O Total Productive Maintenance (TPM), traduzido para o português como Manutenção Produtiva Total, é um programa organizacional em que a gestão se dá por meio do enfoque na manutenção de seus equipamentos, com o objetivo de maximizar o rendimento produtivo através da integração da Manutenção com a Produção, além de ser uma das ferramentas do Lean.
A gestão por meio do TPM tem como princípio fundamental a máxima disponibilidade dos recursos fabris:
- “Zero” quebras;
- Sem pequenas paradas/Sem ajustes frequentes;
- “Zero” defeitos.
Para atingir tal patamar o TPM enfatiza atuações planejadas de caráter proativo e preditivo, ou seja, reparos realizados antes da falha, com base no tempo ou na condição, respectivamente. Portanto, tenta-se evitar ao máximo ações corretivas (reparo após falha), caracterizadas pelo alto custo de parada, baixa disponibilidade e baixo nível de planejamento.
Além disso, o trabalho desenvolvido durante a implantação de um programa TPM cria o senso de responsabilidade compartilhada pelo equipamento, encorajando uma maior participação dos operadores do chão de fábrica e não apenas da equipe de manutenção, diferentemente dos modelos tradicionais.
História
Logo após a Segunda Guerra Mundial, a indústria japonesa iniciou seu processo de reestruturação com forte apoio técnico e financeiro dos Estados Unidos. Nesta nova conjuntura econômica, os japoneses passaram a buscar métodos de eliminação de desperdícios e melhoria de processos para aumentar sua competitividade industrial através da elevação da qualidade e da produtividade.
Os empresários japoneses remanescentes do pós-guerra, apoiados por profissionais norte-americanos como Edward Deming e Joseph Juran, iniciaram uma forte mobilização nacional para a conscientização sobre a importância da qualidade como um fator de sobrevivência em meio a um novo cenário econômico que emergia no pós-guerra.
A busca de aprimoramento das atividades empresariais e a melhoria dos processos de industrialização estabeleceram o ponto de partida para a popularização de conceitos e técnicas relacionados à manutenção e a programas de qualidade e produtividade.
Neste contexto, surgiu o TPM (Total Productive Maintenance), ou MPT (Manutenção Produtiva Total). O termo foi utilizado pela primeira vez no final dos anos 60 pela empresa Nippon Denso, um dos fornecedores da Toyota.
Os resultados expressivos obtidos em relação ao aumento da disponibilidade para o uso de máquinas e equipamentos contribuíram para a rápida disseminação do TPM em todo o mundo e para organizações de diversos segmentos industriais.
Alguns estudiosos consideram o TPM como uma ferramenta de apoio ao programa Lean e associam a sua utilização ao princípio denominado “Máxima Disponibilidade”, que consiste em conseguir que as máquinas e equipamentos de uma instalação industrial estejam o máximo de tempo possível disponível para uso.
Etapas
A implantação do programa TPM esta estruturada com base em 8 pilares:
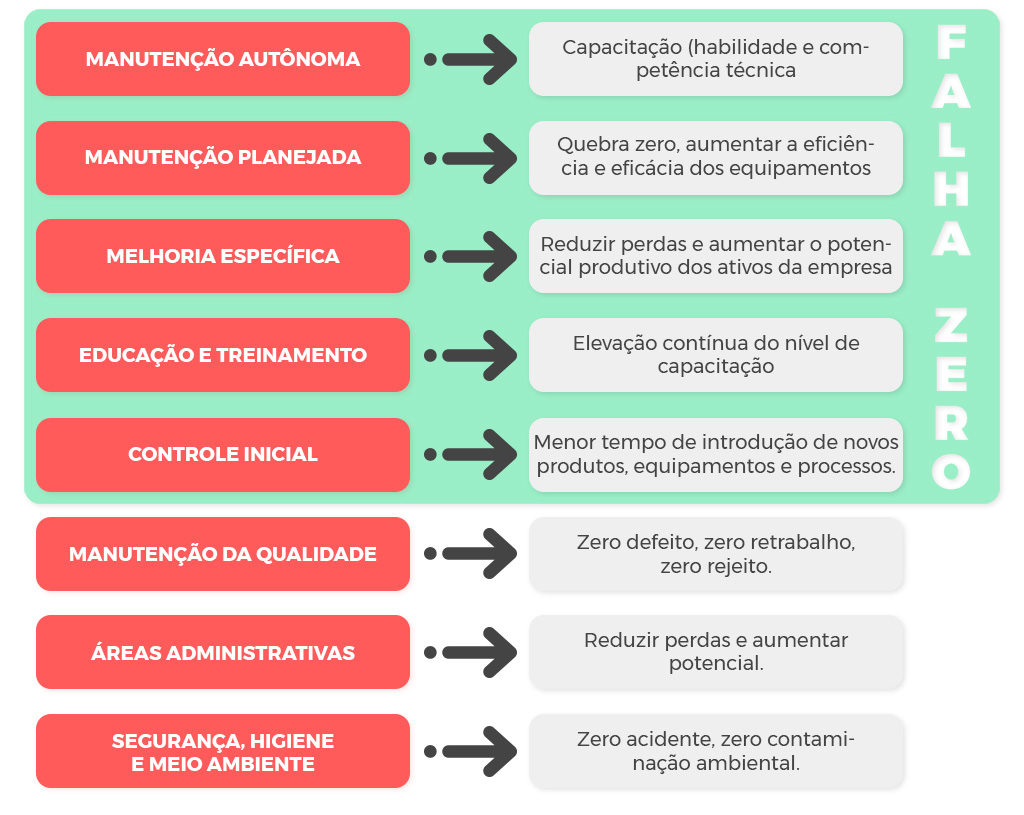
- Manutenção Autônoma: tem como objetivo criar um ambiente no qual os operadores do chão de fábrica da Produção se sintam responsáveis pelos equipamentos produtivos e tenham capacidade técnica para corrigir pequenos e médios problemas, perceber indícios de quebras futuras, executarem manutenções periódicas nos equipamentos (como lubrificação) de forma a extrair o melhor desempenho produtivo possível;
- Manutenção Planejada: o principal objetivo deste pilar é manter e melhorar as condições iniciais de um equipamento produtivo, a um custo mínimo, de forma a garantir maior tempo de funcionamento da linha de produção;
- Melhoria Específica: este pilar tem como objetivo aumentar a eficiência da produção. Para isso, o pilar muitas vezes age identificando, priorizando e atacando as maiores perdas, que podem estar localizadas tanto nas linhas produtivas, quanto em outros departamentos da fábrica;
- Educação e treinamento: o objetivo desse pilar é desenvolver e disseminar conhecimentos possibilitando que outros pilares tenham pessoas capacitadas para o desenvolvimento das atividades. Esse pilar também deve manter controle do nível de conhecimento das pessoas, sendo capaz de identificar as necessidades de treinamentos e realizá-los de forma eficiente;
- Controle inicial: tem como objetivo assegurar o bom desempenho da produção após inovações, tanto no caso de novos equipamentos, como no caso de mudança no produto produzido. Este pilar utiliza as informações de melhorias realizadas por outros pilares, de forma que novos projetos já contemplem as melhorias feitas nas linhas produtivas;
- Manutenção da qualidade (quebra zero): tem como objetivo diminuir ao mínimo o número de defeitos de qualidade. Para isso, este pilar monitora a quantidade de reclamações dos consumidores, e a quantidade de retrabalho nos insumos produzidos. Este pilar faz periodicamente medições na produção aferindo-se as especificações dos produtos, através das variações, se estão conformes. Com os resultados dessas medições e as informações da capacidade e estabilidade, pode-se elaborar um plano de prevenção ou correção dos problemas envolvidos com qualidade;
- Áreas Administrativas: o pilar office tem como objetivo eliminar as perdas administrativas. Essas perdas estão em muitos casos ligadas à qualidade e precisão das informações. Eles podem ser erros em informações tais como: estoque de um determinado item, fazendo-se que a linha de produção pare, diminuindo a eficiência do processo de fabricação. Empresas que possuem esse pilar bem desenvolvido geralmente estão com a metodologia TPM muito bem fundamentada e desenvolvida, pois esse pilar não costuma ser o foco inicial na implementação do TPM;
- Segurança, higiene e meio ambiente (zero acidente): esse pilar busca aumentar a segurança dos funcionários da empresa e diminuir o impacto no meio ambiente causado pelo processo produtivo. Exemplos de trabalhos desse pilar são: redução de poluentes emitidos e modificações em equipamentos que trazem riscos aos funcionários.
Benefícios
Um programa TPM bem implantado irá proporcionar a completa eliminação de:
- Quebra de equipamentos;
- Problemas de qualidade;
- Perdas de produtividade relacionadas ao uso dos equipamentos;
- Outras perdas de manufatura (desperdícios).
Os objetivos da implantação do TPM são:
- Buscar a máxima eficiência do sistema de produção;
- Eliminar todas as perdas
- Aumentar a vida útil dos equipamentos;
- Abranger todos os departamentos da empresa;
- Envolver todos os funcionários;
- Buscar a meta de “Quebra Zero”.
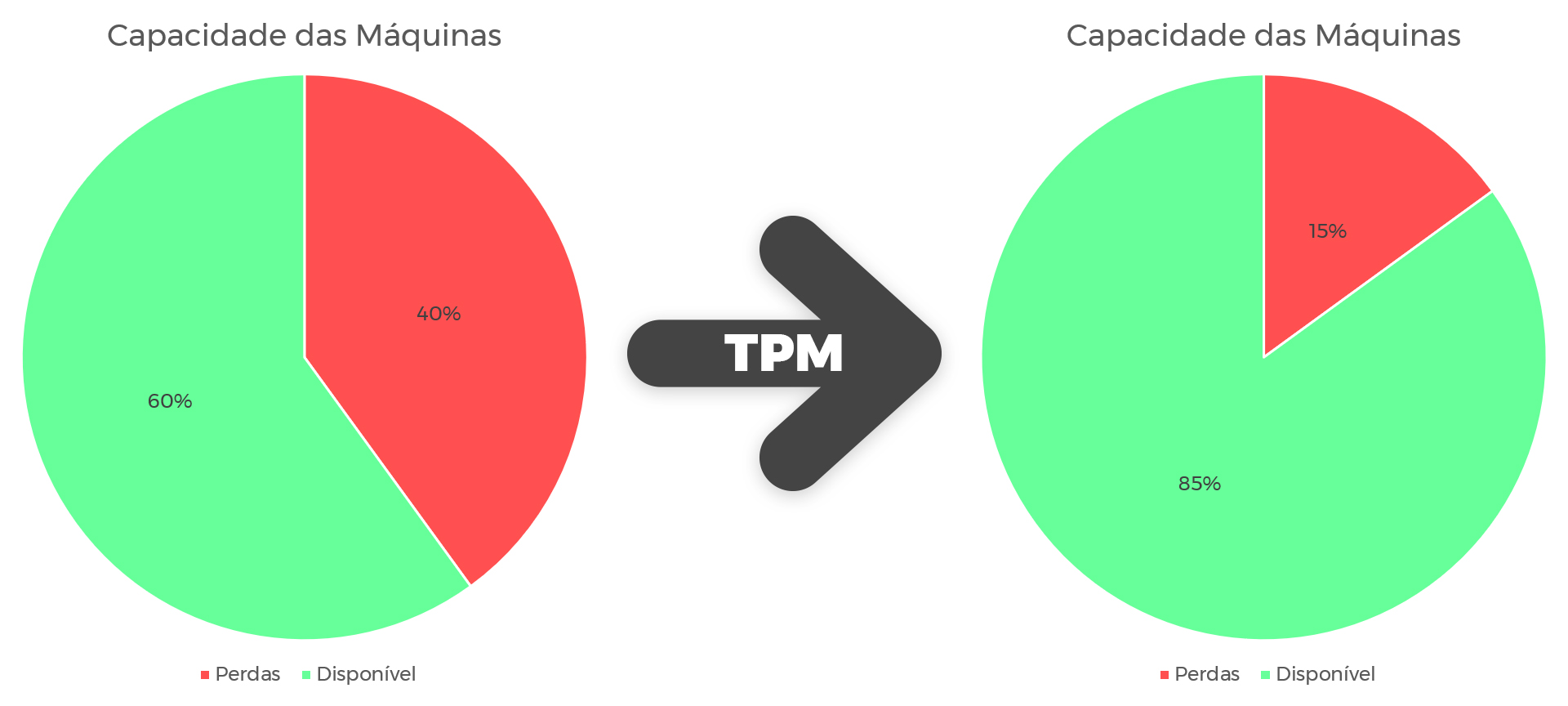
Aplicação
O nível de maturidade da implantação de um programa TPM em uma empresa pode ser obtido por meio do levantamento do indicador de desempenho OEE (Overall Equipment Effectiveness), métrica relacionada à eficiência global do equipamento. O OEE é um indicador que merece atenção especial. Sua análise permite orientar e priorizar ações focadas na solução de problemas específicos e gerar resultados com maior velocidade.
O OEE é o resultado da multiplicação de três perspectivas que caracterizam esta eficiência:
- Disponibilidade: quanto do tempo operacional disponível o equipamento esteve operando sem problemas;
- Performance: o desempenho do equipamento durante sua operação em relação a velocidade padrão (standard)
- Qualidade: aquantidade de unidades conformes produzidas durante a operação do equipamento.
A tabela a seguir ilustra a fórmula de cálculo do indicador:
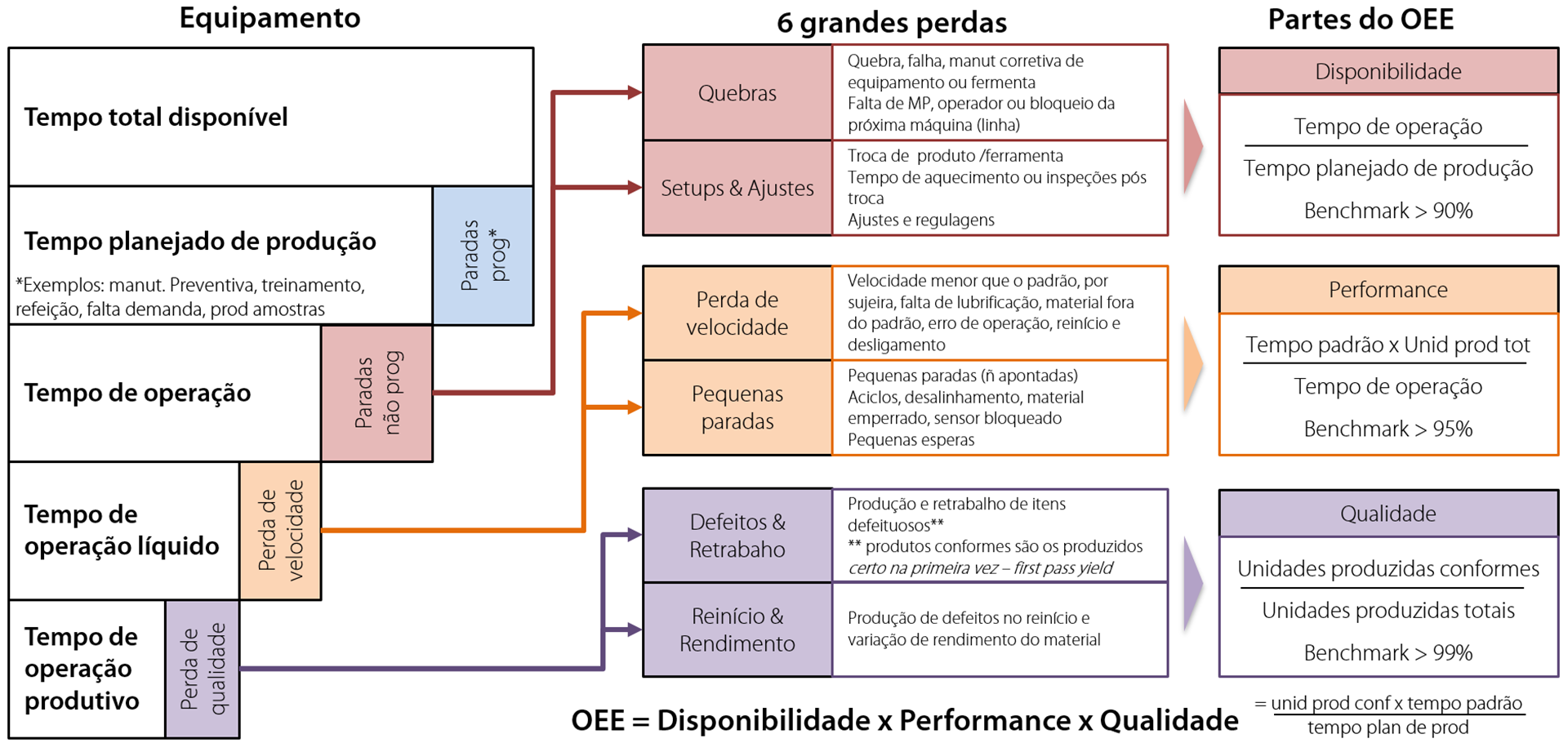
Exemplo de Cálculo
Para manufaturar um lote de 100 unidades de um determinado produto X, ela gasta 12 horas. De acordo com o roteiro de fabricação, o tempo de manufatura do produto X é de 6min/uni. Foram produzidas 4 peças defeituosas no período. Foram gastos 30 minutos em manutenção corretiva e durante 20 minutos a máquina em questão ficou parada esperando por material.
- Disponibilidade = 1 – [(20min+30min) / 8,5h x 2 x 60min)] = 0,95 (95%)
- Performance = [ 6min x 100uni ] / [12hx60min] = 0,83 (83%)
- Qualidade = 1 – [(4/100)] = 0,96 (96%)
OEE = 0,95 x 0,83 x 0,96 = 0,757 (75,7%)
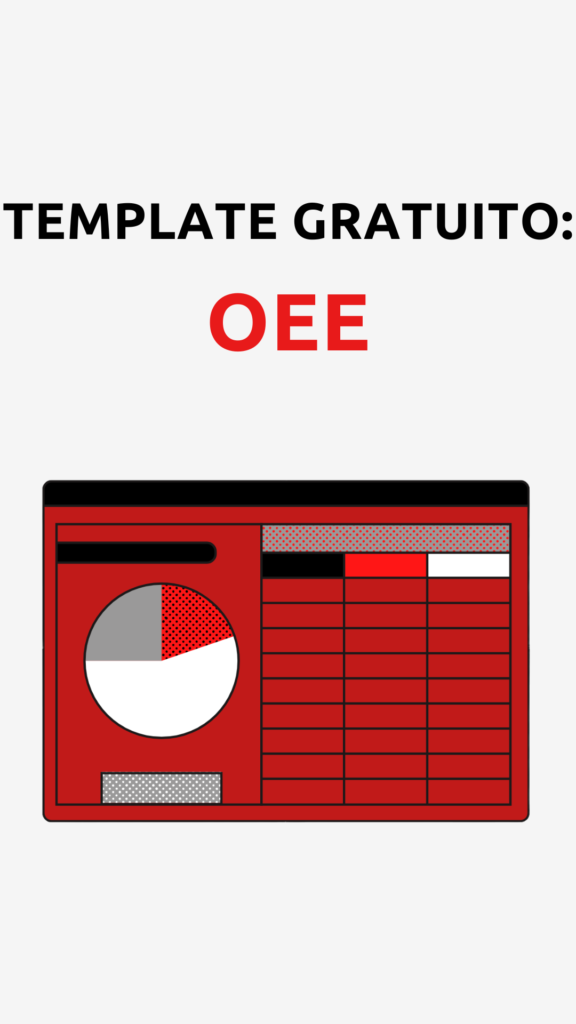
Conclusão
Embora o tempo necessário para a implantação completa de um programa TPM exija ações de longo prazo, a partir das primeiras etapas do trabalho alguns resultados aparecem, o que gera o estímulo necessário para a sua continuidade.
Reduções de custos de manutenção (materiais e tempo dos manutentores), aumento gradativo de OEE e MTBF e redução concomitante de MTTR acontecem ainda nas fases iniciais do programa.
Os maiores desafios se referem às dificuldades em capacitar adequadamente operadores para que eles, gradativamente, assumam as tarefas mais simples de manutenção e detecção de anormalidades. Em empresas com alta rotatividade de pessoal, estas dificuldades aumentam.
A integração de esforços e ações entre os times de manutenção e produção também é um ponto fundamental para assegurar o sucesso do programa.
A realização de auditorias regulares, para monitoramento dos resultados, também deve ser rigidamente controlada, em especial nas fases iniciais de implantação.
O início do programa em uma área piloto é uma estratégia interessante que permite acumular conhecimento e experiência, que serão valiosos quando se optar por sua disseminação em toda a organização.
Nos acompanhe também no Instagram, Facebook e LinkedIn para ficar sempre por dentro das novidades.