O uso de ferramentas e metodologias de melhoria contínua é fundamental para otimizar os processos de uma empresa. Nesse sentido, a Manutenção Produtiva Total é uma das soluções que proporciona redução significativa nas perdas do fluxo produtivo, resultando em processos mais ágeis com custos mais baixos.
Se você ainda não conhece esse conceito, encontrou o artigo certo! Vamos explicar tudo sobre essa metodologia, a sua importância para o negócio e, ao final, traremos um exemplo real de como conseguimos uma redução de quase 50% no tempo de indisponibilidade dos equipamentos de uma empresa parceira. Confira!
Entendendo o conceito de Manutenção Produtiva Total
Vamos começar entendendo melhor o conceito, como ele surgiu e quais são os benefícios que ele proporciona para as empresas. Acompanhe:
O que é?
A Manutenção Produtiva Total, mais conhecida como MPT, é um processo sistêmico de gestão que visa a melhoria da eficiência global dos equipamentos. Para tal, seu objetivo primário é identificar as principais fontes de perdas que podem causar interrupção do fluxo produtivo e, assim, agir de maneira a reduzi-las ou eliminá-las.
Quando surgiu?
No período de crescimento pós-guerra e recuperação econômica as empresas enfrentavam o problema do grande índice de perdas e paradas da produção, que as impediam de acompanhar melhor a demanda do mercado. Na década de 1970, o japonês Seiichi Nakajima desenvolveu a MPT, que começou a ser utilizada nas empresas do país e logo se espalhou por todo o mundo.
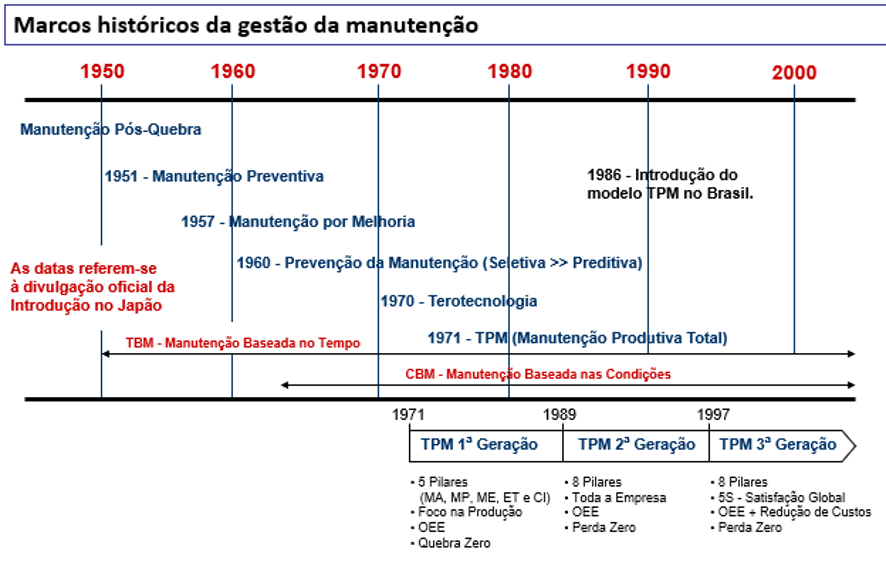
Quais são seus principais benefícios?
O benefício mais importante da ferramenta é a redução da indisponibilidade nos equipamentos da linha de produção. Em decorrência disso, diversas outras vantagens são obtidas, tais como a redução dos custos de manutenção, aumento da capacidade produtiva e redução do lead time.
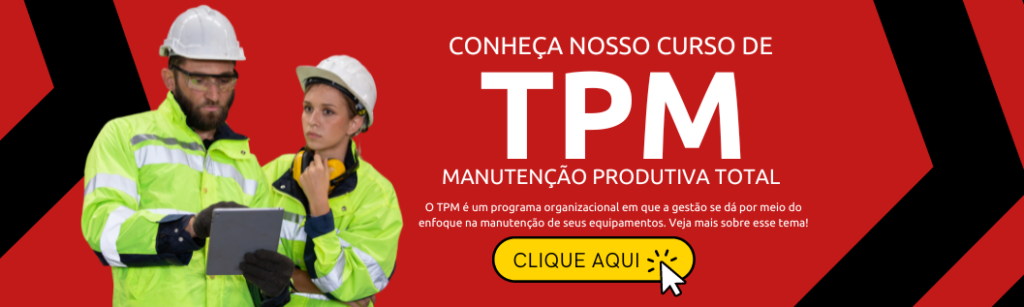
Os 8 pilares da MPT
A metodologia se baseia em 8 pilares para garantir a máxima eficiência do fluxo produtivo. Veja quais são eles.

1. Manutenção autônoma
Esse pilar visa aproximar os operadores dos equipamentos, capacitando-os sobre manutenções cotidianas que resultam na conservação prolongada de cada máquina. As ações vão desde a limpeza correta até pequenos ajustes periódicos.
2. Manutenção planejada
Nesse pilar, a preocupação é com os problemas decorrentes do uso do equipamento. Por isso, conta com duas ferramentas de manutenção: a preventiva e a preditiva. A primeira evita que a máquina pare ao gerenciar seus sobressalentes, já a segunda age na busca por anomalias que sinalizem futuras paradas e permitam que uma manutenção seja planejada com antecedência.
3. Manutenção da qualidade
Esse é o ponto que evita que produtos defeituosos cheguem ao final do processo. Para isso, podem ser utilizados diversos artifícios, tais como:
- dispositivos Poka-Yoke;
- manuais de procedimento operacional padrão — POP;
- controle estatístico do processo — CEP.
4. Melhorias específicas
As melhorias específicas são ações de entendimento e investigação do funcionamento de cada equipamento de forma a encontrar pontos de melhorias na produtividade, maximizando a eficiência global do equipamento atacando problemas mais complexos. Trata-se de uma etapa a ser aplicada mais à frente, para aprimorar os resultados obtidos após a estabilização das manutenções preventivas.
5. Controle inicial
O controle inicial visa realizar um controle que antecede o processo. Nele, sempre que há a necessidade de adquirir novos equipamentos, é feito um estudo para garantir a compra de modelos que sejam mais produtivos e fáceis de operar e manter.
6. Treinamento
O treinamento é um pilar fundamental para a manutenção da sustentabilidade da empresa no mercado. Ele prevê que todos os colaboradores devem ser frequentemente treinados e capacitados, não apenas na operação dos equipamentos, mas em tudo o que envolva os assuntos relacionados ao negócio.
7. Segurança e meio ambiente
A saúde e segurança dos colaboradores fazem parte da metodologia MPT. Por isso, a empresa deve manter um ambiente livre de riscos de acidentes e em conformidade com as boas práticas de preservação ambiental. Afinal, a saúde de todos não se limita ao que acontece dentro das dependências da organização.
8. Áreas administrativas
As áreas administrativas também podem ser aprimoradas. O uso do programa 5S é uma das alternativas para obter a redução de desperdícios nesses setores e impactar o resultado financeiro e operacional da empresa como um todo.
As 6 grandes perdas
Todos esses pilares foram criados para evitar o que a ferramenta chama de as 6 grandes perdas. São elas:
- quebras/falha;
- Trocas de ferramentas (setup);
- tempo ocioso (pequenas paradas);
- baixa velocidade;
- qualidade insatisfatória;
- perdas com startup.
As perdas 1 e 2 estão diretamente relacionadas ao índice de indisponibilidade do equipamento. A quebra ou erros na configuração geram paradas inesperadas que afetam o tempo disponível para uso. Já as perdas 3 e 4, dizem respeito à eficiência. As pequenas paradas ou a velocidade de produção abaixo da média esperada reduzem a capacidade produtiva do processo.
Por fim, as duas últimas perdas demonstram a qualidade do equipamento. Se um produto não foi fabricado em conformidade com os padrões exigidos, seja por ineficácia do equipamento ou pela falta de insumo, toda a entrega dos itens pode ser prejudicada.
Resultados reais da aplicação da MPT pela Nortegubisian
Todo esse trabalho pode ter gerado uma dúvida: será que todo esse esforço gera resultados que valham a pena? A resposta é sim!
A Nortegubisian tem experiência na implementação de ferramentas de melhoria de processos, entre elas a MPT. No case de sucesso que descrevemos neste post, focamos na estruturação da manutenção autônoma, que é o primeiro pilar da MPT. O trabalho começou com o mapeamento do macro processo produtivo da empresa e o treinamento das equipes de operadores. Em seguida, foram as 7 etapas da manutenção autônoma.
Como resultado, a empresa obteve uma redução do tempo de indisponibilidade em 48%, que representa um total de 55 horas a mais de máquinas em plena atividade. Além disso, houve uma redução de 23% nos custos com a manutenção dos equipamentos e um redirecionamento de 60 horas, antes ociosas, dos operadores para as ações de manutenção preventiva.
Com tantos resultados positivo, fica fácil perceber que a implementação do método de Manutenção Produtiva Total compensa todos os esforços necessários. Além das vantagens citadas, vale ressaltar que tratam-se de benefícios definitivos, cuja tendência é de serem cada vez mais aprimorados. Quem não quer isso para sua empresa, certo?
Se você gostou desse conceito e quer aprender mais, clique aqui e confira nosso curso EAD sobre Manutenção Produtiva Total e nos siga nas redes sociais (LinkedIn, Facebook e Instagram)!