O modelo foi desenvolvido na célula piloto de fabricação de semieixos, abrangendo desde a saída da forjaria até entrada na expedição.
Detentora de ampla expertise em projetos deste caráter, a Nortegubisian aplicou conceitos de Lean Manufacturing para mapear os processos, medir o desempenho destes e enxergar oportunidades de melhoria. Além disso, objetivou-se organizar o espaço de trabalho, padronizar e melhorar processos, elaborar procedimentos, instruções de trabalho e definir responsabilidades.
Com a finalidade de garantir sustentabilidade e aderência dos colaboradores à cultura implementada, criou-se um modelo de governança, a partir da implementação da gestão diária, para melhorar a solução de problemas e agir de forma assertiva no menor tempo possível.
Todas essas mudanças e adequações foram executadas em paralelo ao contínuo treinamento dos envolvidos, munidos de frequente acompanhamento e suporte da Nortegubisian para assegurar adesão e perenidade das boas práticas implementadas.
Desenvolvimento do projeto
O trabalho foi executado, essencialmente, em cinco planos de atividades:
- Mapear, medir e enxergar;
- Organizar, padronizar e melhorar;
- Procedimentar e responsabilizar;
- Criar gestão diária e pertencimento;
- Acompanhar e suportar.
O desenvolvimento de cada plano mencionado acima será abordado nos tópicos seguintes.
1. Mapear, medir e enxergar
Esta etapa inicial consistiu em identificar os processos, entender os papéis e responsabilidades dos colaboradores, conhecer a performance atual de cada processo e avaliar as dificuldades observadas. Para este plano, a aplicação de algumas ferramentas Lean foram fundamentais, destacando-se o fluxograma VSM, o Estudo de Tempos e Métodos (ETM) e o Diagrama de Yamazumi.
O fluxograma VSM é recomendado para estabelecer quais as etapas chave do processo e qual a quantidade de WIP entre estas etapas. Além disso, nos permite mapear as interfaces entre os processos, incluindo fornecedores e clientes, sejam eles internos ou externos. A Figura 1 apresenta o VSM da situação inicial mapeada.
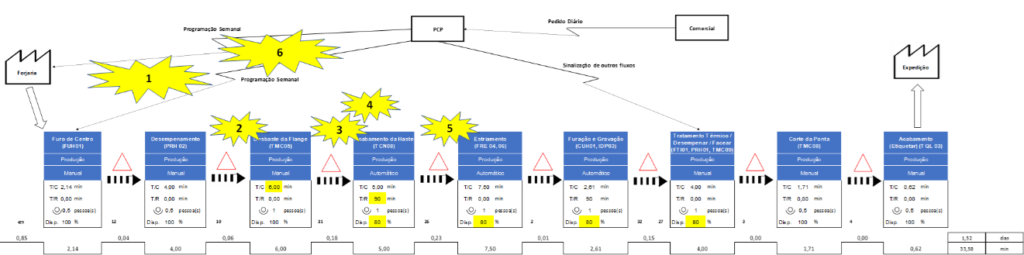
O ETM foi realizado para cada etapa presente no VSM. Conforme cada processo era mensurado, realizava-se uma análise crítica acerca de suas características gerais e pontuavam-se motivos que poderiam afetar a produtividade daquela posição de trabalho. Tais pontuações são essenciais para identificação de oportunidades de melhoria (Kaizens) e elaboração do VSM de situação futura.
Com os dados obtidos a partir do ETM, construiu-se o Diagrama de Yamazumi da condição inicial e checou-se sua assertividade quando comparado ao Takt Time (TT). Para construção do TT, considerou-se diferentes demandas mensais de peças em cada etapa. A Figura 2 apresenta o Diagrama de Yamazumi elaborado para a situação inicial.
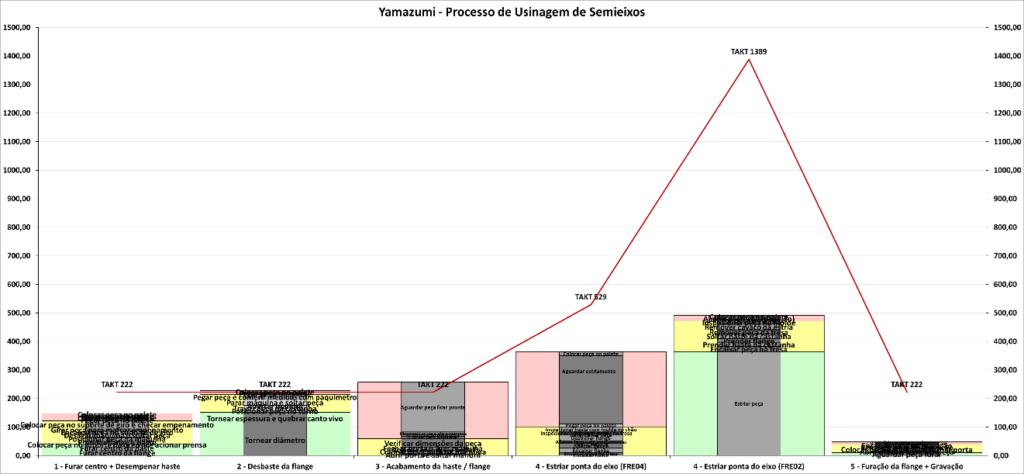
O Diagrama de Yamazumi nos permite enxergar quais operações dentro de um processo agregam valor ou não, além de fazer uma correspondência entre quais operações necessitamos reduzir tempo de ciclo a fim de atingirmos nossa demanda de produção. Através da etapa de mapeamento foram identificadas 11 macro oportunidades de melhoria.
2. Organizar, padronizar e melhorar
Os objetivos desta etapa são criar padrões de limpeza e ordenação do espaço de trabalho através de iniciativas 5S, melhorar a performance do processo por meio do desenvolvimento de melhorias (Kaizens) e ter maior controle, qualidade, produtividade e eficiência operacional, obtidas por meio da estruturação e execução de planos de ação para as oportunidades priorizadas.
Portanto, o passo inicial foi a elaboração de um plano de ação no formato A3 e estruturação do VSM de situação alvo com as devidas oportunidades de melhoria identificadas, conforme apresentado na Figura 3.
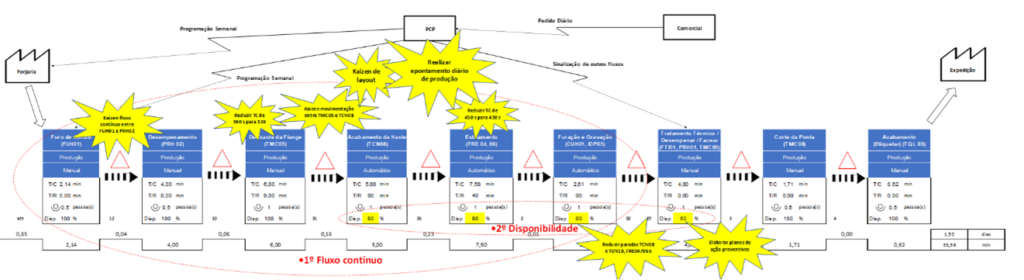
Os próximos passos desta etapa envolveram execução de Kaizens com focos em redução de tempos de ciclo e deslocamentos, aumento de produtividade, ergonomia e organização do espaço de trabalho (evento 5S) e sequenciamento de produção.
Também vale ressaltar outras duas frentes de trabalho que apresentaram resultados significativos: implementação de reunião semanal para análise de causa raiz relacionada a paradas não-programadas que impactaram a semana – responsável por redução de mais de 180 horas de paradas não-programadas obtidas através da execução de planos de ação dedicados – e elaboração de plano de manutenção autônoma, ferramenta inicial empregada em programas de Manutenção Produtiva Total (TPM).
3. Procedimentar e responsabilizar
Garantir que os processos ocorram da mesma maneira e com previsibilidade é parcela essencial de todo projeto de melhoria, pois mantém o conhecimento gerado pela empresa, reduz riscos e erros na realização de atividades, fornece clareza, controle e rastreabilidade às operações, além de melhorar a comunicação entre as áreas e prover conhecimento técnico.
Portanto, ao longo da execução dos trabalhos, foram criados procedimentos e instruções padrão de trabalho, com o intuito de capacitar os colaboradores envolvidos no projeto.
4. Criar gestão diária e pertencimento
A cultura da melhoria contínua deve ser exercitada diariamente por todos os membros do time, seja através da interpretação objetiva de indicadores, responsividade, proposição de ações corretivas e de melhoria e acompanhamento de compromissos para garantia da constância de resultados. Estas ações estimulam o senso de pertencimento das pessoas e são compiladas através de quadros de gestão à vista, logo, esta etapa é um pilar para a sustentabilidade das melhorias implementadas.
Os quadros de gestão à vista devem permitir que todos entendam, de forma clara e objetiva, a situação atual da área de interesse, ou seja, nos permite identificar se “estamos ganhando ou perdendo” e despertam gatilhos para solução ágil de problemas.
Dessa forma, em conjunto com a criação de reuniões padrão e cadeias de ajuda, foi possível sustentar o gerenciamento das melhorias implementadas. A Figura 4 apresenta o quadro de gestão à vista implementado em área central da célula de semieixos.
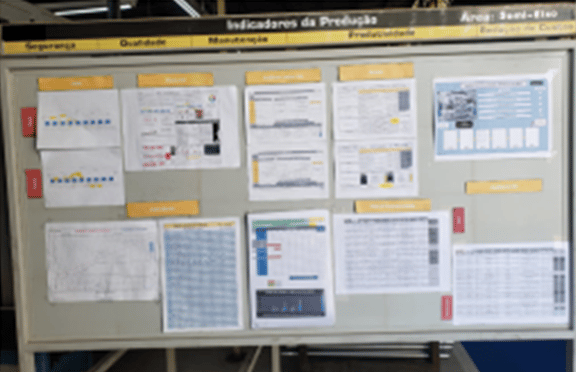
Além do quadro de gestão à vista, foram criados apontamentos de produção hora-a-hora, os quais confrontam a meta estabelecida e a produção realizada. Mais importante do que apontar a produção é identificar os motivos pelos quais a meta estabelecida não é atingida. Assim, fez-se uso dos Gráficos de Pareto para atuar sobre os problemas identificados, a fim de solucioná-los.
5. Acompanhar e suportar
Esta etapa teve por objetivos prover conhecimento aos envolvidos acerca da solução prática de problemas, despertar o espírito do “agir proativamente”, estimular o senso crítico, acompanhar as ações e corrigir desvios e, principalmente, manter vivo o ciclo virtuoso para a gestão e melhoria contínua.
Para isso, durante todo o projeto, os times foram acompanhados, incentivados e auditados pelos consultores do time Nortegubisian. A divulgação dos resultados à medida que eram alcançados foram responsáveis pelo crescente engajamento dos colaboradores à cultura Lean.
Resultados
Ao longo do trabalho foi fornecido o suporte para a continuidade da execução das atividades implementadas, treinamentos de Solução Prática de Problemas (SPP) e 5S, além de acompanhamento na execução dos planos de ação elaborados.
Em relação ao percentual de ferramentas Lean empregadas durante o período de quatro meses de projeto, obteve-se implementação de cerca de 60% delas, conforme apresentado na Figura 5.
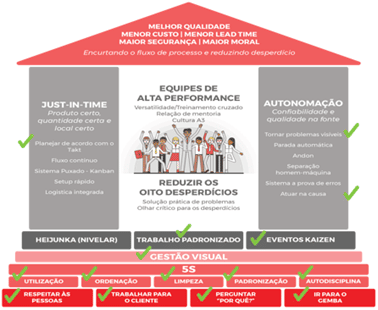
A produção de semieixos também apresentou resultado significativo, pois obteve-se durante o período de execução do projeto, a maior produção mensal dos últimos 6 anos, correspondente a 3.465 peças. Este resultado foi atingido graças à união de esforços entre Nortegubisian e cliente perante a implementação e desenvolvimento da cultura Lean em seu cotidiano.
Agora, se você ficou interessado em descobrir como uma consultoria especializada pode ajudar a alavancar seus resultados em conjunto à excelência organizacional, entre em contato conosco!
Além disso, não se esqueça de acessar nossos outros cases de sucesso e nos acompanhar no Instagram, Facebook e Linkedin.